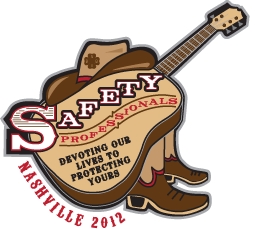
Potential Detrimental Consequences of Excessive PWHT on Pressure Vessel Steel Properties
The following presentation was delivered at the 81st General Meeting on May 14th by Dr. Carl Spaeder. It has been edited for content and phrasing.
Speaker Bio: Carl Spaeder is a private consultant on metallurgical issues and properties of high-temperature metals and welding problems. It's this expertise that has made him a key player with organizations hiring engineers for specialized projects. Dr. Spaeder received his bachelor of science in metallurgy at Penn State before earning his master's in metallurgical engineering at Carnegie Mellon University. He was awarded his Ph.D. in metallurgical engineering from the University of Pittsburgh. His career started in 1957 with USX Corporation. He joined Lehigh University where he served as a senior research engineer specializing in welding and related projects. In 1990, Dr. Spaeder joined Aristech Chemical Corporation as the senior staff materials engineer. Leaving private industry, he opened his own consulting organization in 1999. Dr. Spaeder has been active in a number of industry organizations, including ASME, the American Society for Metals, the American Welding Society, and the Welding Research Council. In addition to being a professional engineer in the Commonwealth of Pennsylvania, Dr. Spaeder has published numerous articles in some of our industry's most prestigious technical journals.
Dr. Carl Spaeder: The format for my presentation is to give you some background on the present code rules and an overview of postweld heat treatment issues. We are going to talk a little bit about stress relieving some of the older steels, like 212. Some of you may recognize ASTM A-212 as the forerunner of the 516 and 515 materials. We will look at work by John Barsom, a mentor of mine, and the postweld heat treatment of modern steels. And then I'm going to talk to you about some things that should be reconsidered by the code. I use a lot of terms interchangeably: reheat cracking, postweld heat treatment, PWHT.
Postweld heat treatment was reported as being highly desirable in the early 1950s. In fact, the book by Stout and Doty makes that point. And a beneficial notion became engrained in common in-house welding programs. If you want to see a one-way street, some of the producers and fabricators thought you had to postweld heat treat. It can be detrimental in certain steels. It has no benefit in some modern steels. And we need to apply the technology from other disciplines. For example, the fracture control plan that's been developed for bridges is a great opportunity to take technology from another area and apply it to the National Board Inspection Code (NBIC) rules. In terms of beneficial effects, it improves the toughness of certain steels, especially steels with high carbon content. It mitigates stress cracking in some service. It outgases hydrogen. The need for outgassing is mitigated by the ability to use strict low hydrogen practices and get away from that problem. It removes residual stresses, and that's important in stress corrosion cracking surface and for dimensional control. There are times when postweld heat treatment is needed for those issues. Overview of postweld heat treating effects: degrade toughness of some steels, introduce microcracks that are not readily found in routine nondestructive examination, and it's difficult to rule out reheat cracking because of the complexity of the heat affected zone. And that's a key point. You can't rule out what steels are susceptible to reheat cracking.
Back in the studies on the Liberty ships that were breaking up in dock during World War II, there was an awful lot of work done by a fellow named Polini at the Navy Research Lab, and he identified some very important things: Residual stresses are important in terms of brittle fracture only with low toughness. When a postweld treatment is undesirable, elastic plastic toughness corresponding to the presence of stresses equal to yield strength should be required. This toughness value allows the omission of a postweld treatment in the absence of issues such as stress corrosion cracking or dimensional considerations. A graph fromthe original Stout and Doty book on welding, Welding Metallurgy, clearly shows that with an A-212, which is relatively high carbon steel, stress relieving is quite beneficial. But on the other hand, we will see it’s not a universal conclusion. It takes a look at the interaction of critical flaw size, stress range, and toughness.
It's rather important to understand the interaction between notch toughness and crack flaw size, stress range and fatigue life. But one of the interesting things was that the stress range turns out to be very important. The crack growth rate is proportional to the power of three, so it's a very powerful effect. And the role of stress concentration effects needs to be recognized. And that really boils down to workmanship.
Workmanship is always very important. Crack arrest can be achieved with some steels that exhibit very high toughness. Some low carbon steels exhibit high toughness approaching the austenitic stainless steels, such as 304. So you can get some really remarkable toughness nowadays with modern melding techniques.
