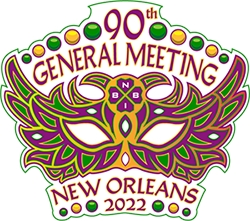
90th General Meeting Speaker Presentation
“Remote Technology and Digital Logs”
Patrick Jennings
The following presentation was delivered at the 90th General Meeting Monday General Session, May 2, 2022. It has been edited for content and phrasing.
INTRODUCTION: Patrick Jennings is the legislative affairs director for The Hartford Steam Boiler Insurance and Inspection Agency. Mr. Jennings has worked for HSB for over a decade and currently works for the inservice inspection department, overseeing jurisdictional issues. In total, he has over 35 years of experience with boilers, from small hydronic boilers to large utility units.
Jennings currently participates in several committees, including NBIC Part 1, several ASME Section I subcommittees, ASME CSD-1, and the NFPA 85 subcommittee on single burner boilers. He maintains a National Board Inservice Commission (IS).
Mr. Jennings’ slide presentation can be found here.
MR. JENNINGS: Let me be the first person that says it's good to be back. I think that's been said about 300 times from all the people that I've talked to. It is good to be back. The intent of today's discussion is to talk about remote technology and how to use it. There are several themes that I've heard this morning from the table up here. One of them was how things have changed. Some of it was very rapidly with COVID, and some of it is just the necessary changes that are needed in our industry.
What I'm going to talk about today is the logs. The logs are one part of our toolkit that we use for inspections. These logs are provided to the customers, and it gives them the ability to look at trends, it gives them the ability to monitor. And the inspector comes in and he looks at them and says, okay, you're doing the work that you need to do or you're not, you need to improve it, etc.
With all the technology that's out there and available today, I have one question. Why are we still using paper? There's a lot of technology out there. Why are we still using paper? Now, of course, there's a very good reason for that. And that main reason is that's what we have now. But we believe that there's a possibility of going past this. And that's what the topic of today is about.
I'm going to talk about a couple things. One, remote technology. There's a lot of really good work going on in the industry now around remote technology. Those remote technologies are visual and NDE primarily.
We'll talk about the current status: where we see the problem in terms of what's needed out there next and what's the next thing that we can do. And then, again, the entire reason for me being here is to start this conversation. We don't have all the answers, but I think we have some really good questions. And I'd like to get you thinking about those questions.
There's a lot of people talking about remote technology. There's a lot of people doing it. It really started with asset management. Somebody that has a large pressure vessel or a refinery column or a large utility boiler, they don't want a scaffold three or four stories up just to find out that they don't have to do work up there this month. They might go up and they'll use the drones or remote technology to identify what they're going to do. Asset management really started the driving of the remote visual inspection. And then there's also the NDE with the crawlers that go up and down.
When COVID hit, this really led to a great opportunity and a challenge for the industry, because there was no travel allowed. A lot of travel was disallowed, so how could we do our shop inspections? That’s where there was a code case. The QAI-1 Case 6, as well as the corresponding NBIC Inquiry RCI 19-02 that allowed remote inspection technology.
This remote inspection technology really is used to address safety issues. In places where you have a permit required confined space entry, it makes a lot of sense, because those are really identified as something that is important. And there's also language that's being discussed around permit required confined space entry.
There was a side benefit, and I consider it a side benefit, because I don't think it's the primary. The side benefit is that there's cost savings. All of this work, though, is for large applications, large utility, large pressure vessels that need massive infrastructure.
But the question is what about main street? I like to joke. I said, we're not going to go out and fly a drone into a dry cleaner to do a remote inspection. It just doesn't make sense. The needs for an inservice are really different than the needs for the large inspections. And main street is where we do most of our inservice inspections. We do the visual externally. We do the visual internally. We witness those control testings and safety control device testings, as well as a logbook review.
Typically, this is smaller equipment, shorter visits. And again, the time savings and the risk avoidance are a lot harder to justify with these drones or this other remote inspection technology. This is where we believe that IoT, or the Internet of Things, with connected devices, however you want to use that moniker, comes into thinking. We believe that this has a potential to supplement our inspections.
What are the elements of an IoT solution? What you do is you have your boiler out there or your pressure vessel, typically this will be boilers, so you have the sensors that you put around it. This is one of those questions I'm going to have. What should we monitor? You can do temperature, you can do a thermal switch, you can do pressure, you can do the presence of water, you can do vibration. Almost anything that you can measure, you can use as a sensor.
