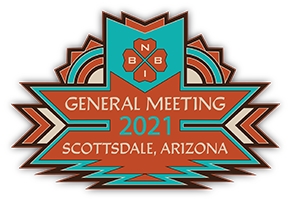
89th General Meeting Speaker Presentation
"Celebrating NBBI Milestones: The NBIC and PRD Test Lab"
Gary Scribner and Joseph Ball
The following presentation was delivered at the 89th General Meeting Monday General Session, May 10, 2021. It has been edited for content and phrasing.
INTRODUCTION: Since 2014, Gary Scribner has served as the National Board Assistant Executive Director – Technical. Prior to joining NBBI, Scribner spent seven years as the deputy director of Missouri. While a National Board member, Scribner was elected to the National Board’s Board of Trustees in 2009, where he served as second vice chair. The US Navy veteran continues to advocate for National Board safety programs.
Joseph Ball is the director of the National Board Pressure Relief Department, were he oversees pressure relief device new construction and repair certification programs, and test lab operations. He is also responsible for conducting shop reviews of valve and rupture disk manufacturers, assemblers, repair organizations, and test laboratories, and is an ASME Authorized Observer for the National Board Testing Laboratory. A professional engineer and National Board instructor, he chairs the ASME Section III Working Group on Pressure Relief.
Mr Scribner's slide presentation can be accessed HERE. Mr Ball's slide presentation can be accessed HERE.
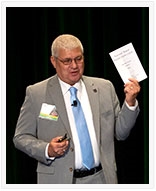
MR. SCRIBNER: Good afternoon. When I was asked to do this presentation on the NBIC – I have been involved with the NBIC for at least 15 years now – I thought this will be easy. I have only 15 minutes, 15 slides. But then I realized I had to go through 75 years of documents. Some of the old documents don't even have a table of contents in them. So, I read a lot of old stuff and tried to pull out the most important things as we developed the National Board Inspection Code to be the document and the industry standard for repairs, alterations, installation, pressure relief valves that we have today. We marked the 75th or Diamond Anniversary of the NBIC in 2020 - there was an article written by Luis Ponce that was in the BULLETIN. And this really takes everything full circle that it was in the BULLETIN, and I will explain that in a minute.
The BULLETIN itself – think about the time frame we were in, the mid-1940s – was approved in 1943. And at the time, there was no internet, there was no e-mail to let people know what was going on, and we had different titles for people. So, the BULLETIN was a mechanism to let the members and commissioned inspectors know what the executive director (at the time the secretary-treasurer) and the executive committee or BOT, and the National Board were doing for them. That was really the stated purpose of the BULLETIN, for the benefit of the members and commissioned inspectors. In 1945, they made an announcement in the BULLETIN that this new code was coming, but they introduced the first chapter of the NBIC.
So, the NBIC did not come out as a complete book. As it said in the BULLETIN, the first chapter was just the first installment, so it wasn't the first published version. We put this as an attachment in the BULLETIN back then, and you were asked to keep this, along with all the additional chapters as they came out and put them together for the first full NBIC. Chapter 1 was administrative, so it told who we were, what the purpose of the National Board was, and it actually had the Constitution in it at the time. So, it also covered NB-131, and 132 - the recommended rules for jurisdictions. This was early on, so this was the beginning of the NBIC. And here is just a copy of the actual book. This is a copy I made, so it's not the real thing. They'd get upset if I take that out of the library and travel with it.
As promised, over the next few years, the BULLETIN introduced the rest of the chapters of the NBIC. Laws and Rules, Chapter 2, Rules for Inspection of Existing Power Boilers, and so forth. I mean, you can read the different titles. And during this time frame, they also went back, just as we do today, a few of the chapters had things added to them, some were changed a little bit. No different than the process we really have today. But it took through 1949 to distribute the entire thing, and you notice the last chapter was Inspection of Fusion Welding.