We are going to talk a little bit about the postweld heat treatment of modern steels. There is an ASTM specification covering high-performance steels primarily for bridges, and John Barsom helped write this specification. One thing they tried to feature in the materials was to design for ease of welding in terms of things like preheat. It doesn't do any good to have a welder weld something in a confined space with very high temperature preheats. You are cooking the welder, and when the guy is being cooked, he wants to get out of there as quick as possible. He doesn't do as good a job.
Some steels have toughness similar to the austenitic stainless steels, they go up as high in yield strength as 100 psi corresponding to the 517 steels, and some of these steels are susceptible to postweld heat treatment cracking, particularly the higher strength. A rule of thumb: the higher the strength, the more likely it's going to be sensitive to cracking.
We are going to talk about a number of documents and consider them in the following order: the Welding Research Council Bulletins, the Doty papers, and some rather interesting work from the Welding Institute in England in a March 2006 Welding Journal. The original work on postweld heat treatment was done by Bob Stout at Lehigh, and it's a very good overview of postweld heat treatment issues. He identified postweld heat treatment as desirable for high carbon steels; marginal benefits for the lower carbon steels. He identified vanadium as being very important. He made the point that postweld heat treatment is not required if residual stresses can be dealt with successfully, and little benefit with respect to fatigue. So he put a nice spin on things and gave us a good starting point.
When I was at Lehigh, Bob Stout and I gave a few short courses together. He was an interesting guy to work with. One of my colleagues at US Steel was Paul Konkol, and he did some studies on a number of steels, A-36, 537, 572, 588. The conclusions he came away with were that the base metal strength and notch toughness are generally degraded by long postweld heat treatments. Heat affected zone and metal toughness are affected by welding parameters. And sometimes you might be surprised to find that the heat-affected zone has the best properties of the whole weldment. It was an interesting finding, particularly as with roll steels, because the welding process itself normalizes those steels and brings up the toughness. There was a Bulletin 395 again by people at Lehigh, who did many studies of vanadium and molybdenum additions.
These additions tend to degrade the Charpy V-notch properties of normalized and tempered base metal and the heat affected zone. The level of degrading is a function of the specific composition and welding parameters. Back when I was at Lehigh, D'or Doty and I did a report on the effect of postweld heat treatment. We identified that the code permits the elimination of a postweld heat treatment when steel exhibits high notch toughness at the service temperature.
The use of a postweld heat treatment is likely to degrade the service performance at the intended service temperature of some materials. The above criterion has been applied generally in code cases, except for the P-8 materials, which are the austenitic stainless steels which typically are not given a postweld heat treatment. Those types of steels are seldom given a postweld heat treatment unless there is some special need for doing that. And actually there are better ways to do it. Glass bead peening, for example (put the surface in compression), is a typical way to do that. We identified some needs in that bulletin for rules to eliminate postweld heat treatment: When it can be justified on the basis of notch toughness in the as-welded condition. Postweld heat treatment needs to be eliminated when reheat cracking is a distinct possibility. And one of the important things to recognize is reheat cracks are very difficult to identify except by nonroutine examinations. So unless a guy cuts out a sample and takes a look at it under a microscope, he might very well miss reheat cracks.
There were some other studies done, and they showed that one of our classic high-toughness material, 516, is degraded by postweld heat treatment. They also identified that the postweld heat treatment follows a Larson-Miller relationship, and reinforced the earlier studies showing a postweld heat treatment is not a universal good. So again, a lot of good information out there.
Doty wrote a paper in the 1960s trying to alert people to the general nature of the reheat cracking issue. For a long time people thought reheat cracking was just associated with T-1 steel, which is steel that US Steel developed and was one of the first steels that identified this issue. And some, like the German people in their metallurgical evaluation, referred to postweld heat treatment as the T-1 disease. But it showed that there were a lot of steels that were susceptible to reheat cracking.
There was another study done by Doty and Ed Szekeres, and this paper details the experience with T-1, 9% nickel and HY-80, and reports that these steels generally do not require a postweld heat treatment. And these steels are successfully used in the nonstress-relief condition in bridges, storage vessels and military applications. HY-80, for example, is used in submarines, and you don't want a submarine that gets hit by a torpedo to crack. So this was a pretty important finding. And there are some really decent studies that were done as part of these things. There was Operation T-1 and there was a special study with Chicago Bridge & Iron where they actually made full-scale vessels and broke them up. There is good literature out there that many people have never taken a look at.
The TWI studies reported in the March 2006 Welding Journal referenced work to justify exemptions from code rules requiring a postweld heat treatment. The TWI view is that fracture mechanics can be used to justify departure from code rules by showing steel has sufficient toughness. It's not rocket science and Doty and I alluded to that in the paper we wrote back in 1993.
