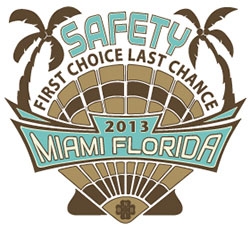
82nd General Meeting Speaker Presentation
Anatomy of a Catastrophic Boiler Accident
By David Peterson
The following presentation was delivered at the 82nd General Meeting on Monday, May 13, by David Peterson. It has been edited for content and phrasing. To follow along with Mr. Peterson’s slide presentation, click here.
Introduction:
David Peterson is a machinery and equipment specialist for the Cincinnati Insurance Company which serves clients in northeast Ohio. Mr. Peterson began his career in 1972 when he enlisted in the US Navy. He served for 20 years and retired in 1992 as a master chief boiler technician. During his naval career, Mr. Peterson devoted 11 years working at ship repair facilities. In 1985, he completed formal training and qualified as a steam generating plant inspector, which is the Navy equivalent of a National Board inspector.
Upon leaving the Navy, Mr. Peterson acquired his National Board commission and has worked as a boiler inspector for various insurance companies. Mr. Peterson wrote an article in the BULLETIN that was published in the summer 1997 issue entitled Anatomy of a Catastrophic Boiler Accident. In his presentation, he revisits his article and shares some of his more recent thoughts and observations.
Mr. Peterson:
Back in 1997, I submitted a paper to the National Board BULLETIN about a boiler room accident that I experienced while I was in the Navy. I have come here today to share that story again and hope to show how that experience made me a better boiler inspector.
Let's begin by reviewing some of the facts of the events that led to this accident. On August 2nd, 1990, Iraq invaded Kuwait. A few days later, Iraq forces controlled Kuwait and declared Kuwait to be a providence of Iraq. Thus begins an armed forces build-up that would later become Operation Desert Storm. Toward the end of August 1990, a large number of US Naval ships began deploying to the Persian Gulf. Included in the ship deployment was the USS Iwo Jima, LPH-2.
The Iwo Jima, commissioned on August 26th, 1961, was an amphibious assault ship designed as a helicopter carrier that carried approximately 2,000 Marine ground force troops. During mid-October, the ship started experiencing problems with its engineering plant, and the decision was made to send the ship to Bahrain where it could go pierside and shut down the boilers. Among the various pieces of equipment that were going to be repaired during this in-port period were main steam valves 1-MS7 and 2-MS7.
The ship's engineer suspected steam leaked by one or both of those valves, thereby preventing two-valve protection to be achieved. A two-valve protection is required to perform routine maintenance on a boiler while the other boiler is in operation. The Iwo Jima arrived pierside in Bahrain on October 25th. On October 28th, a pipefitter from the Bahrain Shipbuilding Engineering Company arrived and began work on these valves.
Both of the valves and their bypass valves were disassembled by removing all threaded fasteners which held the valve bonnets to the bodies. After disassembling the valves, the Iwo Jima's chief engineer inspected each valve. The bypass valve for 2-MS7 was found with some defects in the seating surface, while the other valves did not have any visual steam cuts, cracks or other flaws. The pipefitter was directed to repair the seating surface on the bypass valve by lapping it in with grinding compound and to reassemble all the valves.
The Judge Advocate General (JAG) investigation report from this accident said that the pipefitter completed reassembly of these valves and departed the ship at approximately 7:00 p.m. on October 28th. At 2:00 a.m. on October 30th, fires were lighted under number one boiler in preparation for an 8:00 a.m. underway time. Everything appeared to be just in routine light-off watch.
The number two boiler was lit off at 5:30. And by 7:30 both boilers were online, and the engineering officer had reported that the engineering department was ready to get underway, or in Navy jargon, ready to “answer all bells.”
The ship set the special sea and anchor detail, and this comes into play in this story quite a bit. Because when a ship is entering or leaving port or an otherwise hazardous navigational situation, additional equipment is operated and additional controls are assumed by the ship's bridge. The engineers in the boiler room can't take action on their own.
On the USS Iwo Jima, the number one ship service turbine generator, which was located in the boiler room, was designated as the standby generator. Main steam valves 1-MS7 and 2-MS7 were stop valves that provided directed steam to this standby generator. Therefore, just prior to the ship getting underway, these valves were open to start number one generator as a normal part of sea and anchor detail.
The ship got underway at 6:56 a.m. that morning. Very shortly after the ship was underway, valve 2-MS7 started leaking. Within moments, the valve was leaking very badly. The boiler room personnel reported to the engineering officer in the engine room, which you can refer to as main control, that they had a major steam leak behind number two boiler, and they requested permission to secure number two boiler.
