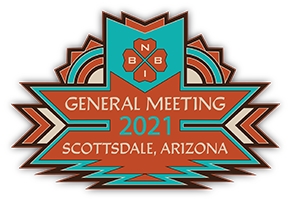
89th General Meeting Speaker Presentation
"Brazed Plate Heat Exchangers: Revolutionizing Heat Transfer with Reliability and Efficiency"
Stacey Marks, P.E.
The following presentation was delivered at the 89th General Meeting Monday General Session, May 10, 2021. It has been edited for content and phrasing.
INTRODUCTION: Stacey Marks is a quality engineer at Alfa Laval, Inc. where she is responsible for production quality at the company’s Richmond, Virginia facility. With over three decades in the industry, Marks has experience in ASME U-stamp vessel manufacturing, PED compliance, welding, brazing, fabrication, inspection, NDE, data reports, and joint reviews. A graduate of the University of Virginia, Marks chairs the ASME VIII F&E and ASME IX Brazing committees and serves as secretary of ASME IX GR. She is a member of the Section VIII and IX Standards Committees, as well as the Committee for Accreditation of AIs (CAA).
Ms. Marks' slide presentation can be accessed HERE.
MS. MARKS: Hello everybody. I'm here to talk about brazed plate heat exchangers, their reliability, their efficiency, and how cool they are. I want to thank the National Board for inviting me here today. I'm privileged to stand here in front of you, having used the Synopsis for many years, having called boiler chiefs every now and then to get my equipment accepted. And I have spoken in front of you once before, I want to say it was six or seven years ago at the July meeting. I talked about our gas-heated plate heat exchangers, but today I'm here to talk about the brazed heat exchangers.
I'm going to talk about design, application, manufacturing, which is really what I know best, the regulations, which is what you know best, and then I'll answer any questions if we have time. But first a little bit about who I am.
So, I'm a good ol' Virginia girl. My mom was a teacher, my dad was a policeman. I learned reading, writing, arithmetic, and rules. And I think that's why I'm here today, because that was my upbringing. I went to the University of Virginia. I have a degree in Mechanical Engineering. I have been inspecting metal at a third-party inspection company since 1991 when I got out of college. One day three gentlemen walked in: a guy named Tommy, a guy named Mike, and the inspector. I didn't know these guys. They brought me this metal box, and it had four holes in it and said, “We need you to proof test this thing.” So, I was like, “I do tensile tests, I do impact tests, I do inspections of water storage tanks. I can proof test a metal box. No big deal, right?”
We put it on the table, we hooked it up, pumped it up, and we all stood there. I think it was 2,600 psi. That was Mike Pischke. That's when I got hired to work at Alfa Laval, because Mike was working at Alfa Laval. I have been at Alfa Laval since 1995. And here I am 26 years later. Mike – half my life I have known you. What I also want you to know is that I'm a science geek. Science rules! I do have two kids and two grandkids, so I'm very concerned with safety in this world for the next generation. While I am a manufacturer, I, of course, know there need to be rules.
So brazed heat exchangers: I'm not sure everyone even knows what one is. This is a shot from the factory, the picture on the left is some of the product just built. These are what we call AC-240s. They are about 1-foot by 2-foot, 2-inch inlets. When you see them in the field, they are insulated like the ones on the right. It's not a shell-in-tube heat exchanger. These are little, efficient. It's not carbon steel. It's not dirty. It's small surface area. It's not cow-manure processing. This is something Alfa Laval equipment does. The chair of Section VIII, he works for Shell Oil. His company has bought some of our spiral heat exchangers for processing cow manure into biomethane.
Brazed plate heat exchangers are much cooler than this. Our heat exchangers are made of stainless-steel end plates, stainless-steel heat transfer plates, and the copper is what melts during the brazing process. We actually do make some where we use nickel in the brazing process. We don't make those in Richmond – we don't do that here in America – we do that in Sweden. What we do in Richmond is the copper brazing. We put studs on them for feet and lifting lugs, and I write that on my ASME data report every time.
This is a shot from a cross-section of one of our brazed heat exchangers. I put it in here to show you how small these refrigeration channels are. It's like a honeycomb, sort of like the radiator in your car. The way the heat exchanger works, it's two fluids: a hot and a cold fluid. They are in separate chambers. They never mix, unless the product is defective, but ours is not. They stay separated, and the heat transfer occurs across these thin metal plates.
