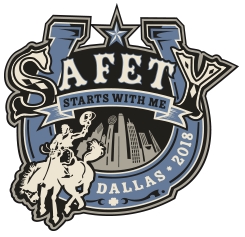
The 87th General Meeting Speaker Presentation
"Pressure Relief Device Investigation Testing – Lessons Learned"
Joseph F. Ball, P.E.
The following presentation was delivered at the 87th General Meeting Monday General Session, May 7, 2018. It has been edited for content and phrasing.
INTRODUCTION: Joe Ball is the director of the National Board Pressure Relief Department. He is responsible for pressure relief device new construction and repair certification programs, and test lab operations. He is also responsible for the conduct of shop reviews of valve and rupture disk manufacturers, assemblers, repair organizations, and test laboratories, and is an ASME Authorized Observer for the National Board Testing Laboratory.
Mr. Ball is a professional engineer in the state of Ohio and is a National Board instructor for IC and VR courses. He is a member of the ASME Section XI and the General Requirements Subgroup and Working group. He is a member of the ASME Section XIII Committee on Overpressure Protection, and is the chair of the Section III Working Group on Pressure Relief and a member of the Subgroup on Component design.
Mr. Ball's slide presentation can be accessed here.
MR. BALL: Thank you. I want to thank Mr. Douin for encouraging me to put this talk together. I have had one other opportunity to speak to the group, and a chance to come back is really an honor.
The purpose of this presentation—we will look a little bit at some of our testing procedures and how we organize the test for investigation.
One of the things we always want to keep in mind is that a lot of this investigation testing represents accidents, accidents where equipment has been destroyed and where people have been injured or killed. So it's an important thing. We want to be serious about it as well.
We are going to look at the testing process and some of the results we have obtained. I looked through quite a series of tests to compile some data, so we will look at that data a little bit and what we’re learning from this.
When we do an individual test, there is information that goes back to the jurisdiction, typically, or whoever the investigating organization is. They use that to figure out what happened in their particular case. But are there bigger picture things that we can take from that test and apply that more generally so other people don't have that same kind of a problem? That's what I call my lessons learned, and that's where we are headed with this.
The purpose of our testing is to assist National Board members, our primary customers, but we also assist inspection agencies and other organizations. We have done some work for forensic engineering companies and outfits like that, when there have been investigations. What they are trying to find out in most cases is what the pressure relief device's contribution was to that particular accident.
We also have looked at some examples where somebody has identified a potential problem with a pressure relief device. We are a certified organization. We want that equipment to function properly. If there is an issue with it that we identify through an investigation test which may cycle back to the manufacturer, they may have to do something about that particular product. So we are looking at it from that side as well.
And then as a side benefit, those issues, if we find any during testing, give us some guidance to address and avoid problems elsewhere, because that's really where we want to go with this.
We are not a forensic engineering laboratory. We are not going to take a pressure relief device apart, analyze the material or the metal or something like that. We do just a small part of the investigation, so there are other people that look at metallurgy and welding, and how the equipment was operated.
We are doing a test that compares the performance of that pressure relief device to the standards it was originally built to. Primarily the ASME Boiler and Pressure Vessel Code is our standard. What anticipated performance should that device have, where should it open, and what capacity should it have? That's the test that we are doing.
We do a very detailed physical inspection when we receive the equipment as well. First we are just looking at it for its mechanical soundness. We don't want to put any piece of a device that's suspect on our test stand. Our first goal, of course, is safety for the people witnessing the test, and the people working on the test. So we do try and look at that. Oftentimes that physical inspection tells you a lot about what the potential outcome of that test will be. Later on I have some pictures of the bad stuff, but look at the valve. If it's full of rust and corrosion, or it's physically, mechanically damaged, that tells you something, and the investigators can use that information then to help them figure out what happened in the accident that they might be looking at.
We have test procedures that we develop. They are based on an ASTM standard E-860, Standard Practice for Examining and Preparing Items That Are or May Become Involved in Criminal or Civil Litigation. It's a pretty basic procedure. It's not how to test pressure relief devices. It's generally how to test things where there are multiple concerned parties. It is more of a process on how to organize the testing than how to physically do it.
