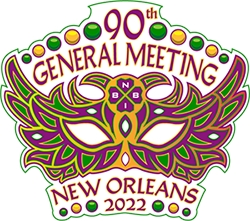
90th General Meeting Speaker Presentation
“Life Sciences and Quick Acting Closures in NBIC Part 2, Inspection”
Vincent Scarcella
The following presentation was delivered at the 90th General Meeting Monday General Session, May 2, 2022. It has been edited for content and phrasing.
INTRODUCTION: Vincent Scarcella is a Risk Control Director for the CNA Eastern Territory. Mr. Scarcella performs audits for NB-369, Accreditation of Authorized Inspection Agencies (AIA) Performing Inservice Inspection Activities, and vendor contract management. He is active on the subcommittee for NBIC Part 2, Inspection, and recently chaired the working groups for Organic Fluid Heaters, High Pressure Systems, and Quick Action Closures. Vinny is the vice chair for the National Board’s Board of Trustees working group NB-380, National Board Inservice Inspector Training Program, and is also an active member on the Committee on Qualifications for Inspection, chairing two working groups for that committee.
Mr. Scarcella’s slide presentation can be found here.
MR. SCARCELLA: Thank you. I would like to go over some of the items that drove these questions that came up in Part 2, that ended up with having a working group on quick acting closures.
I'm going to go over some of the exposures that we're experiencing and why recent events drove some of the actions from the committee. There's a couple other things I'm going to talk about. During this whole process with this working group, we ended up interacting with two other codes.
If you think about it, when something like that happens, you have to have a joint committee, because we'd like to all be on the same page. And I'm going to not read all of this stuff, because there's a lot of reference material. There's thousands of pages. And I'll go over the slides. If you have any questions, give me a shout.
I did put some of my personal history in here, because as a teenager, I became certified as a lab technician, which actually helped in some of the work that we're doing with quick acting closures and current events. Also, I was scene commander for HAZMAT, which actually also helped.
In the military, I was certified in several different laboratory processes. In a previous life, I actually did over 100 entries into biosafety level 4 facilities, which I'll explain a little bit as we go on.
First of all, I want to talk about the other working group members. And one of them is Jeffrey Petersen, who works at Idaho National Laboratories. He's absolutely great. He's joined several working groups that I've been on. He is a great intellect.
William Hackworth recently joined Part 2, but previously — William, you're in the room, right? Oh, okay. Speak up if anything comes up.
And, of course, Tim Bolden, who is a great leader at CNA, has been crazy enough to join several of my working groups.
We’ll move pretty fast. Any of the working groups that I work on, we turned it in in under a year. Going into Part 2, and I've been going there for over a decade, it seems a little frustrating when you see working groups that go on for years and years. And I vowed that when I got on one of these, that wasn't going to happen. So we try to turn them over in two meetings or less. We typically meet every 30 days or every 60 days.
These are just some of the things that came up that we were considering during this process, but the ones we're going to focus on in our discussion today are autoclaves and sterilizers, because of current events.
The nature of quick acting closures is they're different than anything else we inspect. Let's harken back to our test days where we were learning about efficiency. You had to plug efficiency in. And the joint efficiency was what? Ninety percent. And there was a one. And no, not the case with quick acting closures. Sometimes it's zero because the thing is open, right? And then how much pressure actually exerts on the mechanism to close it? Does it factor in the joint efficiency? So, it's not like the things that we're used to dealing with. The opening and closing, the cycling of these devices causes wear and tear, introduces stress.
And another thing about the nature of the minutes when things go wrong, the operators are operating oftentimes standing in front of them. So, if you go into Section VIII and you search on the word “accident,” it appears once. And it's in reference to quick acting closures.
So along comes COVID. What happens with COVID? Billions and billions of dollars of research money comes flying into the life science segment, which is a segment that John Spizuoco has me on as a technical resource. Is John here? Raise your hand, John. There he is, John Spizuoco, my boss. And by the way, he supports everything that I do in committee. And he even bothers to take the time to read a lot of the things that are going on and keeps updated. I really appreciated that. And everybody should realize that. Everybody working on these committees, the boss is paying for it, right? The decision-making, it costs money and it costs time.
Talk about in early days of COVID, the Centers for Disease Control actually classified COVID as a biosafety level 3, which really doesn't mean anything to you until you figure out what these codes mean. It's an ascending level – 1 being not the worse, and 4 being Ebola, to put it in perspective. You have to have an autoclave for biosafety level 3 and biosafety level 4.
Sterilizers and autoclaves need special operation of care. They need special maintenance, but where do we get all the new workers that came into the industry? You have an influx of maybe not the most knowledgeable people operating these things. And in the past, we know that the human interaction has been a factor in failure.