We have small inlets, ¾-inch up to 5-inch. None exceed 6 inches. The biggest one we make out of Richmond is 5 inches. The chambers are small, really. The largest one we make is this tall, so 7 cubic feet is the largest volume you'll see. MAWPs are pretty high for the copper brazed version that we make in Richmond and 650° F is the highest we rate them for. The temperature profiles, fascinating to me, -320° F. Every time I write that on a data report, I'm like, “Wow.” The high temperature is not so fantastic, only 400° F.
What we do at Alfa Laval, though, is pretty unique: we patent our channel plate designs, and we have a lot of patents. They are all in Sweden and overseas, but the concept is to create refrigeration channels of different sizes. The top is our symmetric design, which is what we've been making for 100 years. The lower picture is the new concept where there is more water, more hot, and less refrigerant, which gives you more efficiency in heat transfer. The less amount of refrigerant you can use, the more likely your equipment is accepted by the state.
But where do we use them? Chillers are probably the primary use you will see. The brazed heat exchanger is down here in the bottom underneath, usually insulated. It's a black box; you wouldn't even know what it is. Chillers, they are evaporators, they work as condensers, they work as desuperheaters. All these terms I remember from going to school when I took heat transfer. Never used them, because I'm in the factory, but all the designers, of course, talk in these terms.
Wide range of uses. The cool stuff, though, natural refrigerants. This is where we are trying to get our product out there, because we can design some unique features to handle R-290 and ammonia and propane.
Our equipment is being used as gas coolers for transcritical CO2. I didn't really know what that was. I had to Google it for this presentation. And I didn't know if all of you felt the same way, so that's why I have written it in here. What is transcritical CO2? It's a system that uses carbon dioxide as a refrigerant. This is natural refrigerants, things that don't hurt the environment. But you do have to have equipment capable of high pressures with superior fatigue strength, and our brazed plate heat exchangers do have superior fatigue strength.
They are also used in commercial refrigeration. Grocery stores - the refrigerators, CBD extraction, that's the new thing. With cryogenic uses, we will be able to preserve what you know forever.
I am fascinated by the cryogenics myself. We have a big customer in California, they buy our product, they have heavy documentation demands. Every time they buy one, I have to create a CFC for them and get it on the product before it leaves the building. But it's fascinating to have customers like that with high demands because they are doing cutting-edge work in the industry.
Manufacturing is the fun part. We have four sites around the world. Richmond is our newest site. We opened there in 2019. I have been at Alfa Laval since 1995, and I was very happy to have brazing come back. We've got a much bigger furnace this time. Of the 3 million units that we make globally, out of Richmond it's 25,000. So nowhere near what they are making out of China and Sweden. They make little bitty ones that are this big. The smallest one we make out of Richmond is about a foot long, theirs is 6 inches. We will go a little bit bigger.
We do use furnace brazing. It's a partial vacuum furnace. I will show you a picture of our furnace in a second. We run 24-hour production in three shifts. In Richmond, we are only running two, but all the other sites run three. We do have robots around the world, again not in Richmond because we are small potatoes.
Every site has a 5-S program. We are all ISO-9001 certified, which maybe you are familiar with. We all have ASME stamps, we all have PED certification, and we all have U/L approval. It's one of Alfa Laval's goals to have the same product certification around the world. And I know here in America, there is BHEs that were made in any of our factories being installed and used, because we do ship globally.
It's only been two years I have been making them in Virginia. There are a lot of BHEs in the US made overseas. Our manufacturing set-up is a traditional U-shaped manufacturing set-up where you bring material in, you process it, and it goes back out the door. We have stations where one person works a station. We have preassembly where connections were put into frames.
The next station is where the channel plates are all stacked on top of each other, built into a grid, and rolled into the oven. We call it an oven. We talk like we are baking a cake, but we are actually brazing metal. But we do say we are going to roll it in the oven and cook it.
And then there is the testing station, where we test at 1.43 times MAWP, so we do it in a closed chamber. We use QR codes for material traceability and maintain certificates for everything we buy. Even though we are not required to by U/L, we do. I handle way too many MCRs, I review way too many MCRs. Thank you, Mike, for teaching me how to do that way back when.