The basic principles are:
Document the condition of the items. What did we get, what did we receive for testing? Before we do anything to it, we want to really look at it very carefully, and this starts out in the field. So if you are looking at doing an accident investigation, you are looking at where that device was found, where it's located and what condition it is in before you even move it, if at all possible.
One of the questions is, “Has the item changed since the accident?” Did we have to remove it from the system? What did it take to accomplish that? That might be one of the questions that you'd have to look at to make sure you really understand what the test is ultimately going to show you.
If the test can change the condition of the item, notify all affected parties, and have those parties participate in the test and have the opportunity to see that.
And very often in pressure relief device testing, the test will change the device. It may be stuck. Once you put enough pressure to it, it's not stuck, but now it's going to perform differently. We give everybody the opportunity to see that test, and oftentimes you have one chance to accomplish that.
Perform any nondestructive tests prior to a destructive test. We try not to do any destructive testing, but potentially our performance test is going to change the condition of the valves. So everybody has got to have that opportunity to take a look at it.
Use an exemplar sample before we do the actual test. Sometimes we will do that to evaluate our test setup and procedure. Particularly we have done several rupture disk tests. You only get one chance to test a rupture disk. It doesn't reclose. So what we have done—and we've done this several times—we got a disk that was very similar to that one and did the test on that first. Then we put our actual sample in place and did the final actual investigation test, but after we had a chance to prove the test procedure.
Document the methods used and, of course, the results.
Maintain and label each item to protect and maintain its identity. We are very careful about traceability, about identifying the test sample. We do that with tags and marking and labeling and that type of thing.
Some practical concerns that ripple into pressure relief device testing are:
A lot of pressure relief devices are equipped with a test lever or test device of some kind, and one of our feedbacks to the investigators is don't touch that. People looking at that say, “Let's just double-check it and make sure that device is going to work.” Well, you may free that device up. Then the test is not going to give you an accurate answer. So what we do recommend is you take that lip lever, tie it in place by putting a zip tie or some wire through it or something like that, before you actually remove that valve from the scene of the accident, so we are getting a sample that hasn't somehow been affected.
We identify, document and preserve the inlet and discharge piping. The device itself might work fine, but we may have piping that's incorrect or improper. We are going to perhaps evaluate that as well. Sometimes you are going to have to end up cutting that off, so you need to get a picture of it before you actually disassemble that in the field. That can be helpful to how the test is going to be performed later on.
Prevent any unnecessary handling, and package the valve well. Make sure it's not going to get bumped or anything like that when it gets shipped to the test site.
Our process—we start by getting our senior management involved. That's Mr. Douin. He's going to approve that. And what we do, we recognize this is serious business. There are a lot of people involved. There are potential legal issues that are coming up in some of the accidents. We want to be cognizant of that. We want to make sure everybody is on board before we go ahead and perform the test. We always notify all the affected parties. First, that comes from that ASTM procedure. It tells us to do that. But we also want to make sure someone can't come back later and say, “Oh, I wish I had had an opportunity to see that test. We might have made this suggestion.”
So we know that involves the owner and their representative. We always notify the device manufacturer. They are potentially going to have some legal issues later on. We are going to make sure we are right up front: Hey, your valve was involved in an accident. They are going to have an opportunity to look at it.
We will look at the valve itself. If we identify that it was assembled or repaired by another organization, they potentially could be involved. We would have the inspection agency involved since that's the equipment that they insured. They are probably going to want to see that or at least be aware that that test is going to occur. All these people are contacted. We organize a test date and make sure everybody has an opportunity to come and see that test performed.
We develop what we call a special test procedure. It's called an STP. It's based upon our standard certification test procedures, but we adapt it to that specific item and how it may be used.
So we will try and look at what the MAWP of the equipment was. That is going to help us determine what the test pressure will be later on when we do a capacity test, for example.
When we receive the item, we do a detailed inspection. We have check lists for that. We look at the inlet and the outlet. We look inside of it. We take what dimensional measurements we can off of the object before we actually put it into the test process itself.
We take pictures of everything we do. I have some pictures here. Some of them are a little bit older, though, so they are not the highest technology.
We have a test procedure. It emphasizes the first opening. The question that people always want to understand is, “Where did that device open?” It's a little difficult to understand if that first test is truly representative of the performance, so you can have some discussions about that.
For our normal certification testing, we will test the pressure relief valve at least three times. We will get an average of that performance, and that is the average assigned for that particular valve.