In comes an item to Part 2, and we'll go through a little bit of the process. But suffice it to say, and we knew this long before COVID, if something can aerosolize, it's more infectious, it can spread quicker. And one of the other things is there's a lot of times in a biosafety level 3 or 4 environment where an inspector might have to interact. So we had to deal with that and we're dealing with that with our working group right now.
I'm not going to go through BMBL, Biosafety in Microbiological and Biomedical Laboratories. It references the National Institutes of Health design criteria for laboratories. What's important about that is that it references ASME, BPE, Bioprocessing Equipment, which is important to us. This is a roundabout way to say that everything in that laboratory that's a pressure vessel has to meet ASME Code. So that's the only reason I'm really mentioning it.
By the way, that's several thousand pages of documents to review to try to figure out if there's things in there that we should be letting members and inspectors know about. I'm not going to go through in the interest of time, but there's information and there's references for all of the information here.
The goal in all of these codes from the CDC and NIH is to prevent a lab-associated infection. So if you're a chief in Washington state, what would happen if you get a call from one of these facilities and it's not like a regular call. In a laboratory, you have all these standard operating procedures. They were all developed because of risk assessments that were done for every single process that they have going inside the facility.
And if you're in New Jersey, for instance, you have to inspect HVAC systems. If that HVAC system is over the top of a biosafety cabinet, it has a HEPA filter in it for a reason, because there could have been a pathogen caught in the exhaust stream. And so before you go into an inspection on that, wouldn't you want to decontaminate it? Probably a good idea, right?
But other than the HVAC system, another point where the inspector may be coming in contact with the pathogen is in a sterilizer or an autoclave. So those two also have to be decontaminated. But more than that, in an autoclave in one of these laboratories where there's a pathogen, one end of it is in the dirty end, let's say. So that's in the laboratory where you have these infectious diseases. The whole thing has to be decontaminated before you can go in.
Also be aware that not only does it have to be decontaminated, but if you're dealing with an infectious disease that, say, maybe has a high mortality rate for somebody that has asthma, the owner-user should be called. You should be talking about that. And you may not even be able to go in if you're an asthmatic. And the same thing goes if you're a cancer survivor. If they're dealing with something that could actually impact your health, you may not be able to go.
And one of the facilities that I routinely made entries into for over a decade, if I had owned livestock, I would have to quarantine after leaving the facility. You should be aware of those issues and it's something to discuss and be prepared for.
So, codes. I already mentioned a few. But actually, in my interactions with the National Institutes of Health, they didn't know how I got from where they are to the point where everything in there has to be ASME Code compliant. So it was actually a pretty interesting interaction. We assumed that people that are dealing with these things are well-versed in all of them and maybe not. You have to be on your toes a little bit with it.
So ASME BPE and B31, but in addition there's a couple other things that come out of the NIH design criteria. There's a Factory Acceptance Test, which is a great thing to have. And let's be clear, the people that run these laboratories are smart people. And they're excellent at keeping records. It's part of what they do. It's part of their DNA. And so the Factory Acceptance Tests — there's a Site Acceptance Test and there's a Project Validation Plan. All of these things are great reference material.
So here we come to it. The group is working on going through all of those codes that I was just discussing. And, of course, we went through ASME Section VIII. Is it UG-35-3? UG-35-3 covers quick acting closures. But in addition, in Section VIII, there's an Appendix FF, which we needed to go through to make sure we were going to incorporate those things that made sense and to NBIC, Part 2.
The testing interval — we're still in the modes of trying to figure out what that should be. There are some hurdles like what size? Is the tabletop sterilizer going to have the same NDE requirements as the autoclave? And some of these you can roll a train car into. They're large. Should they have the same requirements?
There are still things we have to work out. And we presented the start of our proposal in January. We just got it last July. And I think we'll be done with all our changes. There are actually 53 changes to the current part in NBIC covering quick acting closures. It's been a lot of work. Right now Luis Ponce has actually got the staff working on getting drawings in and diagrams, because not everybody knows what these things look like.
And there's several stories – when we're going through this, the NDE part didn't look right. It was outdated. So we went to Part 3. And we said, hey, Part 3, because Part 3 would be more involved with NDE, these are the changes we recommended.
And we recommended to Part 3 that we adopt ASME Section V, T-120, which is something everybody that's dealing with NDE needs to review. And I was just talking to Jason. Raise your hand. Jason is on the Section V committee and we're going to collaborate on trying to get some continuity between ASME and all of the NBIC codes.
And so Part 1, we're recommending that we get mandatory pressure switches that prevent the opening of the vessel and also an automatic dump switch if you hit an activation, the travel switch on the door, and try to open it up with pressure on it.
Most of the things that you find have gone wrong with these involve the wear and tear on components, closing components, and stress involved. If you haven't inspected one of these before, there's a lot of nightmare discussions. Craig shared one with me about a failure. And Chief Kinney, are you in the audience, Chief? He shared one about an autoclave failure in his jurisdiction. And actually, Chief Kinney is helping with the NDE requirements in getting that between Part 2 and Part 3, we'll have some continuity there.
