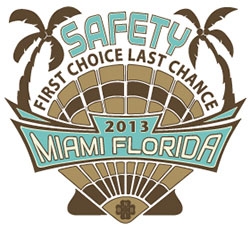
82nd General Meeting Speaker Presentation
Recent Catastrophic Failures of High Temperature/High Pressure Power Boiler Components
By George W. Galanes, P.E.
The following presentation was delivered at the 82nd General Meeting on Monday, May 13, by George Galanes. It has been edited for content and phrasing. To follow along with Mr. Galanes’ slide presentation, click here.
Introduction:
George Galanes is a licensed professional engineer in the states of Illinois, Pennsylvania, and West Virginia. He has been employed in the power generation industry for over 30 years. He recently retired from Midwest Generation. In September, Mr. Galanes joined DTS, Incorporated, as a consulting metallurgical engineer. He holds both a bachelor's and master's of science degree in metallurgical engineering from the University of Illinois, Chicago.
Mr. Galanes is currently a member of the National Board Advisory Committee representing the welding industry. Additionally, he is a member of the NBIC Main Committee, as well as chair of the NBIC Part 3, Repairs and Alterations, Subcommittee. George is also a member of the ASME Boiler and Pressure Vessel Code, Section 1, Standards Committee; and chair of the Subgroup Materials under Section 1. For over 30 years George has been directly involved with conducting failure analysis investigations associated with power generation equipment. He has also participated and led root cause analysis investigations of large equipment failures and performed welding and material consultation. There have been a number of recent catastrophic failures of high temperature and high pressure power boiler components. In his presentation, George Galanes answers the question: Where do we go from here?
Mr. Galanes:
In my presentation I want to share some recent failures of boiler components and what's involved with some of the investigative work. I also want to cover some new ideas on how to get the message out to the mass public when we have component failures, and how we can get the word out to the people who need to know about it.
[Slide: Introduction] My objective is to discuss two rather important recent failures of high-temperature and high-pressure boiler components. Both failures were catastrophic and resulted in loss of equipment, and one failure caused injury to plant personnel.
[Slide: Primary Superheated Link Pipe Ruptures] This is a slide of a failure of link piping that is external to the boiler. It was located near external casing. This picture really doesn't do much justice because even though you can see the axial rupture that was in the thick wall piping, there was quite a bit of collateral damage associated with this particular failure.
[Slide: Typical Boiler Layout] Here is an example of where the failure occurred as shown by the red arrow. This was primary superheater inlet feeder pipes, and you can see there are 136 sweeps. Those are actually called bends, and then we have material OD, which was 6.25 inch OD, and wall thickness was 935. It was a carbon molly steel, which has been prone to having issues in the industry but not something like this. The design pressure is of course 4,100 pounds, and then we are looking at 830 degrees up. This was a supercritical boiler.
[Slide: History Repeats…] Back in 1982 there was a five-inch-long tight through-wall crack found during hydro testing, and that was during a forced outage. Of course, a bowed sample was removed by the owners at the time. And they didn't really do a very in-depth analysis back in '82. The results came back that there were many sulfite inclusions, no Charpy impact testing, and no graphitization observed. It was therefore labeled as an inclusive failure mechanism, which was probably the first clue that something was going on, but they didn't really know what it was. Then it was repaired, the crack was ground down, and it was rewelded.
Then in 1990, another through-wall crack was found. This was during a hydro test after a forced outage. No metallurgical analysis was completed at that time. Once again it was repaired and rewelded.
And then in 2004, a through-wall crack, which was an on-line leak at the time. No metallurgical analysis was completed: a common theme there. And then we replaced the elbow with upgraded P-22 material during a scheduled 11-day outage. This was in 2004.
Now we are up to 2009, which I was involved with it at that time. There were multiple elbow failure events during a unit shutdown. And here the metallurgical analysis that was performed did not detect any grain boundary graphitization because of the unfamiliarity with the damaged mechanism. Going from 1982 to 2009, we had repeat events of which the majority was really never subjected to a thorough root cause analysis. That's a common theme here.
In 2011, we had a single elbow failure of a previously-repaired elbow during steady state conditions, which was different than in 2009 where that occurred during a boiler upset. The original thought in '09 was that maybe we had an overpressure event, and being carbon molly material, that may have been susceptible to brittle fracture for potential graphitization. But we never found any evidence of that from the traditional form of graphitization.