ASME didn't have any regulations, and World War II was when welding really took off. So, that was a change. If you look in the ASME code back in the mid- 1940s, it gives you all these rules for riveting and says by the way, you can use fusion welding if you choose to.
In 1951, the first published NBIC was released, with all the parts together. The NBIC really stayed the same, just kept getting updated. Some of the chapters changed a little bit in time, but it stayed basically the same as far as the layout. Until in 1974, with one of the first attempts to make it an American National Standard Institution (ANSI) document. But this was denied, because up until this point, the NBIC was approved by the Executive Committee. The Executive Committee and the National Board staff developed this internally, and it was denied by ANSI in 1974 because it was not a consensus standard, which it is today. Understanding this denial, by 1975 the first Consensus Committee was formed, and it was from the industry: we had AIAs, we had manufacturers involved. So, we were working down the road to become an ANSI accredited document.
The first committee was only 12 people, it was one committee, and I found the name a little bit interesting: It's the Committee on National Board Inspection Code. They talked a little bit different back then, so I just found that interesting. And it took a little while, there were some other obstacles, but by 1983 we became an ANSI document or an American National Standard. And that's significant – we still maintain that certification. We are going through an audit right now as we speak. It takes about two months to go through the audit, but we intend to keep that going. In 1992 there really was a big change because we started coming out with annual addenda. The NBIC went from the little bound books to a loose-leaf binder to allow people to switch pages out every year. It was on a three-year cycle, but every off year, and sometimes on the actual year, you would get an addenda. You would go through, and it would tell you to remove page 53 and put a new page 53 in, and it would have the change in it.
The 1995 Edition marked some major changes. We did away with the chapters, and it was the first true reorganization of the NBIC. A lot of you in this room will be familiar with the old parts – RA, administrative, RB, RC, and RD. It was also the first attempt at an electronic version of the NBIC. You were sent a CD, and that was our first electronic version of the NBIC.
I get questions from the chiefs, so I wanted to point this out. The 2002 Addenda to the 2001 NBIC was really the first introduction of Appendix I, Installation Requirements. And it was only a couple pages. Over the next few years, that was worked on by a committee, that was not the official NBIC Committee, but developing what became Part 1 of the NBIC we have today.
And in 2007, we split the code into three different parts. We kept it in loose leaf, we still had addenda, but they put it in what they called a “suitcase” since it was getting bigger. The suitcase was to keep all the books together, supposedly, so you could put it in the trunk of your car. I think it only lasted for that 2007 Edition.
Also keeping up with the times, the electronic version was released on a thumb drive that could be mailed out to somebody. In 2011, keeping up with ASME code and trying to make things simpler with the editorial process, we went to a two-year edition instead of the three-year, and no addenda. We also went from loose leaf back to the bound book, just like we started originally.
The 2013 Edition introduced the first true electronic downloadable NBIC. So now you could either get a paper copy mailed to you, or you could come to us and you pay a fee and we would send you a link and, as you can today, get an electronic version of the NBIC.
In 2014, the 2011 NBIC was translated into Chinese and was the first true translation of the NBIC anywhere. I had the privilege to go over with John Burpee and Chuck Withers to China to accept the translations, so that was interesting to do. Looking at where in the world people were interested in this, we decided South America was really in need of the NBIC, so in 2015 we had the first Spanish translation. And it's the last time we translated it up to now into Spanish. So that was made available in Latin America.
In 2017, the NBIC introduced Part 4, Pressure Relief Devices, and there were really two mindsets when we did this change. We surveyed our customers, which are AIAs, the chief inspectors, commissioned inspectors, and everybody in the valve world wanted their own book, just as they do in ASME, and we have Section XIII starting to come out this year. But those inservice inspectors wanted their own book, and we realized going through this process that the PRD Committee was writing these things dealing with pressure relief devices in Part 1 and Part 2, but once they wrote that, the book was out of sight, out of mind. When we went through this process of making Part 4, there were over 25 code changes that affect the items that were in Part 1 and Part 2. So, they had to go back and do a lot of rewrites.