Some code rules need to be reconsidered. There is a compelling need to revise rules for lethal service. Presently the code requires a postweld heat treatment even if the postweld heat treatment degrades notch toughness and possibly introduces reheat cracks that under routine inspection will go undetected. In my view this is a very serious issue. Add rules to the code that eliminate a postweld heat treatment provided fracture mechanics analysis confirms that weldment exhibits sufficient notch toughness to preclude brittle fracture over the life of the vessel. And lethal service should be expanded to include vessels that contain huge quantities of liquefied flammable gases where a vapor cloud explosion is a possibility in the event of a major leak.
A vapor cloud explosion can cause a number of injuries and deaths if the event occurs in a populated area. When I worked with Aristech Chemical, we had vessels that contained large quantities of polypropylene, and we were always concerned that the vessels were located downwind, but you can't count on wind direction always being favorable if a vessel breaks up.
Going forward, the written form of this report is being considered by the various code committees in this meeting this week. It takes a lot of time sometimes to change the code. Probably the most important observation is that it is very difficult to say a particular steel is fully immune to reheat cracking because of the complex nature of the multipass welding and the nature of the heat-affected zone. You just can't rule it out with certainty.
Question and Answer Session:
MR. CANTRELL: Chris Cantrell from the state of Nebraska. Do you think the postweld heat treat tables in Section 1 and Section 8 are adequate, or are manufacturers using those actually inducing defects into their product?
DR. SPAEDER: Well, I think that's a question for the code bodies to sit down and go over. I made a presentation at the ASME code meeting in 2010 in Washington D.C., and I have the sense that people recognize we have to go back and take a look at all the code rules and make sure they are okay. In fact, my understanding is that we can move from some of the stringent rules in there right now in some of the materials, like 516. But that's a job for the code committees, and it takes a lot of time. It was sort of interesting that Domenic Canonico, who got the award today for safety, was one of the hard-nosed guys that took the position that you always had to postweld heat treat. And Domenic and I go back for a long, long time. But it's sort of interesting to see that some of the people that had very rigid positions are now softening their positions and recognizing that you probably don't always want to do a postweld heat treatment, particularly in lethal service. I think that's a classic case where it just doesn't make sense to have a rule that you always have to do a postweld heat treatment, even if you are degrading properties, especially cracks that you can't detect. That seems to be a no-brainer.
MR. WALTERS: Joe Walters from Travelers. Why are the reheat cracks so difficult to find with normal traditional NDE?
DR. SPAEDER: They are very small and the orientation is hard to predict. You may not see them in a radiograph, but it takes a lot of guts to have some very small cracks and say you have got to redo these welds. Going back to very early studies, when they first tried to get T-1 into the code, there were eight or ten pressurized vessels built. They literally dropped ingots on them, and found that the steels with the high toughness did very well and the cracks didn't propagate. But they went back – they actually at the time weren't looking for reheat cracks, that hadn't been something that people were generally looking after, and they went back after some other issues – after it became apparent that steels like the T-1 could develop reheat cracks. They went back and looked at some of those vessels and actually found cracks in them. You don't pick it up by routine nondestructive testing.
Meeting Attendee: How do you pick them up?
DR. SPAEDER: By cutting a sample out and looking at it under a microscope at 100X.
MR. STURTZ: Jerry Sturtz with Arise. Would technology like plastic replication be able to detect that type of cracking?
DR. SPAEDER: Well, I'm sure there are other techniques, and if you present this to the NDE specialists, they will find a way to do it. But the routine things we have in place right now, you are not necessarily going to catch them. There was more work done on reheat cracking at US Steel than any other problem that ever existed. There were always at least two or three projects in the 30 years that I was with US Steel, and it just is unbelievable. The one thing that they did find is that there was a pretty marked correlation between cracking and the amount of ductility in a creep rupture test, the short-time creep rupture test, which you would expect. So there is just a whole raft of information. There is no problem that we have done more research on and dragged our feet so long on.
MR. SKALNIK: Larry Skalnik with CNA Insurance. Do you have any case histories attributed to excessive postweld heat treatment?
DR. SPAEDER: I don't personally, but I have seen the results of the loss of toughness. They are pretty well documented. But you have a two-edge sword, because when you do the postweld heat treatment, you are bringing down the residual stress, so that's beneficial to you, but at the same time you are degrading toughness. And it doesn't make sense to do a postweld heat treatment if you don't have to. It’s a cost type of thing. We need to be a little smarter in some of these things.