But for an investigation test, you would think the first pop or the first opening of a valve is what was it was doing in the field. But what we can't always replicate, particularly on steam valves, is what the temperature of that device was when it was in the system. That can change the answer a little bit. But for the most part, that first opening tells you most of the story. And I have data on some of our test results.
Then we will do a capacity test. We tie that again to the pressure vessel that was being protected. For example, if it's a vessel set with a MAWP of 100 and the user would have expected the capacity to be at 10 percent above that for a Section VIII valve, then we build our procedure around where that device was going to be used.
That procedure is distributed to all the test participants. They have an opportunity to comment on that. That way everybody is on board before we do the test process and understands exactly what is going to occur when that test is done.
We receive the test object. We sometimes are asked to maintain a formal chain of custody because there are often legal issues associated with that, so we will have some way to have traceability of when it was shipped, when we received it, and who received it. We do the same thing when it goes back to the owner or whoever that device has come from.
We will do that physical inspection, then go ahead and conduct the test.
But as I said, personnel safety comes first, so we do have a few items that—and I went through my test records—there are some things we looked at and said, “Sorry, we just can't test that.” It's damaged beyond any reasonable condition, and we are not going to risk ourselves to do the test if we don't think we are going to get good information and we can do it safely.
When we are done, we have a report that's distributed back to the test sponsor. That usually is the jurisdiction, and then whoever else they designate that it goes to.
We get a chance to be a little creative in some of this work, though, so it's a little surprising what can actually be tested. Our normal test procedure on steam requires we pipe up the discharge to measure the capacity. This top outlet valve doesn't have a discharge port; it just exhausts directly to atmosphere. So what we have is a big canister. Essentially it's a giant “T” that the valve goes inside, and we capture the steam and send that on into the test system. So we have some different variations that we can do there.
This is a valve where the inlet threads were damaged, and actually that valve was physically broken off of the piece of equipment that was in the accident. It would be nice to understand how that valve was performing. So we put together a little test assembly. This is essentially two flanges. We clamped the valve in position so we didn't have to use the inlet threads. After we checked it for pressure tightness, we put pressure to the inlet. We couldn't measure capacity under that situation, but we could measure performance.
And in some cases, we have had several examples like this where we could actually measure the set pressure characteristic of the valve even though the valve itself had been broken off during the accident.
Here is a valve we received with some pieces of the piping. So there is an elbow on the inlet. That is not a preferred installation position, but this is how that valve had actually been used in service. Normally with an inlet like that, particularly a short radius elbow, there is a lot of pressure drop associated with it. That would not be the best way to use that valve. But that's how it was installed; that's how we tested it. It also happens to have an elbow on the outlet to direct the discharge pipe up, which is a little more common. But we tried to test it as close as we could to the actual as-found condition.
Most of what we test are pressure relief devices, but since we have pressure sources, pressure measurement capabilities, and flow measurement capabilities, we can also take a piece of pressure equipment that was involved in an accident, hook it up to our equipment, and generate some useful information that's beyond pressure relief devices.
We have done an excess flow valve. That's a valve that you normally have on a propane tank. The hose that's used to fill up the tank will have a valve, which will shut off if that hose is ripped off as the flow rate increases. It's sort of the opposite of a pressure relief valve. They call them ride-away accidents. The truck leaves, and they forget to unhook the hose. An excess flow valve should shut when it senses that increase in flow. We put it on a flow meter and measure the capacity at which the valve will shut off.
We looked at an autoclave. It had a whistle that was supposed to tell you there was pressure between the door and the vessel when the door was being opened. It looked like a big steam whistle. We developed a pressure source and measured how loud that was as part of the investigation.
We've done some pressure switches and pressure gages. We calibrate pressure equipment all the time. We can take a pressure gage from the accident and put it on our equipment and see how it’s reading.
You have heard probably several times over the years about the Medina steam traction accident, in Ohio, very tragic. We did the steam injectors from that. Those are steam-powered pumps. They actually did work. The pressure relief valve did not.
In one case, somebody asked if the safety valve had gone off, would somebody have heard it, and there was some question on valve performance. We measured sound level so that we could tell you what the performance was, but also, yes, you probably would have heard this 126-decibel valve go off in your factory.