[Slide: What happened on that day] On Thursday, February 10th, a primary superheater inlet pipe ruptured at 7:37 AM, and this was during a normal load increase. This unit is a load-following unit. There were injuries. In the 2011 failure, two plant employees and one contractor employee were air lifted to a burn center, all with second degree burns. They were all released the following day. Two employees were taken by ambulance to the regional medical center, and both released the same day; one employee was treated for dust inhalation. Fortunately there were no very serious injuries and we were able to recover from that event.
[Slide: Type of Rupture] This is an example of the sweep that failed. As you can see, it's relatively thick lipped, and it was an axial rupture along the extrados of the sweep. This was also the same type of failure that occurred in the 2009 event. This particular type of failure was catastrophic, meaning that it happened without any leak before a break. It just broke.
[Slide: Teamwork] As part of this 2011 incident, a team was assigned – a multidiscipline approach – and we also brought in an outside contractor to assist and give us an objective point of view. We needed somebody who could come in and take a step back. Many times as you go through these investigations, especially ones like this where we have had multiple repeat events, you tend to get myopic, and that's the type of thing you really don't want to have in a true root cause analysis (RCA) investigation.
The cross-functional team members consisted of operations, plant personnel, and outside consultants. And we ensured a methodical review of events and known processes for establishing causal factors. This is extremely important in carrying out a proper root cause investigation. In addition, fracture mechanics and boiler flow modeling were used to assist in the RCA. Because, as I mentioned before, back in '09 there was concern that we had potentially a boiler overpressure event or excursion that occurred, and we thought that could have created shock waves which could have potentially triggered the brittle fractures in the previously-formed sweeps.
An outside entity was the lead in conducting the RCA to ensure independent technical oversight, and also because there were injuries involved with this particular failure. The failed sweep was sent to a metallurgical lab for a comprehensive analysis, and that analysis included chemistry/tensile testing. Quite a bit of tensile testing was done on the undamaged sweeps that we removed, as well as the failed one. We took samples both in the longitudinal and in the tangential directions because we were concerned about the effect of potential damage that could have an impact on one orientation in a particular failed piece or undamaged piece versus another. We spent quite a bit of time mapping out where we wanted to take the specimens. We also did hardness testing, impact testing, and metallographic examination.
[Slide: Look Closely] This is the typical type of damage that was observed in the failed sweep. The little black chains are actually graphite -- it's actually intergranular graphite that has occurred over time. This perplexed us because we saw something like this in 2009, but there is not much information in the literature that told us this was carbon that was being pulled out of the carbon molly material. And if you look at the typical graphitization that occurs in P-1 or carbon molly material, the P-1 material, usually it's going to be graphite nodules which probably most of you have seen or at least seen in the literature.
In this case there was very little in the way of any literature to point us in a direction that the graphitization was actually occurring along the grain boundaries. The material literally was imbrittling itself and there was no strength with the grain boundaries themselves. I guess over time, if there was no pressure, you would start to see the grain simply coming out of the material just because of this damage mechanism.
[Slide: What happened…] This type of damage mechanism is time-dependent, meaning as a grade 1-P material remained in elevated-temperature service, the pipe would exhibit continued loss in toughness and ultimately fail catastrophically with no leak before break. And that's exactly what happened from 1982 as we were progressing in time. And that probably explains the diagnosis of inconclusive results because they probably didn't pay attention to this type of subtle damage mechanism that was occurring over time.
The failure initiated and propagated from the OD surface of the bend extrados. This location would have been exposed to the highest forming strains. Bulk hardness testing confirmed the extrados as having the highest hardness, which was why we did the hardness testing. And you compare that with the straight runs which were much lower. The higher the number, the harder the material. All of this now is starting to come into play as to understanding that the P-1 material has the potential for graphitization, now you continue doing the lab analysis, and things start to become a little bit clearer.
The loss of toughness and significantly reduced elongation values were confirmed. And that was based on the tensile testing that we did. In the formed sweeps versus straight section of grade P-1 pipe and based on extensive mechanical property testing, so all of the work that was done in the 2011 investigation pointed to the unusual damage mechanism with the P-1 material.