DR. LAU: My name is Ken Lau. I have two separate questions. One, you were talking about FBQ A-212, that's 516-70-type material. I'm not in the materials side, but I understand that postweld heat treatment for an extended period of time is when you really degrade the material. But the code does not talk about how long it needs to be. It just says what's the minimum time. That's the first question. The second one is you also talked about T-1 like 517-type material, which we use a lot in carbon transport. Now, the 331 spec, USDOT spec, actually was more stringent for the longest time than the ASME code, and they respect the thickness. For instance, for UHT we actually say only more than 5/8 thick. Would you comment on that? Because they seemingly have specified it could be because of what they transport, carbon 331 types of tanks, everything would be up for heat treatment?
DR. SPAEDER: I would like to get your question in written form and then try to respond to it. But when I was at Lehigh, there was a utility that had gotten a warning on postweld heat treatment on fans. They routinely looked at their fans every three months and found cracks. After a few years they sent me a sample – a two-ton piece of steel – out of a $100,000 fan. And when you are at a university, a sample that weighs two tons is exactly what you are looking for. But when we looked at the samples, we found there was overlap, not reheat cracks, and the people misinterpreted the inspection results. They were interpreting overlap as cracks, and basically they scrapped a perfectly good fan. I had to go back to the people who sponsored the project and explain they scrapped the wrong fan. So, it's really a very complex subject. There is an unbelievable amount of literature out there, and it's time for us to bite the bullet and take a hard look at the rules and make sure that we don't have things in the code that don't make sense.
MR. HILTON: Ed Hilton from Virginia. You are talking about eliminating postweld heat treatments by analysis. Is the analysis of the parameters going to be set in the code; is it something that a manufacturer or repair company could use?
DR. SPAEDER: My experience with the code is that they try to give directions on how to do things. ASME expects the engineers doing the analysis to know what they are doing, and this is not always the case. In some codes they want to tell you exactly what to do and take all the engineering judgment out of it. ASME tends to want people to do an analysis themselves and satisfy the customer. It may very well be a decision between the owner and the fabricator that the fabricator says that for these types of things this type of analysis will do, and based on this analysis as the owner, are you comfortable with this analysis. Walt Sperko, Chairman of Section 9, was one of the guys that monitored the project, and he's shown studies where they use a fracture mechanics analysis to say that certain materials shouldn't be given a postweld heat treatment. So I think the rules and how they handle them are probably not going to be published in the next couple of weeks. It takes a lot of time for people to sort these things out. (But the philosophy has now become apparent that postweld heat treatment is not always a good idea.) Once you accept that notion you can figure out and do rational rules.
DR. CANONICO: You say extended postweld heat treatment. What do you mean by extended?
DR. SPAEDER: Well, the Konkol studies, for example, were out to 100 hours.
DR. CANONICO: Oh, that's too long, no question. Section 11 controls the length of time that you can do postweld heat treating, and still you must pass the requirements of their code. So the code doesn't require 100 hours.
DR. SPAEDER: Well, I appreciate that.
DR. CANONICO: And most companies would never use 100 hours, I don't think. We have done a lot of studies showing the effect on Charpy properties for extended periods of time, long times like you are talking about, 100, 150, 200 hours. The other point I was going to make was on reheat cracking. There was a lot of work done in the early '80s, '70s, back in my area on bridge, and there is at least a rule of thumb based on chemical analysis, as far as reheat cracking is concerned, that is good guidance. We did a lot of studies on 533 where we ran into reheat cracking, and we found out it is mostly bad residuals, the tins, the antimonies, and materials you don't anticipate are there.
DR. SPAEDER: Well, you are perfectly correct. A lot of times tramp elements get in there, and a lot depends on the producer, whether they are making their steel from scrap or whether they are making it from steel that comes from the blast furnace. It's hard to put your finger on exactly what the real cause of it was. But modern technology in steel making has become so advanced that there are some things we can do now that we couldn't do 20 years ago. For example, most of the stuff is continuous cast iron, and those steels tend to have some aluminum in them, so you can continuously cast them. So essentially you are not going to find the 515 steels available because they aren't going to have aluminum in it. Of course, a lot goes back to some bad studies. There were notions about the effect of the grain size, for example, on 515 and 516, and some of those were lousy studies where the creep tests weren't taken out very long and people misinterpreted the data, and that data is long gone. That goes back to Dick Miller's days. There are many things in the closet that some of the old-timers know that young people don't know about.