Test attributes—we look at where the valve first starts to leak. In most cases, it is pressure relief valves. We look at the initial set pressure measurement where the valve recloses. We may do a complete sequence of several pops to see if that changes any. Particularly for the steam valves, it will tell you if it was warmed up properly or not.
We will do a capacity test. When we do that, we are bringing the pressure up, so we see where it opens again and where it recloses.
We have done a couple cases where we just measure the lift. If either it's a very large valve, or we don't want to have the valve under pressure for a really long period of time, we can do a lift measurement. That tells us mostly what the capacity would be.
We have done testing, and then we may add additional test cycles. We will put on the piping that we found, see how that might have affected the performance, things like that.
When I did look at some of this data as I went through a whole series of tests, I was surprised we had 97 different tests since 1991, and there is no relationship to time. We keep having pressure equipment accidents. So what people do here is important because there is still stuff that's going wrong.
I tried to look at this data, some different trends, and what type of equipment we tested, and tried to summarize it a little bit.
Let’s start with code sections. About half of what we did was either Section I or Section IV, pressure equipment. I'm not sure what this tells us about the state of that equipment. I think most jurisdictions regulate boilers and heating boilers quite a bit, but there is a little less regulation on the pressure vessel side.
We had a few non-code items. We are not in the non-code business. We are in the code business, but we had several cases where the jurisdiction that was very knowledgeable about pressure equipment essentially had loaned their services to some other state organization. In most cases, it was an OSHA type of group, where they were concerned with worker safety. They had a pressure equipment accident, and they went to the people in their jurisdiction that know about pressure equipment. That's the boiler and pressure vessel group. And so we did a valve on a water tank and another valve that was on a low-pressure vessel, not normal code stuff that we deal with. But that's helping out. That department is trying to help out their safety group.
About half the tests were steam. The other half was air. A couple water valves were thrown in there. We had a few that we did on both water and steam. Because there was some question about how that valve was being used at that particular time, we checked it on both fluids.
About a third of the types of devices tested were safety valves. Most of the rest were safety relief valves. That's your Section VIII stuff, but that also includes a lot of the Section IV hot water boiler valves, and a few other oddball things there. We did a T and P valve and some rupture disks. Others were a couple of excess flow valves, things like that.
Now we get to some of the lessons learned. So what is all this telling us?
There was a valve from a large chemical plant that had had an explosion and a fire. The valve had some kind of burn marks on the outside of it. It was pretty heavily mechanically damaged. The inside of the outlet had a plastic type of substance in it. I didn't think that valve was going to do anything, but it did perform. It wasn't within tolerance or anything, but it opened. It seemed like that valve was doing its job. But as we were having discussions with the different test parties, a guy asked me, “Well, I see what the valve did, but if there was something that was in the outlet that looked like a giant plastic football stuffed in there, would that affect the performance?”
I said, “Yeah.”
He responded, “Well, before we brought it down here, we chipped it out. So it didn't fall out. It was mechanically removed.” And what it turned out—this was a plastics processing plant—they had a number of relief valves that all discharged into a common manifold. There had been an overpressure condition. That fluid always went both ways in the pipe. The fluid that was discharged, which was this plastic, had melted. Molten plastic had gone back up the pipe and gone into the outlet of the other valve, and it was plugged up. So no matter what it did on our test stand, the important piece of information that originally was missing was that there was a big thing that looked like a football stuffed in the outlet. So on my test notes, I write down valve probably would not have worked with a big plastic thing that—I didn't say it looked like a football, but . . .
So it's important to understand the condition of it, understanding exactly how it came out from the field. Taking that big plug out of the outlet probably changed its performance a little bit. I made sure that was prominently captured in our notes.
Application of pressure relief devices is important, and they are designed for a certain service. We want to make sure they are used that way.
We tested a valve that was involved in a release of ammonia in a refrigeration system. We tested it as it's listed on the nameplate. We get it all done, and they say that the valve was on the liquid line. It's a gas-certified valve, so I can't really tell you what its liquid performance is. The valve was misapplied. It was not in the service that it was actually designed for.