These sensors that we're using, as you can see here on the screen, they use what's called low-power consumption, long-range signals, or LoRa. That signal then goes back to a gateway and that gateway then sends the signal via cellular signal back to our cloud-based servers. On these cloud-based servers, we can now perform tests of this data. We can look through the data. We can try to find trends. We set these algorithms based upon our experience and based upon what we're looking for, so that we can identify situations that need to be alerted or just recorded as a digital log. If you get an alert, that alert would be based upon the severity of event at the time. If you have something that's very severe, you're going to let somebody know in the middle of the night. If it's something that's less severe, you might send them an email and tell them this is something you should look at.
Over time this technology that we're working with has gotten less expensive. And the way that we're currently using this IoT solution, and other companies are doing the same, we're not the only one, but they're also using it for property and casualty, loss prevention. And as part of that, we put the server out there. To add one or two or three devices to monitor the boiler, is actually very inexpensive.
Here's the questions. What can we monitor? What could be monitored? What should be monitored? And, again, the whole intent is along the lines of what is the purpose? The purpose is the boiler and pressure vessel's integrity and the safety. We have data. I'm going to show data where we can test that the customer is testing their low water cutout on a regular basis. We are looking at operational data, blowdown, on/off cycles, temperature differential. And then again, there's lots of data that we're using for property on the property side, water presence, humidity, temperature.
We can actually look at historical temperature or can pull in other outside data so that it can be all part of this big picture that we're trying to paint of the situation. And here would be a really good one. There's a lot of technology out there with the new boilers and they're connected, or they have the ability to be connected. What if we can tie into that? What would that look like? How can we use that data? A lot of potential issues, a lot of concerns that we would all have to go through. And, again, this is part of the reason we're here: to start this conversation.
Customer acceptance. One of the things we found and one of the things we believe is that the customer has to accept this data. It has to accept this technology. We are not out there to punish the customer. We're out there to reward the people that are doing things well, and we're out there to encourage the people that can improve to improve.
Cyber security. It's hugely important. All of our systems right now are air gapped. Everything that we do is on our system completely one hundred percent separated from their system. We think that cyber security is something that would have to think about, it's part of what we're talking about.
Obviously, if you're measuring more things, you're looking at more things, and you're looking at things more closely, there's going to be responsibility and liability issues. Again, those would have to be worked out.
Invasiveness. There are two types of invasiveness. The customer acceptance that we talked about, as well as the invasiveness of the equipment inside the boiler room. We don't want to be too invasive. So, there's a balancing act that you have to do. Again, if we're going to work with other vendors, there's going to have to be standards, there's going to have to be agreements, there's going to have to be discussions about what's appropriate.
Let's talk about a couple case studies that we've done and why we started with where we started. First one, space heating, as you well know, is a large part of our business. We do a lot of heating boilers. We had a client that we worked with, and we went out there and we looked at their population.
This client, a large client, has a lot of space heating. We focused it first on the cast iron boilers for steam or cast iron boilers, because they have failures with cast iron boilers. I'm sure none of you have ever seen, right?
Seventy-two percent of their boilers are hot water boilers and 28 percent are steam boilers. In terms of the claim counts, 81 percent of their claims come from hot water boilers, 19 percent come from the steam boilers. However, the dollar loss value when you look at the gross loss comes primarily from the steam boilers. Forty-two percent of their loss comes from 19 percent of their total claims. If you look at just the steam boilers, one-third of those losses are caused by failure of a low water cutout. These are low frequency events, as you well know, but they're very high severity. We felt that that was something that we really wanted to focus on.
Hot water heating boilers are very different. They're just cracked sections. Very cracked sections. Ninety-five percent of losses were cracked sections. They're not extensive, but they really dominate the loss history.
Here's an example of what we did with a steam boiler for this place that we had worked with. As you can see on the screen, this is a very typical installation. This is a steam boiler, a cast iron boiler with a flow type low water cutout. In these cases, if you have low water cutout failure, typically it results in the loss of the boiler. If you have a low water cutout failure on a larger boiler, like a process boiler, you actually have a much more significant potential event primarily because of the stored energy. We recognized that for the process boilers, this would be a really good target to go after, too.
One of the key things that we've done well is testing of those low water cutouts on a regular basis so that we know that they're working, they've been exercised, they've been stroked, and that is really key to preventing those losses. What we have is we can see where the blue arrow is pointing to the device that we put on simply measures temperature. And when that yellow valve is open, the water drains out of the float, the temperature rises, we've marked that, and we know that they've tested their low water cutout.