We also have touch screens in production. I'm fascinated by the fact that we have touch screens in production, because we don't have that in all of Alfa Laval, but in brazing we do. This is the door to the brazing furnace. The furnace is about 12-feet-tall, and I'd say 20-feet-long.
This is our certified brazing operator standing here looking inside trying to decide if what's in there looks good or not. He's sitting here in the front row, if anybody has any questions for a certified brazing operator, who happens to be my husband, I will also admit. But he's also the team leader for the production cell. Brazing grids. When you build your product, the most important thing when you are brazing it is building that grid so that when everything gets molten and it stretches, it doesn't all fall down.
We have had things fall down in the furnace, so building the grid is important. The brazing grid consists of a solid graphite plate. The product sits here. We stack the product in different ways. There are fixtures to keep the product from touching each other, because you don't want the metal to touch anything it's not supposed to, because it will all stick together. You have to put dead weights on it because you have to have a certain amount of restraint. Otherwise, once the metal gets to temperature, it's just kind of floating there. It could go any which way; you have to restrain it.
Sometimes we don't restrain it well. These are the bad things that come out of the oven. The one in the middle, you can see back there in the second row, it all leaned over. It's resting on that element in the center of the furnace. This was a mess to clean up. Sometimes the fixtures stick to the product because the copper gets molten and flows wherever the copper wants to flow. It sticks to our graphite fixtures, and then we throw the fixture and the heat exchanger away because you can't break them apart. Sometimes the copper flows the wrong way on a connection. It's supposed to create a joint, but it just creates a puddle and spreads wherever it wants to go.
This picture here on the bottom left, there are tiny little pinholes in this braze joint. I got that with my cell phone. I was amazed that I was able to capture that with my cell phone. But sometimes pinholes just pop up after brazing. Just like welding, porosity happens. And every now and then, your safety relief valve goes off.
After manufacturing comes testing. Testing is so important. We test in a closed chamber. We load the product, and there is a computer control. When we test, we do a pressure test of 1.43 times MAWP on all chambers. Some of our products have two chambers, some have three, so we do test every chamber independently.
Then we do the leak test with helium. Because it's refrigeration equipment, they are running refrigerant through it. In addition to pressure testing like ASME requires, we also do helium leak testing. We pull a vacuum in the chamber, the rig, and then we insert helium into each chamber to see if it leaks out externally and also check for leaks internally into the next chamber, because you don't want your refrigerant mixing with your water or your process fluid.
It's expensive testing. This unit here takes us probably 30 minutes to run the full test. Then when it's good, the machine will tell you it's good. When it's bad, it will tell you it's bad. And when it's bad, that is when the expert must come over with the mirror, peek in the hole, and try to see if he could see if something is missing copper. It's not so easy to tell. Sometimes when you want to figure out if you have a crossover leak, we get creative. Sometimes you stick a rubber glove up there to see which hole the air is coming out of so you can figure out how to plug it.
We do rebraze things one time and only one time. We know that the material strength is reduced by about 15% when you rebraze it, so we have a policy that we only do it once. But if we can find the holes in the copper, we can put more copper on and rebraze it, and it passes sometimes. Sometimes not, but sometimes it does.
Field failures. So, the other thing I get to do at Alfa Laval is handle all the customer complaints that come in. Our number one complaint is actually transportation damage. It has nothing to do with the heat exchanger. It's that truckers tend to throw product when they take a curve. I buy stuff from Amazon, and it arrives to me just fine, very well packed, but for some reason our heat exchangers show up with bent connections, bent studs. So that's my number one problem: transportation damage.
Aside from that, it’s copper corrosion, which is, of course, going to happen in the refrigeration industry.
Mostly what I'm seeing, though, is cracks around connections. This picture at the top left, there is actually a crack in here that again I was able to take with my cell phone, no fancy equipment. Maybe you just have to know where to look. When customers hook up the connections, sometimes they will not secure the connection. You have probably seen this. You put too many loads on it when you hook your piping up, and then it bends. We don't reinforce the connection, it's not meant to carry loads, so when customers connect, they do need to be careful.