The trade-off ended up being that anything that's in Part 1 or Part 2 that deals with installation or inspection of pressure relief devices, that's repeated in Part 4, so it's in front of that committee at all times. If they change those parts, they have to do a corresponding change in Part 1 or Part 2 as appropriate. The rest of Part 4 dealt with accreditation programs, the VR program, and moved those requirements out of Part 3. The valves came out of Part 3, and it is strictly repairs and alterations to pressure retaining items. Special rules for pressure relief devices went over to Part 4, along with those installation and inspection requirements.
This is the key to the NBIC in our process: we have 14 different committees to develop the NBIC. It's the Main Committee, subcommittees, subgroups, task groups. There are over 125 dedicated volunteers that really make this happen. Some of these volunteers are on multiple committees. The 2021 NBIC is on track, it will be available July 1. There are over 100 code changes. We are working to get a presentation together for the October Chiefs’ Meeting that we will go over it with them, and for the AIA meeting for ASME we will be going over some code changes there.
And we have a nice, new bold look, a little bit different, but it also is very significant. We are a changing industry; this is no longer a male-dominated industry. We have a lot of women contributing a lot, we have had several presenters up here today, so the cover recognizes that. We have more and more female inspectors coming to Columbus to take both IS Commissions and AI Commissions every day. So, we thought it was important to recognize that.
Our next meeting is July 12 through the 15 at the Hilton Cincinnati Netherland Plaza Hotel, which is a unique, historic hotel. It will be a hybrid meeting. So if you are interested to see what the NBIC is all about, please register on our website, and you will be sent a link if you want to join through Zoom, or please come join us in person. For the members, when the NBIC becomes available July 1, we will provide each member with a paper copy, as we have in the past, and every commissioned inspector within your jurisdiction with an electronic copy, including the chief inspector.
Thank you for your time.
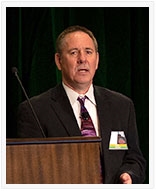
MR. BALL: It's a real honor for me to speak about what our group does and the 30th anniversary of the PRD Test Lab. And I've had the privilege to be involved with the lab all the way through that 30-year time period. But the real reason and the theme is what's the purpose of the lab, what are we hoping to accomplish by having that facility. And part of it ties in very nicely with the National Board Inspection Code. Because under the NBIC, we do have a program to certify organizations that do pressure relief valve repair, and as part of that they have to perform a demonstration test. So, they have got to take a valve, repair it, and make it work.
We are doing many tests associated with that program. Hopefully it's making that process better, as people understand what these valves are really supposed to do. So, I am going to try and tie the various testing, main types of testing that we do to what the benefits are to the membership and then ultimately the public.
Our background in pressure relief device testing really started at Ohio State, going on to the original National Board Test Lab, and then on to our – we say a new beginning, but it was really 30 years ago. I'll look at the interface then with ASME and National Board programs, which is the capacity certification process, test laboratory certification which supports that. The VR and testing certification are really to ensure pressure relief valve testing and repairs are done correctly. Then this just mentions investigation tests. We don't like to do those, but once in a while that does come up. And then get to our challenges for the future.
The National Board's original involvement in pressure relief valve testing was started in 1935. The National Board sponsored some tests for some different pressure relief valves, and they found that some of them were grossly underrated for their capacity. Some did not flow nearly what they were rated for in the nameplate. There really weren't any code rules for the certification of valves until those tests were done.
Recognizing some of those problems, the ASME code added a process to qualify a valve line, and that work was done at the OSU Robinson Mechanical Engineering Laboratory where they just had a steam facility. They did steam testing. It was done on the weekends. On the other side of the screen, though, it's a really neat object that I have gotten, I inherited you might say, but it's the log book from Professor Bucher who was the gentleman who ran that facility at OSU. And it's a little hard to see, but if you look through the list, that's it, every test that he did he meticulously documented. And there are companies like Watts, Kunkle, valve companies that are still around today, they are represented in his list of tests that he did. And I have the book, which I don't know how many tests were in it, but probably several thousand.