At 8:11 a.m., main control reported a major steam leak to the commanding officer on the bridge. Before the commanding officer could take any action, the bonnet completely blew off the valve, dumping steam at 600 psi and 850°F into the boiler room. Immediately the ship lost all propulsion power and electrical power and was dead in the water.
The emergency generator started and the ship regained some electrical power, but could not maneuver. The ship went to general quarters, and at approximately 8:35 a.m., a repair party entered the boiler room to investigate for damages and search for survivors. Ultimately, all 10 of the crew members who were in the boiler room during the accident died as a result of the accident.
Four of the crew members managed to escape the boiler room, where they were transported by helicopter to a Navy hospital ship. The other six personnel were found dead in the boiler room. At 11:30 p.m. that night, the last survivor passed away aboard the hospital ship Comfort.
I will try to describe the events to you and give you an idea how it felt to be down there that day. The light-off watch had been routine. There was no indication that anything was amiss. As the number one generator was being prepared for operation, the bypass valves on both 1-MS7 and 2-MS7 would be opened to warm up the piping and drain any condensate. They would then start to roll and warm up the turbine. Shortly before the ship was to get underway, these valves would be fully opened and the generator would be placed in operation and paralleled with the number two generator.
Shortly thereafter, the bonnet to the body valve flange joint on 2-MS7 began the leak. Within minutes it was a major steam leak and getting worse. The boiler room operators were frightened, and their instincts were telling them to shut the boilers off and get out of the boiler room. Of course, under normal operating conditions that's exactly what they would have done. However, the ship was at sea and anchor detail, and their training was telling them to continue operating until they received permission to shut down.
In a panicked voice, they reported to main control that they had a major steam leak behind number two boiler and requested permission to secure number two boiler. The phone talker in main control replied, “Main control, Aye,” indicating that he had received and understood the message. He then replied, “Wait one,” indicating that he was passing the word along and waiting for a response. That was the last communication.
Seconds later there was a loud boom that was heard all the way in the engine room. From that loud boom and the steam pressure gauges dropping, the chief engineer immediately knew what had happened. He ordered the main engine throttleman to open the throttle valve and try and drain as much steam out of the piping as possible.
Four of the boiler room crew members immediately ran to try and escape the boiler room. The other six crew members stayed and tried to shut down the boilers. It was reported that the main propulsion assistant (MPA) had positioned himself on the stairway leading to exit/entrance of the boiler room. I would assume that his primary motive was to keep anybody else from coming down into the boiler room. The MPA was a young officer in excellent health and physical condition, and he was already on the steps to get out of the boiler room, yet he could not escape the boiler room without sustaining fatal injuries. That fact illustrates how quickly the boiler room filled with intense heat. The men demonstrated exceptional bravery by remaining at their post as the steam leak got progressively worse.
This slide is a sketch of the layout of the boiler room. When we say main steam, in Navy terms, that meant superheated steam. They called superheated steam auxiliary steam.
The number one ship’s service turbine generator (SSTG) was located in the boiler room. There were two boilers. The ship had two D-type watertube boilers. Each boiler's normal operating pressure was 600 psi and 850°F at the superheater outlet. Each boiler was rated for approximately 250,000 pounds per hour.
Just past the main steam stop valve for each of these boilers was a pipe branch to route steam to the number one generator. The stop valves were 1-MS7 and 2-MS7 respectively. These valves were steel-gate valves of the outside screw and yoke design. The valves were approximately four-inch pipe size. The valves were butt welded into the piping system with the valve stem being in a horizontal position.
The valve bonnets were attached to the bodies by threaded fasteners with a spiral round compression gasket to seal the two pieces. The valve bodies were drilled and tapped. Studs were screwed into the valve bodies, and nuts were used to secure the bonnet. There were 10 fasteners installed to make this joint, and each of these studs was three-quarter inch diameter. Each of these valves also had a three-quarter inch bypass around them for warm-up.
This slide shows examples of what the valves looked like. The valve on the left looks very similar to what these valves looked like on the Iwo Jima. The valve on the right has the same bonnet-to-body type of joint where the studs are threaded into the valve body and just the nuts were instead of a bolt-type arrangement.
At the time of this accident, I was a master chief boiler technician assigned as the boiler inspector for Amphibious Squadron 12. The Iwo Jima was one of the ships in the squadron. A few days after the accident, I was on an airplane bound for Bahrain. Although it has been 23 years since this accident, I can still vividly remember aspects of my time aboard the Iwo Jima.