[Slide: In summary] We found that the grain boundary graphitization was confined to formed bends and did not appear to have been thermally treated after forming, meaning the bends were probably cold bends based on radius that we saw, and there was no thermal treatment which should have been done with today's codes and standards. But at this time, this boiler was built around the 1960s time frame. Because of the grain boundary graphitization damage mechanism was not well understood or reported in the literature, which I mentioned before, it was more difficult to quantify the severity of damage in comparison to more traditional forms of graphitization with the nodules. There are means out there to assess graphitization damage nodular form, but there wasn't anything for grain boundary graphitization. After extensive sampling of sweeps and straight pipe sections of known grade one primary superheater pipe material, there was no grain boundary graphitization observed in straight sections of the grade one pipe because the spools contained no residual forming strains, which was very important. Once we understood that the sweeps were susceptible to grain boundary graphitization, what do you do with the straight sections?
[Slide: Prevention…] Risk management comes into this as part of the corrective actions. Based on the findings from the unit primary superheater sweeps, a review was performed to determine the extent of grade one pipe material. I was tasked with going through the other boiler on that property and also the rest of our Midwest Gen plants and determine if we were at risk. Carbon steel piping was also sampled because there was carbon steel piping on this particular boiler, and no grain boundary graphitization was detected for the carbon steel piping. Similar thickness and similar OD, except it was carbon steel because it was lower design temperatures in that portion of the boiler.
In addition, a search of the grade P-1 material was expanded to include the remaining coal-fired units for this client and for the other one I worked for. No other grade one piping was installed in the boiler proper, so that was good. It limited the risk to just the two units for the previous client. After careful review of the metallurgical test results for the sample grade P-1 pipe material locations for both boilers, it was recommended to replace the original grade one sweeps with grade 22 and monitor the remaining P-1 piping until full replacement using the grade 22. This was very important because we didn't really quite understand the mechanism as to it being time dependent. We knew it was, but we didn't know how fast this damage occurred.
As part of the evaluation, we did go through a risk ranking for all the sweeps, and some sweeps had more advanced graphitization damage than others. We took that information and mapped out a strategy to be able to go for some period of time with minimal risk of any future failures, and then to allow us to do a scheduled outage to replace the P-1 with P-22 materials. This was a fairly complex investigation that took about eight months, so it wasn't something that was simple.
[Slide: Failure #2] The second failure occurred with an heat recovery steam generator (HRSG), and a schematic shows a piping system that initiates from the HRSG. This is a start-up line for main steam conditions. What happens is the line is used when they start up the HRSG. There are, I think, four units on the property, and this line is used to start the unit up. As steam quality comes up, the line is valved out, and there is a main steam line that goes to the other location on the property. The bubbled areas show the approximate locations of where the rupture occurred on this particular warm-up line.
[Slide: Warm-Up Line Failure Investigation] The activities associated with the root cause analysis and metallurgical failure analysis involved mapping of the failed warm-up line, which is important. When I got the call, I immediately rushed out to the California facility and began the process of mapping out the pieces of where the failed warm-up line was found; removal and preservation of the failed segments; and engineering review of the operating information. Of course, we all needed to know at that time if the line was over pressurized or possibly operating above its normal design temperature. Engineering review of the design basis of the warm-up line, and then selection of a metallurgical lab to perform the laboratory analysis in support of the failure investigation.
What's good about this particular failure was nobody got hurt, so no lawyers were involved, and the company asked me to personally do the root cause analysis with an outside lab. This took a different twist than the previous investigation where we had injuries.
[Slide: Failed Warm-Up Line] Here is an example of where the rupture occurred. It was a fairly ductile fracture based on the extent of deformation that occurred.
[Slide: More Pictures…] Here is an example of a close-up of a T looking downstream. Obvious features: to the right is thinned material which is indicative of a ductile rupture; there is shear deformation on the top half part of the failure and near the bottom; and also what looks to be rust or residual water that's been in the line.
[Slide: And more pictures…] What we did then is capture the fragments. These are the various fragments that I thought would be of most interest to lead us back to the damage mechanism, and ultimately the root cause of the failure. Those pieces were mapped as shown and then sent to a metallurgical lab near the West Coast because we didn't want to have to ship everything to the Midwest.
[Slide: Warm-up Line ID Surface] What is obvious here is the extent of pitting that was on the inside of the pipe. You can see round, bottom-type pits which corresponded also with thinning that occurred from the ID out. This is typical of corrosion-type or oxygen cell pitting that one would see with potentially stagnant water conditions in a line.
[Slide: View of the ID Pipe Surface] This example is a different shot showing the extent of thinning at the very base of the pipe at the 6:00 position. This was a horizontal line and you can see a trough effect, and also along the side walls fairly large pits occurred.