Any questions?
MEMBER: I just wanted to ask how was the decision made to do the nondestructive testing based on time rather than cycles of the door closures?
MR. SCARCELLA: That's an excellent question. And simply put you know about isostatic presses, and we deal with cycles, and we just did this when we updated HPS in Part 2. The cycle discussion is rather complex. And how many times did we go into an isostatic press and find out they haven't been counting the cycles? And then where do you start with from that? And it's just a lot simpler when you track five years. You have to make some changes to the actual device before you have to change a part. One, instead, put something in to count the cycles, actually. And I'm not aware, unlike Div 2 vessels, ASME Div 2’s are built to cycles. You'd actually have to engineer it and, you know, reverse engineer it and find out how many cycles is the thing good for before we can actually do that. It just seemed a lot simpler to go for five years.
Thank you. Good question.
MEMBER: Do you have any idea of what acceptance standards you guys are planning on using?
MR. SCARCELLA: We go by Section V, right? And it's going to involve the OEM deciding and the NDE engineering, not us. We're not going to write acceptance standards. That's beyond the scope of Part 2. That's not what we do. We're going to have to rely on the NDE world to actually figure that stuff out.
MEMBER: Also, as far as time limit for an implementation, are you planning on getting this out at the next revision cycle?
MR. SCARCELLA: We're going to try to get this in for July. Hey, Luis, how fast are we going to have those drawings?
MR. PONCE: Probably not for this cycle.
MR. SCARCELLA: Okay. So we're going to miss the cycle. It's not my fault. (Laughter.)
MR. PONCE: I think we should do it without the drawings.
MR. SCARCELLA: That might be an idea. We can talk about that before July. But let me be clear, the staff that works on this, we have Jodi, I have Jonathan. Luis, I mean, how many emails have I drove you crazy with?
MR. PONCE: Kimberly is also working on this.
MR. SCARCELLA: We have a great team working on it. And I forgot Chuck, Chuck Becker, right? Is Chuck in the audience? We recently added somebody to the working group who had 17 years of experience just in construction of these, so that helps.
MEMBER: Good presentation. I think we often forget the visual is part of NDE. I can tell you that there's been three recent failures I'm aware of in which two of those three would have been easily caught by NDE. One of those was a fatality. And when you have modifications to the doors and such, it's pretty easy to see when someone is doing something wrong. The manufacturers also recommend, almost every single one of them, a daily operator type inspection routine. Yet they know it, maybe we can look towards a CSD-1 type approach or say, hey, that's what you need to be doing. We do for our customers. That's normally where their awareness falls short though. You also have to remember a lot of these, I know life science is one, but you get in the carbon industry, you have 50 or 100 of these and you got thousands of workers there, but that's where they're going to get killed at.
MR. SCARCELLA: Right. Absolutely. One of the things that happens with these, and I think we have to really massage some of the language in Part 2, is that the gasket doesn't get changed. So you're constantly pushing on this gasket and over time it wears and nobody is inspecting it and it can get stuck. And that's when you come up and do your inspection and you find there's a crowbar sitting against the autoclave and something bad is going to happen. I guarantee it. There's story after story of people finding cracked and missing hardware or hardware on these things. The visual inspection is critical. And we need to give the inspector the right tools so that we can get the right inspection. And we need to give the members enough information that they have good reference information to get the job done.
Yes, Milton.
MR. WASHINGTON: Yeah, very good presentation, very informative. One thing I wanted to ask you in Part 2 in your working groups that BPE process, of course we're limited as to what we can put in this Section 2. Would it be beneficial for those jurisdictions to adopt ASME BPE to help with that regard, if it's possible, or reference this account so that we can utilize that?
MR. SCARCELLA: If it was me, Milton, absolutely. We've known each other a long time. I think it's a good thing, because not everybody is going to follow CDC or NIH guidelines. And adopting BPE, ASME BPE will cover that- a lot of the things we're concerned about.
One more question.
MEMBER: Sir.
MR. SCARCELLA: I'm Vinny. You can call me Vinny.
MEMBER: Vinny, when you get to the closure ring mechanism, are you also going to talk about the back pressure O-ring type closures?
MR. SCARCELLA: See, I don't know how deep we should go. And actually that's what bringing Chuck on the team has been helpful in that, but what is the average inspector capable of and what should they be doing and what should an NDE expert or maintenance expert on these things are doing?
We have to find that line and not try to make the average inspector, you know, we don't want to stress that. So maybe they should be making sure those things are done and making sure those records are kept, but not necessarily doing an in-depth inspection on a piece of equipment that they're really not familiar with.
That's it. Thank you very much, everybody. Really appreciate it.