Here's some of the data that we have from this site. On the left you can see regular testing of the low water cutout. They're doing it really nicely. On the right you can see infrequent testing of the low water cutout. This is the case where the valve on the left you say, hey, you're doing a great job. Thank you. Keep it up. On the right you say, you know what, you can improve. Let's do better.
Here's another installation. This is a dry cleaner. Very typical that you'll see for a central plant dry cleaner where you have all of the outlying stores that send all their laundry to one place. This is a 150 horsepower firetube Scotch Marine. This boiler we can get the low water cutout IoT device, as well as the blowdown, because for process boilers, blowdown is part of your water chemistry. And it's a really important part of making sure that if you know that they're doing this, it gives you an indication, at least, that they're really paying attention to their water quality.
Here's the digital log for this dry cleaner boiler. Again, they're doing a really good job. Let's hone in and look at some of the data. It's just these two devices that we talked about. We now see that this boiler starts up around 6 o'clock in the morning. They test their low water cutout, they do their bottom blowdown, they run from eight to ten hours, and then they're offline overnight. And then for the weekend, they're offline. So not only do we know that they're testing their devices, but we’re also starting to understand their operation. This is the kind of data that we can say aha. You can set those algorithms and say something changed, what's different? This is really interesting.
We talked about those steam boilers. For the hot water boilers, it's a very different loss scenario/loss situation. These are the cast iron boilers with the cracked sections. These are higher frequency. They're not high frequency, but it's higher frequency, lower severity. Cracked sections, you know, you've all paid for cracked sections, but they're very disruptive. We’ve done some looking at the data analysis and it's most commonly during the coldest months of the year, so it's very disruptive.
Contributing factors for cast iron sectional cracking are high temperature differential, supply and return, cold water shocks, frequent cycling, or low water outlet temperatures. So, again, with two sensors, supply and return, we can look at the return data to say, yes, they're keeping the return temperature where it needs to be. You can look at the differential between the supply and return. This boiler manufacturer recommends a 40 degrees maximum differential between the supply and return. In this case and in several other cases, we found where they were running a 60-degree temperature differential across the boiler, which can lead to the thermal shock. People think of thermal shock as a singular event, but it's really an accumulative effect on the boiler. Every time you can stop one of these events, you're actually improving its ability of resilience to thermal shock.
A couple other things. So now that you have this data, you can look at things like cycles. Every time you shut off the boiler, you purge it with cold air if you have a hot boiler. Again, that's one potential contributor to thermal shock. In this case we can see that they're operating the boiler within the supplier's recommended cycle times. The other thing, and this was a little surprising to me, is that you can also find out when there's cold water being returned to a hot boiler. We actually found that some of these situations were occurring even when they had the mixing valves.
This is, again, just example data of how we can use IoT for the low water cutouts. We can use IoT for those operational parameters that help us prevent losses, because that's what it's about. If you can prevent a loss, you're going to save money, you're going to have a happy customer, and there's less potential for somebody getting hurt if we can prevent these losses. Remote visual and remote NDE are not going away. They will continue to grow their roles for the large equipment inspections, asset management, shop inspections. And we do believe there might be limited jurisdictional use of remote visual.
For example, I think it would be a good one for if you're in violation. But your day-to-day remote visual in your main street businesses we think is going to be a challenge. We've actually tried some of them with customers just to try the process out, and it's really difficult. Again, with the code cases, you have to have visual acuity, you have to have your lighting, you have to have certain requirements. And it's just going to be difficult, we believe, but not impossible.
We are currently using IoT for loss prevention services. Again, property casualty primarily, but we think the expansion of this into the equipment breakdown side is just a natural progression.
Can IoT be used as a supplement for – let's start with external inspections. Can we do that? Does that make sense? Could we use it to replace? If we had enough data, would you feel comfortable replacing an external inspection with a fully -- and if they're a monitored boiler, would you feel comfortable it's being operated well and is being maintained? Could we extend time intervals between the externals, if you're not comfortable getting rid of them, with the intra-board internals?
Before we get to this, we really have to figure out where we want to go, what do we need to do this, and what's in flight and what's needed. And again, if we're going to use vendors, you know, work with the vendors, we're going to have to have standards, we're going to have to have discussions with them about what this might look like. Again, we must overcome the concerns raised to get buy-in by all of the parties. Clearly this is not a replacement for trained inspectors. This is not a replacement for operators. This is the ability for our industry to improve the work, the good work that you do to make it even better.
Thank you.
I hope I have questions.