[Slide: Local Thinning from Corrosion] This is another example of local thinning from corrosion.
[Slide: Results] Some results were: failure of the warm-up line; internal wastage that weakened the pipe resulting in catastrophic rupture in service at multiple locations within the line. The internal wastage was corrosion from either stagnant or pooled condensate during off-line conditions from exposure to air atmosphere. There was no evidence of internal erosion or -- erosion/corrosion that would have contributed to the failure. By the way, this material was carbon steel piping that was used for the warm-up line.
[Slide: RCA] The causal factors of the root cause analysis was interesting. There is a valve that was on the warm-up line that's used as part of the start-up process, and what we think happened was that this 12-inch Fischer regulating valve exposed the weakened pipeline to internal operating pressure near main steam pressure conditions. In other words, this line normally does not see full main steam operating conditions.
Typically the valve is used as a regulating valve, so as the steam comes out and the steam quality goes up, this valve suddenly closes shut and then the other valve opens up, and then that steam line then becomes inoperative and the other main steam line takes over. In this case, there was a logic error, and apparently the line had essentially isolated itself under full main steam operating conditions. That normally wouldn't be bad from a design standpoint because a line is designed for that, but internal thinning occurred over the years. And suddenly a very thin line was exposed to main steam conditions, which it really should have been designed for, but unfortunately, the fact is that it couldn't take the pressure. So we had a catastrophic rupture of the steam line.
However, it is important to note that if the warm-up line did not sustain internal corrosion, it would have safely accommodated main steam internal pressure based on original design conditions from ASME B-31.3. But it was out of sight, out of mind. Conditions of improper drainage and then stagnant conditions developed in the line over the years. I think the line was in service about 18 years, so that was enough time to have this residual or parasitic-type thinning that ultimately resulted in failure only because we had a logic error in a regulating valve that failed.
Then there was a lack of urgency in reviewing the previous pipe inspection results from February 2011. This line was inspected and they knew about the thinning, and yet they didn't call the support group, which I was in at the time. They took it upon themselves, thinking the line was designed for main steam conditions, but with the valves and whatnot, they didn’t expect to have a valve failure. They were eventually going to replace the line, but the line failed before that.
This is something to be aware of. It was probably one of the critical findings from the due diligence on this particular failure. Then we have the need to have a sufficient number of drains to ensure proper drainage of the warm-up line to prevent stagnant or pooling of condensate when the line is valved out. This becomes a corrective action. We recognized that we found evidence of pitting in the pipe, and then we went back and looked to see how the line was sloped, and we found that there were spots where the ground supports shifted a little bit. The line then started to get some low spots. When it was laser shot, it confirmed there were areas that could pool stagnant condensate. And of course, in an oxygen environment, you are just asking for corrosion pitting.
[Slide: Prevention] We developed inspection plans for the warm-up line and other high-energy steam lines at their facility. And the inspection program results should be reviewed independently of site personnel to ensure no gaps or missed opportunities for corrective actions. Even though we found the damage mechanism, the root cause pointed back to a problem with their in-house engineering controls. This was part of the prevention with the corrective actions. And then we surveyed the replacement warm-up line and other lines that are used on an infrequent basis to determine the need for drains or drain pots.
Because the warm-up line had an issue, we decided to take that to other lines at the facility, and we found some interesting results. With these corrective actions, we steered them in the right direction to prevent recurrence of failure.
[Slide: Where do we go from here? And following slide] We need some kind of mechanism to get the word out and provide information to users and jurisdictions, and make others aware of these types of failures. Some of you might have heard about the first failure I talked about, but I'm sure others of you have not heard about the warm-up line because it didn't result in any injuries. Something we need to think about is how to get this type of technical information distributed. And it doesn't have to be in the form of confidentiality agreements, but more in terms of promoting safety and trying to raise awareness. We can learn from these types of failure analysis investigations, even on the corrective action side, and it could perhaps be applicable to other folks, including yourselves or somebody you know who operates a facility. Our objective should be to prevent reoccurring failures, promote safety, and get the word out to help make safer environments.
Q&A
MR. CANTRELL: You kept mentioning on the first scenario that there was a lack of a description of this type of problem with the intergranular graphitization. Have you created literature or has the owner created literature and maybe had it peer reviewed and tried to get it published in like ME Magazine or any of these others?
