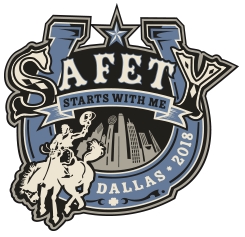
The 87th General Meeting Speaker Presentation
"NuScale Power: A Nuclear Manufacturing Paradigm Shift"
Scott Bailey
The following presentation was delivered at the 87th General Meeting Monday General Session, May 7, 2018. It has been edited for content and phrasing.
INTRODUCTION: Scott Bailey is the Vice President of Supply Chain for NuScale Power. He leads all aspects of the supply chain function, and has over 30 years of experience in power generation supply chain management. He holds a Master's degree in Business and a Bachelor's degree in Marine Engineering.
Mr. Bailey's slide presentation can be accessed here.
MR. BAILEY: Today we are going to talk a little bit about what we are up to and what you can expect to see in the future, and how that impacts the industry and impacts a lot of you folks that are sitting right here.
The reason we talk about the global reality is that power plants and certainly the NuScale Power module are a lot more than just electricity-generating devices. When you think about a lot of the areas of the world, they haven't been electrified. They have global warming issues or air pollution issues. A lot of people don't have clean water. So we like to think that the solution we are providing is a lot more than just traditional utility power generation. Here at NuScale we have a commitment to the people, the planet, and prosperity.
This is our mission—NuScale Power produces scalable advanced nuclear technology for the production of electricity, heat, and clean water to improve the quality of life for people around the world. So that's the motherhood and apple pie part of what we do in our business. But let's talk a little bit about NuScale Power.
The idea of the NuScale reactor has been around for a long time. In fact, back in 2003 under a Department of Energy grant, the work was originally begun, and it was called the Multi-Application Small Light-Water Reactor Program, and it was at Oregon State University. You are also going to see that we are in Corvallis, Oregon.
We were formed in 2007, and we’re a single-purpose entity. In other words, there is only one thing we do, and that is designing and getting our nuclear power reactor certified.
Fluor is our major contributor. Many of you probably know Fluor, if not all of you. In other words, they became our major investor in 2011, and since then, between Fluor and the U.S. government, that's been the source of our funding these days. What a lot of funding it is to get a nuclear reactor out there. And you will see that. So in 2013 we received matching funds of 226 million dollars from the U.S. government. And we have already spent that.
We have 350 patents, and we have some applications for more out there. We have 344 employees.
And we are currently undergoing what's called the design certification process, and that's in order to get our design in front of the regulators so that they can certify that it can actually be built. And we are the first small module reactor (SMR) technology to go through that process.
I'm going to talk to you a little bit about the plant. We are not going to get into a lot of details, but it's more than just a plant. And you'll hear me say this more than once. It's twelve plants within a plant. So our standard plant design is twelve 50-megawatt reactors. It's an ASME vessel within an ASME vessel. So unlike some of the large plants you may have seen, there is no concrete containment. Our outer vessel is the containment vessel. And it also is an ASME Section III pressure vessel.
Our plant is designed so that we have twelve of these modules. There are six modules on one side and six modules on the other.
What makes our plant special from a safety perspective is we don't require a lot of electricity. Well, we don't require any electricity. There was just a recent news release that part of our design had already gone through the Regulatory Commission. We do not require what we call in our industry safety-related power to shut down this plant. We don't have to do anything. It really just relies on convection, gravity, and conduction. We only have five valves inside the plant that have to work, and the control rod drives the drop, and those drop on a loss of power. So it will safely shut down.
Generally the way this design works, it heats up the water. The water goes up through the riser. It spills over onto helical coil steam generator tubes, and it heats the water that is in the inside of the tube.
So unlike a typical light-water reactor design, we heat the water –we make the steam inside the tubes instead of outside the tubes. And then once the water gives up its heat to the coils, it drops back down to the bottom, and it just starts all over again. And it's really that simple.
As I mentioned before, each one of these reactors has its own steam power plant that goes along with it. Think twelve steam turbines. Each one of them is independent from each other, and when you start thinking about the flexibility of this design, you can see why our founder did it this way. Each one of those reactors sits in its little egg crate, sits in its position within the reactor building. The twelve modules are housed in the reactor building. And, incidentally, that's the only place where any safety-related equipment is. And in addition, the buildings that are perpendicular to the reactor building are where the steam is, basically where the balance of plant equipment is housed, so six on each side.