I told you we ship 25,000 heat exchangers a year; 80% to 90% of them are U/L rated. I think I did 10 ASME heat exchangers last year. U/L 1995 has been around for over 100 years. They have successfully been regulating our refrigerant-containing equipment for that long. They require periodic audits and come to my facility once a quarter. But they also require 100% leak and pressure testing by the manufacturer, and then I have to do this fatigue test for every model I make. I build two samples for each chamber that I have, we strength test it, and then we test for 250,000 cycles. I do it every year for every model.
So that fatigue testing stands out to me because I am an ASME committee member, and I'm very well versed in what ASME requires. But there is nothing in ASME about fatigue testing, and that's where my product fails. I fail fatigue testing. That's what's tough for me to meet. So, in my mind U/L is almost a superior code for this kind of equipment because of the way it treats the fatigue's properties. ASME requires you to have a third-party contract with an AIA. And I'm going to say this from the stance of those people who do not like ASME, because this is how it was told to me from U/L: That AIA, they are such a burden. You have to have a contract with this third-party AIA, and then you have to have certification on all your materials. Every piece of material, you need a certificate. And it's got to be a 3.1, and it might need to be signed off by the mill, and it better be legible. And if that digit runs off the right side of the page, the AI is going to make you get a new copy of that MCR.
And then you must have welding and brazing qualifications for your process, for your people, and then you have to renew their certifications. And then there is that metal nameplate. Again, I'm saying this like the U/L people – there's that big metal nameplate that you have to weld on. For U/L, it's just a sticker. So, these are our weld coupons from Richmond. All the stud welding tests we had to do with the bend test, tensiles on the lap joints for brazing, we had to do macros on the studs. I didn't do any of that for U/L, it's just for ASME. I did have to do it for PED, though. So, PED and ASME, of course, are very similar.
So BHEs – brazed heat exchangers – they are reliable. My failures are cracks; they are not catastrophic; they are small leakages. They are efficient, and because they are compact, they are small. They are not carbon steel; they don't require a lot of repairs. They are pretty cool actually because we have got some really fascinating technology built in. We do 100% testing in the factory. We have got this fatigue test that we do that's quite onerous, and we meet all the regulations: U/L, ASHRAE, ASME and PED, because we ship it over into Europe. I'm willing to take questions if anyone has any questions. I will mention that if Mr. Jeff Oliver is here, I would love to talk to you, because you have a brazed heat exchanger that I hear you are looking for a certificate on.
Anybody have any questions, except Jeff?
MR. DAVID SULLIVAN: Why do you go through the expense of using helium gas for testing instead of some other inert gas?
MS. MARKS: It's my understanding, because I didn't choose, but I was told we use helium because of the particle size, the molecule size mimics that of refrigerants. It's just a little bit smaller. Helium is like the perfect size, tiny little particle size.
MR. JOSEPH BALL: Are there repair processes for them? If you get one that comes out of the field, you can unbraze it and braze it up again?
MS. MARKS: No. Well, we don't offer repairs on them. Now, I do think you will find somebody that will walk over with a little bit of copper. We don't repair them, though, no. We would remove them.
MR. BALL: Most of them are small enough, it's easier to replace it?
MS. MARKS: Yeah, right.
MR. WALT SPERKO, any questions from you?
MR. MASUKU: So, all things being equal, what's the useful life on those exchangers?
MS. MARKS: Twenty years, maybe 30.
MR. SPERKO: It all depends on how nicely you treat them. If you feed them well and take care of them, pat them once in a while, they last a long time.
MS. MARKS: That's right.
MR. SPERKO: Is your furnace that you do the brazing in an atmospheric controlled furnace? And if so, what atmosphere?
MS. MARKS: Oh, I shouldn't have had you ask me a question. I don't know that much about the furnace. Mr. Marks? Do you happen to know the answer to that?
MR. MARKS: Zero atmosphere. It's all done in a vacuum.
MR. SPERKO: There we go. So, there's no atmosphere, it's a vacuum furnace. Super, thank you.
MS. MARKS: There you go, yes. That's why you have a certified brazing operator.
MS. MARKS: The certification process works for ASME. Well, thank you very much. I appreciate the opportunity.