QUESTIONS
MEMBER: I've asked this for a year, because I'm a technology geek, is do you see something like we said – I have one place out in the middle of Minnesota that is 400 miles from – say I send them a GoPro, it's $50. Would you do an inspection, a visual inspection, over a GoPro? Yes. I own it. Test low water cutoff. You got a picture. I mean, you're doing a visual inspection. What's the difference between me looking at a drone that's 100 miles away?
MR. JENNINGS: We've actually tried that for demonstration purposes. It's actually more difficult than you think. First of all, the code cases that allow inspections for the shop, they actually have some specific requirements around the visual acuity, because you're looking at more than just the low water cutout. That's an easy one, right? But you're looking to have the visual acuity. You have the lighting requirement.
And then you have to have somebody that says, okay, walk me around. And it's no, no, your left, your other left. And eventually at some point they get frustrated. So we tried this and it's a very frustrating process.
We're not saying it can't be done, but that's something that's going to have to require some thought, some practice and some tryouts. Thank you.
MEMBER: You mentioned a lot of parameters up there. You didn't mention carbon monoxide. Is that one of the possibilities?
MR. JENNINGS: Absolutely. If it's something that you can measure, again, it's something that you set up and set alerts. Now, that goes back to those liability/responsibility type questions, also, because we all know that one.
MR. CREASER: Thank you for your presentation. I'm sure there's going to be awesome discussion on this in that I see and agree with you that there's probably some benefit to having that type of technology. I think some of the things that you said in some of your slides are that the constant connectivity and the cyber-attack and all of that could be eliminated by not having that connected that way.
MR. JENNINGS: Absolutely.
MR. CREASER: When you were talking, I was thinking okay, well, what if I came up to do my inspection and then there was a portal there that I had a connective device that I can connect to and see what that operator has been doing for the last six months with this boiler and go, okay, this boiler has been well operated. That would alleviate some of the things that I might focus on or direct me to some other things that I was not focused on. I think maybe one of the biggest challenges would be the actual internet connectivity and your client not wanting you to have –
MR. JENNINGS: Exactly. That's also why we started with the stuff that we have control over. That's one of those conversations where it's worth to have, but your point is well taken. Again, if we can do this monitoring during an internal inspection and get that data that they said they've looked at it.
MEMBER: My question is who has access to this information, just HSB and the client, or does the jurisdiction have access to it? Let's say a client leaves HSB and goes to insurance XYZ. Do they get to keep that information?
MR. JENNINGS: Perfect question. Again, the whole point of today was to initiate a discussion. That's exactly the kind of question that we really need to say. At this point, if it's data that we collect, it's us and the customer, right? But who knows.
MEMBER: Hey, Pat, have you discussed this with any jurisdictions to this point on whether this would be allowed or whether legislative changes or regulatory changes would be needed?
MR. JENNINGS: Yes. There will absolutely have to be legislative. There will have to be regulatory. There will have to be some NBIC type work. I've actually had several informal conversations with a couple of jurisdictions just to get a feel for is this something that's worth talking about.
And, you know, we got a good response that, yes, this is something worth talking about. Is it the right way? Is it going to be easy? I don't know, but we want to, again, start that conversation. We're pursuing some of this work. We're on it for loss prevention.
MEMBER: Pat, nice presentation. Thanks for bringing it up. Strong believer in technology in general. And I think we'd all be fools not to adopt some of it, but I also believe the inspection integrity needs to be maintained in that, you know, enhancing the inspection with technology is absolutely imperative.
MR. JENNINGS: Yes.
MEMBER: We can't replace the inspector. We can't think about --
MR. JENNINGS: Absolutely.
MEMBER: -- turning it into a widget process because I can tell you that the finer arts of inspection are those things that you may not be able to get to through remote.
MR. JENNINGS: That's exactly why we have difficulties with the remote visual, because, again, there's a lot of stuff, but can you do some of that work when you're doing your internal in your own site?
So right now, we're talking about this as a supplement to inspections, because we believe that you get more and more data, absolutely. Anything else would be further down the road after we prove that this process works and it's acceptable and comfortable to the industry, but you're absolutely correct.
MEMBER: Hey, Pat, I'm just curious what the overwhelming customer response is. Is this a big brother type view, or have they been receptive to the technology?
MR. JENNINGS: The people that we've worked with have been for demo – the data that I started with was demonstration. And they were very receptive. And some of those relationships are continuing. From the IoT, from the property services side, we just recently issued a press release. There was a 500 percent return on investment for our customers for doing this, so yes, it's working.
Thank you.