So as you start thinking about this, you can install one reactor, make electricity with it. Install another reactor, make more electricity. You can do six. So it's truly scalable.
One of the advantages that our design provides is factory fabrication. The whole module itself, if you look at the containment vessel, which is the outer vessel, is about 75 feet tall and about 15 feet in diameter, and the inner vessel is about 58 feet and around 10 feet in diameter, and there is a vacuum in between the two. These can all be built in the factory. We've done a lot of work with a lot of the U.S. forging companies, and they can make a lot of forgings. So unlike the current big plants now that have to go to Japan or other places to get the forgings, we don't need to do that because our forgings aren't that big.
So factory fabrication. Small footprint. We sit on about 40 acres. And recently there were some announcements about our emergency planning zone, meaning that, mathematically and technically per the standards, that instead of having an evacuation zone that's ten miles out or five miles out, whatever it might be, ours can be the site boundary just because of the safety of the plant. So it becomes an industrial safety kind of challenge.
It's a transportable and flexible operation. When we have twelve plants, we have 100 percent steam bypass, so we can dump all of the steam of any one of our steam turbines into a condenser at any time, so we can control power and load shaping and so on.
So where are we going from here? Over a billion dollars will be invested before we shovel one load of dirt. This is all in just getting this thing certified and ready to go. That's a lot of money. That's a lot of investment. That's a lot of time.
As much progress as we have made, we are still just better than halfway there. We are kind of in the six hundred million dollar range. So we still have a long way to go. We are in the process of selecting our fabricator who is actually going to build these modules.
And then the owner has to get a license and so on and so forth. So we still have a long way to go. The schedule is going to be 46 months from the time we submitted our application to the time we get design certification. And people say 46 months, wow, that's a long time. That would be the fastest ever by a long shot, right? It's a long time, and it's a lot of regulations, it's a lot of certifications, and a lot of work.
We just completed phase one. In fact, that was in the news this last week. And there are overlapping phases for the various chapters, but needless to say, we are still on schedule. These are the kinds of activities that we are up to. We are in the 2018 time frame. We are selecting a manufacturing partner. I spend the majority of my time working through those details.
As you can see here, we are also pursuing our N stamp.
And then in 2019 will be the combined operating license application (COLA), and that's what the owner has to have. We get design certification that says our design is safe, and then the owner gets the operating license that basically says it's safe to put it at a specific site. So we expect to get design certification in 2020 and start building things in 2021.
So what's different?
I've talked about a lot of these things, but the whole nuclear steam supply system is all housed inside the integral power module. That's unusual in itself. The only important things which attach to that are our chemical volume control system, our instrumentation for our safe shutdown and those kinds of things.
But from a pressure vessel perspective or from a safety-related perspective, it's all inside the module. Once you get outside of that, it's not safety related. It is factory built. We talked about that. The turbine buildings themselves do not have any safety-related equipment in them. And we talked about this before, that the ASME vessel, is a vessel within a vessel, and each module feeds its own steam turbines. So it is truly a modular reactor.
So from a supply chain and from a manufacturing perspective, what's the paradigm shift?
This isn't your traditional power plant. This is much more like Boeing building aircraft than it is an EPC building a power plant in, for example, South Carolina. This is not a one-off thing. This is manufacturing. You have to start thinking about production lines and volumes. In fact, we've already engaged ASME in a few areas. We need to be able to inventory these modules. And right now the system doesn't necessarily allow us to do some of those things.
It's a steady-state manufacturing in a factory kind of thing. You are selecting your supply base based on a long-term relationship with these suppliers. It's like if you are building a Volkswagen, a BMW, a Ford, or whatever it is, in that they have a select set of things that come with the car. You don't get to choose who made the steering wheel or some of these other things. You have a very limited number of options. So we will be selecting these long-term partners for heat exchangers and pumps, even on the balance-of-plant side, so that we can standardize the plant.