Shortly after I arrived, I was having coffee in the chief's mess and talking with Senior Chief Johnson, who was the engineering officer of the watch for that morning's light-off. Shortly before the ship set the special sea and anchor detail and about 30-40 minutes before the valve blew, he had taken a tour of the fire room. He became emotional as he described a conversation that he had with one of the young watch standards who was down in the fire room. This guy was approaching the end of his enlistment, and he called out to the senior chief as he walked by, “Only 40 more days to go, Senior Chief.”
I also remember a conversation with the lone survivor of this accident. BT-1 Hamilton, the oil and water king, had started down the ladder to draw water samples. As he was climbing down the ladder into the fire room, the main propulsion assistant screamed at him to get out of the boiler room. He had no more than exited the boiler room when the valve blew. I remember him saying to me that if he hadn't just been distracted by a 30-second conversation on his way to the boiler room, he might have been walking into the disaster instead of running away from it.
Of the people who perished in this accident, I only knew one of them personally. BT-1 Robert Bolden was the boiler technician of the watch, or in Navy jargon, the “top watch” that morning. We had served together aboard a destroyer, the USS Coontz from 1982 to 1984. In 1983, the Coontz underwent a one-year overhaul at the Philadelphia Naval Shipyard. Bob and I drove from Phillie to Norfolk many times that year to visit our families over weekends. Bob was a devoted husband and father of two daughters. He was also a very good boiler tech, and he died bravely, following orders, and trying to operate the boiler plant in a manner to which he had been trained.
It's virtually impossible to describe the way I felt when I entered the boiler room for the first time. Normally, a boiler room has many contrasting colors. However, the Iwo Jima boiler room was a very eerie white color. This was because the velocity of the steam sandblasted all the pipe insulation from nearby pipes, and that insulation was evenly distributed throughout the boiler room into almost every crack and surface.
I could picture the terror the operators felt as they desperately tried to shut off the boilers and escape the heat. Quick-closing valves were installed to be able to quickly shut off the fuel oil pumps and quick-closing valves at the fuel oil supply headers. The boiler room operators had pulled these quick-closing valves so violently that the steel cables were broken on every one of them.
The main steam stop valves for the boilers were manual to open, but they had pneumatic motors that could remotely close them for emergency. However, when the bonnet blew off the 2-MS7, it sheared the hoses providing air to the pneumatic motors, so the main steam stop valves did not close.
Beyond the impact of feeling what the operators must have felt in their final minutes, I began assessing what a mammoth undertaking it was going to be to get this boiler room operational again. We had to disassemble and clean all the electrical switch gear and many pieces of machinery. Thousands of man hours were expended on this project. The Navy brought a tender to Bahrain to do the majority of the repair work.
Once the repair work began winding down, our work shifted to training the replacement crew members and building their confidence in the boiler room. Many of these crew members were very young and they had seen their dead or injured friends, and a lot of them were scared to death to go back in the boiler room.
One of the hats that a Navy chief petty officer wears is that of counselor. I had many long heart-to-heart conversations with these young men asking them to trust that I would make sure everything in the boiler room would be safe before it was restarted; everything imaginable would be inspected and tested; and then tested again.
Ultimately, the cause of this catastrophic accident was the installation of nuts of the improper material installed in the valve body to valve bonnet joint. The pipefitter from the Bahrain Shipbuilding and Engineering Company that performed the work was Pakistani and he didn't speak much English. As he was preparing to reassemble the valve, he thought the existing nuts were corroded and he wanted to replace them. It was stated during the JAG investigation that he asked one of the ship's crew members for new nuts, and was told to look through the boiler room's spare parts bins. The nuts he chose to install were made of brass. The nuts chosen and used by the pipefitter were not visibly distinguishable as brass because the manufacturer had applied a black oxide coating to them that gave them the appearance of ferrous metal. This was a problem long before this accident.
There were many times when I was a boiler room supervisor that one of my subordinates would try to use these black brass nuts on a steam piping job. Like Gibbs on the TV show NCIS, I would slap him on the back of the head and explain to him that they were not suitable for steam piping.
During normal operation, valve 2-MS7 would be closed because its purpose was to provide steam for the standby generator. As steam at 600 psi and 850°F began flowing through this valve, the brass nuts were expanding at a much greater rate than the steel studs, quickly losing the strength to secure the bonnet to the body. After less than 30 minutes of operation, this valve catastrophically failed.