The other neat thing is he documents the cost of his steam. So, he had to buy the steam from the OSU power plant, and some of the test bills are as high as $10 or $20. Nothing we do today costs $10 or $20! Because it was used on the weekends, over time it was not very practical to stay there, so in 1974 the National Board built our own test laboratory. And you see behind the building, which is the lab itself, is a smokestack. That was by the Picway Power Plant, south of Columbus. They worked out a deal that we could put the lab there and receive steam from the power plant. So, we actually leased the land for the building. We added an air test system, which they didn't have before, and then a liquid system was added shortly after that.
Over that time, the code expanded. The original test was just a qualification test of the design, it didn't really look at the production side. So, there was testing of production samples added in the '76 code. So now a representative from an ASME-designated organization, which is the National Board, would go to the manufacturer's facility, we watch them put sample valves together, and those are supposed to be off-the-production-line samples, and those are going to go back to the lab for testing.
Assemblers were added. Those organizations received the component parts from the manufacturer, but they do the final calibration. That was really considered a code activity. It wasn't very well addressed until that time period. A test process was added for them as well, so they had to demonstrate their capability to make the valves function properly.
In '84, liquid valve certification was added. So, until then the code had just covered steam and air gas service valves. Over this time this was also making more work for what we did. This is from a very old, little pamphlet that we had to hand out and talk about the test lab. It's a little hard to see, but the big brass circle in the middle is the steam condenser. And those were World War II naval surplus ship condensers that were used to condense steam used to measure the flow from the steam valve. And then on the bottom picture, on the right side is a big silver tank. That was a weigh tank that started its life at the Robinson Lab, was used there for weighing the water from the steam system. And that was moved up to the current lab and is still around. It's just a big bucket, and it's been around for 60, 70 years now, still doing the same thing.
Over time we had some problems at the Picway Plant. They started using it for peaking. So if you had a really nice day, right in the middle of the day they didn't have a high need for electricity, and they would shut that plant down because it was kind of a smaller one in the grid. When you shut the plant down, then you get a cold day, the pipe would freeze. So, there was issues with the reliability of our steam, and we looked at adding a steam system down there.
The planning started for a new facility that would be closer to the main office, because this lab was 15 miles on the south side of Columbus. A feasibility study was done.
Your building can't just be a building – it has to symbolize something – so what does this symbolize? If you looked at it, it's supposed to be an arrow pointing toward the future. A new lab was built and in 1991 we opened the new facility. So, it started out at about 10,000 square feet. It included the laboratory and offices for all of the staff of the Pressure Relief Department: the admins, the engineers, the technicians. So, we had a place to kind of have one group all together, and at that point we moved out of the headquarters on Crupper Avenue.
In 1999, rupture disk certification was added to Section VIII of the code. Until that time, a rupture disk could be used in the same location as a pressure relief valve, but it did not have a code symbol stamp, there was no type testing or anything like that. That was finally added, so we had to build some rupture disk test rigs. They are flow-tested a little bit differently. We had to purchase a new air test vessel that was larger and had a nozzle on the side where those rupture disk test rigs would come out of. In 2011 we underwent a 3,000-square-foot expansion and added two higher pressure gas test systems. Previously we could test up to – we call it the 720-psi system. They added a 1,450 and a 2,500-psi system, so it really raised our gas testing pressures up quite a bit.
We changed our gas testing from air to nitrogen, switching to a liquid nitrogen system where the nitrogen is pumped up with two small pumps, raised to a very high pressure, and vaporized. And that is our current gas system.
In 2015 we upgraded all the boilers. They went from two steam generators to three. We’ve added a bunch of water treatment updates, things like that, to really upgrade the steam systems and put a lot of automation in there.