So the impact that it will have on the industry is that it is much more of a factory focus. A lot of inspectors will be out in the factory, both the code inspectors, as well as the NRC inspectors. Obviously, they will be at the plants as well, but they will be in the factories because the magic happens inside the NuScale Power module, so that's where they will spend their time.
For me on the supply chain side, we have fixed pricing opportunities. Once we've built a few of these, we will have a high degree of confidence in how much it costs to make one of these things. It's all about quantities and scale. It's not about size. The current large reactors that are being built in the southeast are very large reactors. They are all about size, but we are all about the quantities. And our challenge will be about how do we scale. Because you order one plant, you get twelve modules; you order two, 24. You can see, it scales pretty quickly, and it doesn't take long for you to strip out the capacity that we currently have in the United States.
Standardization is a great opportunity. With this many plants, let's not follow the old nuclear plant designs where you had three different N triple S suppliers on the same site with three different kinds of plants. No, it's one kind of plant all the time.
Load shaping and load following—I mentioned we have 100 percent steam bypass, which means that even a 50-megawatt reactor, we can dump as much steam or as little steam as we want to to manage that power, plus we can drop 50 megawatts off-line any time we want to. So there are all kinds of load shaping and load following options that we can utilize.
And there are all kinds of nonutility uses, which is what we call our NuScale Diverse Energy Platform. There are a bunch of different things that we have looked at here. We have looked at co-generation at oil refineries. We have looked at hydrogen production, desalinization and coupling with wind. We've studied all these things.
And we've also done some study on what we call mission critical kind of electricity. So the whole concept of making sure you get reliable power, four nines, five nines kind of reliability at smaller megawatts. Having twelve reactors, it's pretty easy to get those numbers up pretty high.
I've talked a lot about where we are headed, and it's pretty exciting. I have been with NuScale for seven years, which in NuScale life, that's a long time. And I'm pretty excited to be there. It's really going to change things.
And I think there are people in this room where your fingers are going to touch this in some way, because we need the codes to help us get through this because this is being built to ASME standards.
Questions?
MR. CHRISTOPHER CANTRELL (CHIEF BOILER INSPECTOR OF NEBRASKA): Where is the core loaded?
MR. BAILEY: It will be loaded at the site. Core load will –in fact, the way our plant is designed, come apart. Basically there are three pieces, so refueling— loading is the same as refueling, where you take it apart and put the fuel in under water.
So I didn't mention this, there's a seven million, eight million gallon pool that those reactors sit in.
(A question is asked.)
MR. BAILEY: Yes, the question is on disposition of hazardous materials. Unfortunately, the Department of Energy still hasn't solved that for our industry. This is a light-water reactor, and it does create nuclear waste, or spent fuel, if you will. Our solution right now in our current design is what they call an ISFSI, which is independent spent-fuel stored installation. You would put it in casks on site.
(A question is asked.)
MR. BAILEY: The question was on life expectancy. Sixty years.
PARTICIPANT: And then they are retired, or can they be refurbished?
MR. BAILEY: I won't be around to know that for sure, what's going to happen, but, no. The reality is unless you relicensed it. Each one of the twelve in a plant will have its own license. So you theoretically could do a life extension if you did all the technical work, similar to what the older plants are doing today. But our current design life is sixty years.
Now, theoretically, one of my guys does decommissioning cost estimates as well, but this is probably the simplest plant decommission that there is. You just segment the internals, fill it full of ground and bury it, and you are done, and then you put a new one in.
So we just haven't really gotten that far down into it, but right now the plan would be retirement at sixty years.
(A question is asked.)
MR. BAILEY: Good question, and I probably should have touched base—because the question was when can we shovel dirt. 2026 right now. Our current lead customer is Utah Associated Municipal Power Systems, and they are advancing down this path to get a design certification to site it at the Idaho National Lab just outside of Idaho Falls.
They have already squared away the water rights. They have the lease squared away. They have 30-something smaller utilities (UMPS is 40-something), municipals and those kinds of utilities that have signed up for the project. But they have to get power sales contracts in place for all 30-something. So they are in that process right now in order to get enough off-take to go with the project.
And then the second one that we have been talking with is Tennessee Valley Authority. They have applied for an early site permit for a small modular reactor on the Clinch River site just outside of Oakridge, Tennessee. So that's another one we spend a lot of time with. I'm glad you asked that because I meant to mention it.