One thing to think about: the reasons why this actually happened were 1) the ship was at sea detail and 2) this was a normally closed valve. Had this been the same repair to a normally opened valve, they would have found it earlier in the light-off process and been able to isolate it. In that case, it would have been just another near miss. All of us being safety professionals, we know that for every tragic accident that kills or injures or makes headlines, there are thousands of near misses.
So what kind of nut should have been used? I remember from my Navy days that any time I was working on superheated steam components, any threaded fasteners had to be ASME/ASTM Grade B-16. These studs and nuts had distinguishable markings on them identifying them as Grade B-16. When I started working to put this presentation together, I thought it was going to be simple to find this information. I searched for weeks before I found this. If I am remembering correctly, the studs would have B-16 etched on the flat surface of the studs, and Grade B-16 nuts would have a raised letter “H” or possibly a letter “B” and the number four on the face of the nut.
The letter “B” identifies the nut if it was being made from bar stock. The letter “H” identifies the nut as being heat treated. And then the letter identifies the grade of steel. A nut marking of 2-H identifies a heat treated nut made of carbon steel. A 4-H nut is a heat treated nut made of carbon alloy steel. The brass nuts used during the repair to 2-MS7, while black in color from the oxide coating, had no identification markings on them whatsoever. In the case of the repair to valve 2-MS7 on board the Iwo Jima, the use of any type of steel nuts would have been preferable to the use of brass nuts. The use of an incorrect grade of steel might have shortened the time period before another repair to the valve was required, but the valve probably would not have failed catastrophically after less than 30 minutes of service.
The JAG investigation determined that the required quality assurance procedures had not been followed, specifically the type commander QA manual. In this case, that would have been Commander, Naval Surface Forces, Atlantic (COMNAVSURFLANT). And the QA manual specifically listed main steam components as being QA Level 1. This meant that all materials, including threaded fasteners, had to be positively identified as meeting the required specifications.
The initial charges being considered by the JAG investigators were manslaughter. However, these charges were never filed, as no willful negligence was proved. The ship's commanding officer received a letter of reprimand. He was on his way to admiral. The chief engineer was relieved of his duties and permitted to retire from the Navy. The main propulsion assistant died in the accident. The boiler technician chief petty officer was relieved of his duties and was discharged from active duty. Less than two months after this accident, the Iwo Jima was repaired and was underway continuing with Operation Desert Storm assignments.
However, before I left, I made a vow to myself that I would make every effort to never again be involved with an accident like this one. With that said, I truly hope that sharing this story reinforces how serious and important our jobs are in this industry. Many people in the public depend on us for their safety. It is especially important in today's environment of cost-cutting and increased profit margins that safety not be sacrificed. The National Board, ASME, and jurisdictional authorities all provide many excellent codes and standards and are available for all of us, just as sufficient written standards were available on board the Iwo Jima. But these are just written specifications that by themselves don't hold water or steam. Therefore, it's up to boiler inspectors to thoroughly conduct our inspections and uphold these codes, because many people are counting on us.
We must strive to stay abreast of changes in our industry and to ask questions if we are not sure how or why something is being done. In most cases, when something doesn't look right, it's because it's not. When I was asked to speak before this group, I was asked to try and conclude this presentation with a "moral of the story" type of ending. I guess the moral of this story is: if something doesn't look right to you as an engineer or a boiler inspector, it probably isn’t, and you need to question it.
I have been working as an insurance boiler inspector for a little over 20 years. I am always surprised at how often I have heard fellow boiler inspectors make comments like, “If you make a recommendation, you had better be right.” I would urge you not to question your training, qualifications, and experience. I don't think I can count the number of times I had boiler owners tell me things like, “My previous boiler inspector never said anything about that condition,” or “my previous boiler inspector never made me pull drum internals or remove those hand-hold plates or open that area of the boiler.”
The NBIC clearly says that all areas of the boiler are to be examined during an inspection. A first-year boiler inspector would probably recognize that it doesn't look right to see every hand-hold plate seal-welded into the various headers of a power boiler and all those areas of the boiler inaccessible to inspection.
During the JAG investigation on the Iwo Jima, it was never officially determined that an inspection had been made to valve 2-MS7 after its reassembly. However, based on my experience in operating Navy boiler plants, I can almost guarantee that somebody looked at that valve, even if it wasn't a formal sign-off type of inspection.
If somebody had looked at that valve, it's possible that they said to themselves, “those nuts don't look right.” They might have thought for a moment that maybe they should tell somebody. Then they might have thought for a moment, “I don't want to look stupid. I'm sure that pipefitter knows more about this than I do. It has to be all right.”
That's the thought I want to leave with you. If something doesn't look right to you, have the conviction to question it.