We had an asphyxiation accident, very tragic. An individual was killed by a nitrogen release in a small enclosed area, and they were concerned about the valve leaking. We received the valve and did a test. As a code pressure relief valve, it was fine. The valve which you would normally see on an air compressor is just designed to discharge to atmosphere. There is no port that you could put a discharge pipe into. It doesn't have a threaded outlet or anything like that. And what I think probably happened is the valve had actually popped off in service. And it was a small instrumentation, like an instrumentation booth that you would have on a pipeline, and they had a regulator or something like that. That room filled up with nitrogen, but the valve’s job is just to protect against an overpressure condition. It should have had a valve with a discharge—pipe it out to a safe location where it's not going to obviously affect somebody who was around it.
The audience is inspectors. Periodic inspection and maintenance are important. A lot of the devices that you see for sophisticated users have programs to remove them and do a pressure test once in a while. That's certainly good practice. A lot of the valves that you see in most situations have little maintenance and things that go on. It's that boiler inspector out there doing your annual certificate inspection that's probably one of the few people who looks at that.
There was a valve for an air compressor, so it had the little pull ring on it. You pull that and it tells you if that valve is stuck or not. The valve was actually rated like 125. We took it up to 180. Finally it opened, but if you looked in the inlet, that thing was just plugged solid with some kind of debris. After that went through it was open. Now it was actually not working. It was leaking. But if somebody had checked that valve in service, they would have said that this is wrong. It needed to be replaced. It was about a five dollar valve, and it took an air compressor apart.
There was a 200-pound valve. The first opening was 234 psi. It dropped off a little bit after that, but my question is, “Would an inspector have flagged this?” Well, they very dutifully painted the compressor, and they went ahead and painted the pressure relief valve. What I think happened was the paint was all stuck on the stem. It basically glued that thing together. And just by the general condition, I didn't need to test it to tell you something was not quite right with it.
So here are some random inspection notes. We have test data that we have obtained, but we make notes when we see things.
We had a valve built in 1967. I can tell that from the date code. It's over 40 years old. It actually still worked, but the expansion tank on a heating boiler came apart. That's a really old boiler that probably hadn't been looked at. Seals were missing. The seals didn't match the manufacturer's name, somebody has tampered with it. The valve was thirty years old. Masking tape was on the bonnet vent, so the valve chattered. So basically they put it into service with the shipping plug still on it.
An inch-and-a-half valve on an inch-and-a-quarter connection, that's a very basic code violation. It didn't quite meet its rated capacity. We put it on the correct connection, and it worked the way it was supposed to.
A 150-psi valve didn't open at 201psi. When we do this test, at some point, we are bringing it up, you kind of get a little nervous, and you just say, “Stop.” That's a valve that was declared stuck, but it was almost 20 years old and really corroded. We put it under pressure, and the lift lever didn't move the thing at all. That tells you the valve was stuck shut.
A Section I valve on a five-and-a-half-foot-long inlet pipe. It should have been about five inches long for whatever size it was, and they said that the valve is damaged. Yeah, it's damaged because it was chattering because you had a huge long inlet pipe. Any inspector should have caught that.
We had several valves that we tested where there was a complaint that the lifting lever was not making the valve function, and they said that the metal part or the lifting lever was bent. And this is an inexpensive valve. We put it on the test stand and take it up to the Section I requirement, which is 75 percent of the inlet set pressure—or the set pressure. We opened the lift lever, and it worked fine. My conclusion was —and there were several of these—that people were testing the valves without any pressure under them, which looks like they’re not working, but it wasn't the valves' fault. The valves worked fine.
The majority of the accidents, where we have tested the pressure relief device, did not happen because the safety valve did not work. The corollary to this is people said the boiler blew up because the safety valve didn't function. Well, that's just not true. Something had to cause the pressure to increase, first of all. But what I tried to do is look at our actual record of the testing. I said before I had looked at 97 tests. Seventy-two of those devices did open. And my graph is the measured set pressure divided by the stamped set pressure. So if it's less than 100 percent, that means the valve opened low. If it's above that, the valve opened high. So you can see a great majority, 72 out of 97 valves, did something. These are all valves that had been in service. Some of them were high, some were low, but they did something.
And you kind of see some additional statistics with that. Some didn't open. So we had four that were just leaking, so something was coming out of there, but they obviously were not going to perform.
Seven were just stuck. We took them as high as we intended to go with them. We couldn't go any higher. And usually our cut-off is one and a half times MAWP. In some cases we didn't want to go quite that high. But they were stuck.