MR. DONALD COOK (CHIEF BOILER INSPECTOR OF CALIFORNIA): How has your prototype worked out?
MR. BAILEY: Actually, it's great, because that's been there since 2003. So when I say there, he's talking about the NIST, which is the NuScale Integral System Test facility. I think that's what it's called. But anyway, and that's at Oregon State University, and we work with those guys. It's basically a electrically-heated device—it's not really a prototype—that we can actually test heat transfer and all those kinds of things, and basically what we are doing is validating that our codes predict certain things to happen, and they actually do happen. So we have been very active in that facility since we opened it in 2007.
PARTICIPANT: What's the refueling cycle?
MR. BAILEY: It’s a two-year refueling cycle. So generally speaking, if you do the math, about every month, every other month, I guess, you are refueling. So it gets away from the typical nuclear refueling, which is eighteen months, where you bring several thousand people in and take everything apart and shut down your plant. You would almost continuously be in outage and moving from one to the other, and you would be doing it with your own staff. And it's really a ten-day refueling outage. It's not a lot of time. And refueling is not the critical path because we don't have that many bundles. It's the steam generator tube inspections that are actually the critical path for an outage.
(A question is asked.)
MR. BAILEY: So his question was if one NuScale plant goes down, can another NuScale module pick up that turbine. The short answer is no, because they are completely separated, so when that goes down, it goes down.
And there are a lot of reasons why we did that. Part of it was because the utility requests it. In other words, they like the independence, they like having the stability. The same thing happens—you lose a turbine shaft or something like that, you don't lose any more than 50 megawatts.
So, we have looked at all kinds of designs, but in the end the short answer is no.
(A question is asked.)
MR. BAILEY: No, they are not cross-connected. And there are reasons why we do that too, and it's related to reactor behavior.
And keeping those separated is important because the whole reactor power is based on how much steam you are drawing and so on and so forth. So you want to keep those things separated. We call it the multimodule effect, so you don't want one module affecting the other one, because it gets really complicated at that point.
PARTICIPANT: What are the advantages and disadvantages compared to current light-water power reactors?
MR. BAILEY: That's a good question. The question was related to how does this compare to the current light-water reactors.
We use the same fuel, for instance. In fact, we use half-height fuel bundles. So it is light-water reactor fuel with the same enrichment that is currently being used in the big plants.
And it is considered a pressurized water reactor. IPWR I think is the correct definition.
But the technologies that we are using are not anything that anybody hasn't seen. We borate the pool. In many ways, it follows the same concepts as a traditional PWR and light-water reactor, which makes licensing a whole lot easier for us.
(A question is asked.)
MR. BAILEY: The question was what is the pressure. I want to say 600 pounds, but I am going to have to get back to you on that. I can't remember.
PARTICIPANT: Wouldn't it be 400? I was wondering what the pressure rise would be.
MR. BAILEY: You asked me a question I can't answer. I can get back to you, and actually, my e-mail address is SBailey@NuScalePower.com. And seriously, sometimes I just have a brain melt and forget about things that I do know the answer to, but I certainly can get any answers to any questions. In fact, I know we have a spec sheet somewhere that I can get you that would fill in the blanks.
PARTICIPANT: Most current reactors are sort of solid state; I mean, they run all the time. Yours sounds like they are going to cycle a lot. Have you taken the effects of cycling up and down into account? You talked about taking them off-line if you don't need the power, so you shut it down and then maybe start it up the next day and do this on a more frequent basis than currently is being used.
MR. BAILEY: So I think the question was related to the challenges created by bringing a reactor up and down all the time?
My expectation is that most operators are going to want to run these either 100 percent power because economically it doesn't make a lot of sense to burn fuel that doesn't produce steam. So to dump the steam into the condenser doesn't make a lot of sense from a cost perspective. It allows you to do an instantaneous reaction to certain things.
More than likely I would expect owners to shut the plant down, and take it off the grid for a period of time, and it probably won't be a day or so. It will be like during an area where maybe hydro is really high or something like that for a load shaping, if you will, more than a load following.
We just know we can. I'm just not 100 percent sure an owner is going to do that because it's really not that economic.