And it's kind of neat, there is a picture on the left from when the first lab was built – or the current lab was built. Brand new, the floor is all shiny. And then on the right is the current lab. And just like anybody that's lived in one place for a long time, we've got a lot more stuff than we used to have, and all the paint colors have changed. But some of the original equipment is there. Some of the vessels have been changed, the control valves have been changed, all the data measuring stuff has certainly been changed, and the lab staff have done a lot of work on really updating that part of the operation.
Every test has a test number. It started with 1, and it's up to 53,804. They've probably done a couple hundred tests since I looked at the database when they did that. About half are air, about a quarter are steam, a quarter are liquid, and that number is pretty much the same, but the tests keep going on.
And the original lab had done about 15,000 tests, so over 30 years we did about three times that many. I break it down into really five main categories. For new product certification: 36,000. Repair certification: almost 9,000. Laboratory comparisons, a little less of a common activity, but still over 600 tests. Almost 200 investigation tests.
And then, finally, 2,000 are labeled National Board tests. And what those are is you have to continuously test your process and make sure it's validated. We do tests of flow nozzles, system tests, tests of sample devices just for our own internal use. And we are constantly doing that type of stuff, make sure that you are really getting accurate answers that are repeatable.
But here is now where we can take those numbers of tests, and what's the purpose of them? And the first main purpose is the interface with ASME and National Board programs, and that's the new product certification. The number of tests per year have gone up, so we are at about 2,500 tests a year now. So that number is probably bigger currently. But over the whole time period, that's all different manufacturers, rupture disk manufacturers, assemblers – bringing in their product, testing it to the code standard, and hopefully making sure it works the way it's supposed to.
Those tests have to be done in an accepted lab, so we have a PRD certificate that's issued by ASME based on a review of our quality program. Those tests start with an original series of tests to establish the capacity rating value, and then there are production samples that are selected to represent the production element. The original ones are prototypes you might call them, and that's on a six-year cycle, and that's hopefully keeping that product still functioning the way it's supposed to and giving assurance to the members and hopefully the public that the pressure relief devices will function properly and have an accurate rating.
That way you know that line of valves has been through that process is we have that NB mark on the nameplate. There are older variations that it was just the letters NB. But that means that organization has been through the type certification process for that particular design, and they can put it on the nameplate for that purpose.
Not all the tests are done at our lab. About 85% of them are, though, so that's a pretty big number. Other labs are available to do that work. Most of the other labs are owned by valve manufacturers, so they just test their own stuff.
All the qualified designs that have been through the process are listed in NB-18. That's our listing of all the currently certified pressure relief device types. And that is available on NBBI.org. It's a living document, and they have that to the point where it's updated every day. So it's not really a document you would print out as a references source, but if you have a question about is this type certified, you can do searches through there and get a report on what that company does, what their product that they are certified for is.
Supporting that is the laboratory certification process. We are the ASME-designated organization for pressure relief lab certification. Like I say, we have a certificate for that, but then we audit all the other certified labs. And we are the comparison standard. So, if you think of like a big wheel, we are the hub, and everybody is comparing to us. And when we do that comparison, we are comparing to other people.
There is a list of all the certified labs. That's on the web page as well. That's not the whole list. They are mostly in the United States, but there is one in England, a couple in Germany.
On to the repair program, this is directly tying back to the National Board Inspection Code. The valve repair certification, or the VR program, technical requirements are in NBIC Part 4, an integral part of that document.
There is a separate document that has the administrative requirements. Those are all published on the website, so a new applicant can go find out how do I get this certification in that NB-514 document. Our scope is ASME/National Board capacity certified valves, and that's a link back to the fact that we were the certifying organization when that design was newly built. People who are repairing it are repairing the same product. Hopefully it should go back and function as the new valves are supposed to.
They demonstrate the process, so they go through an audit just like an R stamp company or anybody else. But then their demonstration is to repair several sample valves, which gets sent back to the test laboratory. It's at least two valves. It can be three or four depending on what the scope of work is. So, if they do steam valves, that adds a valve. If you do Section IV, you could potentially have to do a demonstration valve there. And they are tested to the same standards as a new valve, so it's expected to open within the same tolerance and flow the capacity that's on the nameplate.