I had one that was plugged up, the air valve with the inlet all gummed up. Some were leaking from the get-go. There were a few that were no tests. Either we chose not to do that because it was damaged, or some were not applicable. And I had older notes, where I didn't always get all the details down.
So about 60 percent of the objects tested open at 110 percent of the set pressure or less. Seventy-three percent opened below one-and-a-half times. Kind of a quick thumb, that's your hydro pressure, more or less. Thirteen percent between 1.1 and 1.5 times the set. Some were high. That certainly isn’t what we would like to see. Two opened above that one-and-a-half times. Then we had 12 that were stuck or plugged up. So that kind of gives you an idea of the performance. These are all valves that had come out of service, so two-thirds of them actually opened, in some cases opened low. What that tells you is that the pressure equipment had some other cause of failure. It was not necessarily directly overpressure.
We were involved in the investigation of two autoclaves. They tested the pressure relief valves. The valves tested okay, which tells us that the vessel failed below set pressure of the pressure relief valve. And most of the accidents that we’ve seen with autoclaves (vessels with quick-opening closures) usually involve some issue with the door or how the lock mechanism works. We don't always see the details.
But the test of the pressure relief valve tells the investigator you did not have overpressure. You need to look at something else. And usually what they find is wear on the locking ring or locking mechanism, improper maintenance, or something like that.
We had a valve from a boiler tube failure. Usually that's low water condition. It wasn't an overpressure condition that caused the tube to fail. It was something else. The pressure relief valve test helped the investigators figure that out.
What I think comes out of this is that we don't always see the results of all of the complete accident investigation. We do our part and say, “Here is the result on the pressure relief device.” The investigators are looking at other things. They will look at corrosion, erosion, damage to the pressure equipment and stuff like that.
But I think most accidents actually have multiple causes. It takes more than one thing to go wrong for a pressure equipment accident to occur. One, was there an overpressure condition? If so, what caused that overpressure condition to occur? That's usually operational elements. The temperature control didn't work, the pressure control didn't work, or something like that.
Then the next question is, “Did a faulty pressure relief valve affect and make that accident worse because it didn't actuate?” Our test can tell you that answer.
Or were there any other defects or issues that adversely affected the pressure-containing integrity? That's a big question, and in most of the accidents, there usually is some other condition that is going to affect that pressure vessel.
We had one case where we were expecting to receive a valve that was on an air compressor. When it showed up at the lab, they needed a forklift. What do you need a forklift for? They sent the entire air compressor. And the compressor is kind of laying on its side, and there is a pressure vessel. It's the compressor that's mounted on the top of a pressure vessel. The kind of thing you see in your garage all the time. That pressure vessel was just laid out. It's wide open. They sent the whole thing.
So we take the valve off, we do our test. And I don't remember what the result was exactly, but while we are there, the representative says, “Well, here you might want to look at this, just more for interest.” You can see obviously where the vessel has failed, and it's bent. The starting point is in the middle. So wherever it came out, you look at the middle, and right there is a very large lap patch. So that's a patch that is just stuck over something that was leaking. So it already had a failure there. The lap patch was square, so we have stress risers at all the corners. It's field-welded on.
There are like five different things wrong with that. It's unauthorized, done by somebody who didn't have an R stamp or what they were doing, and it's very obvious from looking at where the failure initiated, where it grew, and when it went,it cracked where the patch was. Then that peeled open, a piece of metal came off, and somebody was injured. Unfortunately, it was probably the owner of the equipment who had done the repair.
Whatever that pressure relief valve was or was not doing—I think it might have been the painted valve—there was something else that contributed to that accident. The lack of knowledge, lack of proper repair techniques, all of that figures into ultimately what caused that particular accident.
So that gets me to my conclusion. Investigation testing is an important part of understanding why an accident occurred. Certainly it's not going to be the only element.
So you have to look at all things when people are doing those investigations—how the equipment was operated, serviced, repaired, and applied. All those things apply. Then we want to understand how the pressure relief device acted.
Hopefully with our test data, as well as the other lessons learned, we can use that information to avoid those problems in the future. That's really what we want to get out of this. You know, it's never good news to have an accident, but if we can take that information and avoid accidents, that's where we really want to go.
This is one of the services that we provide to the members. We actually do testing for other organizations as well. The difference is we don't charge the members. For our normal testing, the cost pays for the operation of the equipment.