MR. GALANES: The Electric Power Research Institute (EPRI) took the initiative to come up with some project funding to look at that. But unfortunately, as great as EPRI is, it's only as good as its subscribers, and that means only a limited audience out there. But to answer your question, probably a paper should be done on this. I haven't had time to do it. Are you asking me to do it?
MR. CANTRELL: Please.
MR. GALANES: That might be possible. I will tell you, it was a very interesting failure mechanism. I had some of the most brilliant guys on this. I mean, I missed it, and then I had three labs, and they missed it. I had another guy that looked at it who I'm not going to name, but he eventually got it through somebody who he knew that was an old-time metallurgist before he had recently passed away. I think a paper is in order. We will probably get something out. I think it should be done. The problem is the sensitivity towards the facility that had this failure. A lot of times you have to work around that. But I think it's been long enough now that we could probably get a paper out of it.
AUDIENCE MEMBER: Have you tried to heat treat any of the specimens?
MR. GALANES: Yes, we looked at that. Carl Lundin did quite a bit of work on this type of stuff, and what he found was when you reheat treat, it comes back even faster as far as graphitization damage. So, yes, we looked at that option, but we found it wasn't going to be effective because we really couldn't put a time frame on how long we would want to keep these things. What we decided to do was to look at the damage sweeps, we then took damage sweeps out -- or a sampling of sweeps, and then we categorized the damage. It's actually interesting; some of the sweeps that had the same bend radius did not have the same extent of intergranular graphitization. We came up with a rating process of one through five. I can't disclose anything beyond that because that's tied up, but that's how we tried to approach it, and it worked out very well. The facility that had this problem no longer has the P-1 piping material. It's been changed out.
MR. CANTRELL: Is this common to a certain boiler manufacturer – is it common to certain years of manufacture? How can we as chiefs try making a more targeted outreach to people in our states or owners in our states to try and help them out with some of this?
MR. GALANES: Let me think about that. I need to be careful how I answer that, and not from the lawyer's standpoint. I would say, no, it's not related to a boiler manufacturer. P-1 material -- carbon molly materials have had issues of graphitization over many years. I don't like the material. I think it's unpredictable. I wouldn't use it today. But for facilities that have it, I think what you need to do is start a comprehensive evaluation program to look at, first of all, formed areas and where the bends are. Focus on those areas, do some evaluation to see if you even have the grain boundary graphitization damage.
Now, a unique feature about this piping that I didn’t mention is it had an out-of-conformance specification for aluminum. Somehow the aluminum was increased in this particular heated material. But beyond that, it just came down to temperature, forming, thickness, all that. But you can still manage the process. It's a matter of knowing what to look for.
MR. CANTRELL: If I'm talking to an owner in Nebraska and tell him he needs to be aware of this, and he may ask me where to find more about this and what exactly it is, what can I tell him?
MR. GALANES: This is very, very unique. And that's why I was happy to come here and talk about it, because it's something that's out there lurking, so you need to be aware of it. EPRI certainly could help you too if you are a subscriber. But if a person in your jurisdiction is not a member of EPRI, they are not going to get that information. They are going to get it through this type of venue, which is the reason why you want to bring it forward.
MR. WILLIS: Regarding the second instance, those lower areas of pooling and pitting, was that an issue that developed because of inadequate support?
MR. GALANES: It was an issue of improper drainage and exposure of the line to atmospheric conditions. And the improper drainage was, I think, just the way the line was originally laid out. It wasn't sloped properly. It didn't have any drain pots in it. Now we have got that installed. When the line was replaced, we reengineered it to have that. But there were no drains from that point that I showed you going all the way down. That line was probably about half a mile in length. But that's been corrected.
AUDIENCE MEMBER 2: You had a time factor, so it's very time sensitive.
MR. GALANES: For the graphitization?
AUDIENCE MEMBER 2: Yes.
MR. GALANES: Yes.
AUDIENCE MEMBER 2: There are a lot of older plants -- we all have older plants in our states. Is there a time period that would have more likely had this material in this type of situation that we can narrow the time range?
MR. GALANES: This vintage material was 1960s.
AUDIENCE MEMBER 2: So something in the '60s up to the '70s you would be weary of?
MR. GALANES: I would. Again, we had a nonconformance on the aluminum content. The aluminum content was much higher than it normally would be. It was out of spec. But the key here was the fact that the bends were not thermally treated after forming.
AUDIENCE MEMBER 2: None of them were back then.
MR. GALANES: Correct.