Over time, we have done almost 8,900 tests of valves for VR certification, so about 300 a year. Kind of piggybacking on top of that is the National Board Testing Organization Program, or the Test Only T/O Program. Those requirements are also in NBIC Part 4 and has its own administrative document. Its purpose is the testing and recalibration of ASME stamped pressure relief valves. It's for cases where people are doing periodic testing, but they are not going into the repair activity. So, this puts a quality program to that testing process.
And again, if someone is going to qualify for it, they have to test several valves. They are going to send them to the test lab. We are going to retest them and see if you are getting the same result that a certified lab is. Theoretically we are the measuring stick, if you will. Are they getting the same result for their test? Is their test accurate?
It has the same requirement for the number of valves they have to test, but it does tie very heavily to the VR program. So, the way it's set up now is if you qualify for a VR certificate, the T/O pretty much follows – they get that pretty much automatically. But we do have a few organizations that all they do is test smaller valves, and they maybe don't want to do repairs, so there are a few tests that are done for that T/O certification as well. So, for VR and T/O, the whole purpose of the testing is to demonstrate the capabilities of the organization. They are working with already certified designs, so that design should be capable of meeting the requirements.
But capability as to the test equipment, knowledge of personnel. Demonstrations on typical work samples encourage repair organizations to improve their capabilities. If you bring a valve in and it fails a test, there is a retest that's associated with that. And sometimes people have to upgrade their process, they have got to get a bigger test vessel, do some training on their people, and hopefully all of this testing is going to give assurance to jurisdictions and users that repairs and testing are reliable.
We do a little bit of investigation testing. Not very common, but that is available as a service to the membership. Over the 30-year period, we have done almost 200 investigation tests, so six or seven a year, and that's usually when there is a pressure equipment incident.
One of the things that will help you rule out one cause of the incident is to test the pressure relief device, if possible. And sometimes it works. That tells you that you may have had a failure below design pressure. Sometimes it doesn't. It may have, in fact, been that pressure relief device, something was wrong with it. Which gets us to the goals for the future.
Like any organization, we are changing, evolving, moving forward. We hope to continue to provide accurate, informative tests to all our customers. The type of equipment that we look at continually changes. So, you think, this is a valve that's been around for 100 years, what could they possibly do that would be different? And right now, we are seeing several samples for very large valves that are primarily used on flair systems that are called spring-loaded or buckling-pin non-reclosing pressure relief valves. So, it's a very large valve that once it opens, it stays in the open position. A lot of them are based on butterfly valves. We can't tell people what to make or what to innovate. They come to the code, and sometimes they have to get a code case or something to cover that. But here is this new product. Well, we have to look at how are we going to test that. Some of those devices are very big, so we are seeing some cases where we do flow testing of models and then a performance test of a larger valve to maybe see if it still functions properly.
We have to respond to the changing business environment. We had, of course, a huge example of this just in the last year. Everybody has been affected by COVID, and the lab staff did a great job. We went through a period we didn't want to have outside people coming into the laboratory if we could avoid it, so the technical staff developed a process to put the tests online. The customers could come in, dial in through a Zoom meeting, and have all of the electronic data available on a screen. It is the same screen that the engineers were looking at as the test was going on, along with a view of the valve itself, and they can see and hear what's going on. And that has actually turned out to be popular for people who couldn't travel. You know, those are the kind of things that come up. We have to be able to respond to those and be ready for those types of things that change.
Continuing to provide service to the membership and users of pressure equipment. And hopefully this is one of the things that pressure relief valves has become the new standard terminology. I have heard people complain that, well, in the old days you knew what a safety valve was – it told you what its purpose was. And what we want to do is keep the safety in pressure relief devices, and hopefully the laboratory is a tool that we can use to accomplish that purpose.
Thanks for the opportunity.