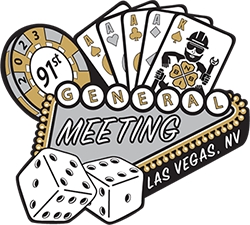
91st General Meeting Speaker Presentation
“What’s New in Weld Metal Additive Manufacturing”
Teresa Melfi
The following presentation was delivered at the 91st General Meeting Monday General Session on May 15, 2023. It has been edited for content and phrasing.
INTRODUCTION: Teresa Melfi is a technical fellow at Lincoln Electric Company. Ms. Melfi is a member of the National Board’s Advisory Committee, representing the welding industry. She has nearly 40 years of experience, with roles in operations, research and development, and international engineering. Ms. Melfi holds more than 50 US and international welding-related patents.
Ms. Melfi’s slide presentation can be found here. Videos from her presentation can be found here.
MS. MELFI: So what's new? I talked to this group a few years ago about weld metal additive manufacturing. And what's new is it's being used now. We'll talk a little bit about the background, some use cases, and get everybody up to speed on where we are today.
One of the things I want to talk about is what does it mean to the people in this room? What does it mean to the inspectors? What does it mean to the chiefs? What does this mean to the owner/operators? What does this mean to the insurance companies so that we're all ready when the time comes when we put weld metal in place of forgings or large castings?
We hear about additive manufacturing, but typically when we're talking additive manufacturing, it's things that you can fit into your hands and carry around. That's not what I'm talking about. These are big parts. They're made of metal. They're extremely large.
So who am I? Those of you who don't know me, I am a welding nerd. I like to say I have more than 25 years of experience, not 40 years, but that’s another story. I've been involved in a lot of codes and standards. And it’s now kind of an alphabet soup of codes and standards that are looking at additive manufacturing and what we should do today.
One of the things that I'm most proud of and most humbled by is being welding advisor for the National Board's Board of Trustees. I work for Lincoln Electric, and those of you who are in welding know Lincoln Electric. We are not a utility in Nebraska. It's a big company with 11,000 employees and $8 billion market cap.
But why are we additive manufacturing? What made Lincoln Electric decide to start building stuff that gets turned into components? It's welding. We've got a bunch of Ph.D. metallurgists on staff. We know all about metallurgy and mechanical properties. We've got a whole slew of welding engineers who know how to deposit metal. We make the feedstock; we make the wire. Every day in one of our plants in Cleveland, Ohio, we draw enough wire to circle the globe twice. We are also involved in automation and robotics. When you walk into Chrysler or Harley-Davidson or John Deere and you see those big welding setups, most of them are Lincoln Electric setups.
So additive manufacturing, is it different than welding or is it really just welding? When we talk about additive manufacturing and you look in some of these codes and standards or you read some of the publications out there, they'll talk about 3D printing. They'll talk about directed energy deposition. They'll talk about builds. They'll talk about feedstock.
When I talk about it, I talk about welding. We talk about GMAW (gas metal arc welding). We talk about GTAW (gas tungsten arc welding). Our parts are weld metal. It's well understood. The property is understood. The NDT (non-destructive testing) techniques are very well understood. If you want to go out and get funding for a research project, you use those additive manufacturing terms. If you want to build something, you use the welding terms. That's what people understand.
Just to get us all on the same page, we start with a 3D print, a CAD drawing. This one is a hollow-bladed propeller that's being built onto a shaft that already exists. This is what the part looks like after it's built. It looks like weld metal. And finally, when it's machined, you can't tell that there was ever any weld metal there.
So, robot and manipulator work is like a choreographed dance. You can see the robot depositing the first weld metal on here. Again, it's depositing and it's doing everything in the down hand position so that there is very little chance of having welding defect. It's not really exciting; it's what weld does. The robots do exactly what they're told. They put the weld metal right where it needs to be with the deposition parameters that you tell them. Welding robots are very, very different from welders. They run 24/7. They don't get hungry. They don't stop for breaks. And you can see, it's a very controlled process.
I said they're being used today, and they're being used in a lot of places. I credit codes and standards that are out there with a lot of use. API has the 20S specification. And 20S is used for putting parts into refineries, some sea applications – anything that's involved with the API book.
AWS has a specification that's used for structural parts. Maybe, it has a tech pump. If you have a chance, Google a YouTube video. An aircraft carrier, the USS Enterprise, was on a timeline to miss its commissioning date because they didn't have a couple of these hold valve clamps for the main door that goes into the nuclear compartment. So, what did they do? They had them build out a weld nut and they installed them, and they're now installed on the carrier.
You may have heard of code case 3020. It was the way you qualified weld metal for additive manufacturing. In the 2023 edition, Section IX now has a whole new section QW-600. It's been incorporated and has the qualification rules for qualifying weld metal additive manufacturing.
Section VIII, Section III, and Section I, B16 all have items that are either in ballot or on the table that will allow the use of components made out of weld metal in those applications. NBIC has a committee going, ABSA, TSSA – everybody is looking at how to codify this so that we don't have to essentially reinvent the wheel with data every time we want to put one of these in. But weld metal has been used for decades. Walt Sperko wrote a little paper about it, about how it's used in the nuclear industry, and how it's been used for 20, 30, 40 years. If you go to his website, sperkoengineering.com, you can download his paper.
But the fun part is how is it being used? Where is it being used? When we started off, the materials were being used for prototypes. They were used for tooling; they were used for things where it wasn't safety critical. And then it moved into machinery. Think about big gears, compressors, places where things wear out and you might not be able to get them back in.
This is a pretty simple one, and this was very early on. There was a bearing housing, and the maintenance guy saw it vibrating, pulled it out, and recognized there was a crack in the flange. It was a pre-World War II part. The company was long since out of business. There were no prints, so this had to be laser scanned to create that CAD drawing. Then there were some modifications that had to be made. It had to be printed. The weld metal had to be welded and then machined and put in service. All this happened in two weeks. We couldn't get a call back from a forging house or a casting house in two weeks.
Here's how it went: There's a part that came in on a pallet. It's a pretty big part. It’s actually an assembly, not a part. You can see that there are a couple of flanges welded onto a big old steel casting. The first thing that had to happen is a CAD file had to be created. I think this is groundbreaking technology. This one here is the one that is used in the additive facility for very large parts, because it's really mobile.
You can take it into a welding cell. You can scan a hot part as well as a cold part. And it's used for dimensional verification once the part is printed. It's just difficult to measure everything you need to measure without something like this. If I had the sound on, you'd hear a little beeping, because he's getting audible signals of what needs to be scanned and what's already been scanned.
They make a lot of different brands of these. Some of them look just like PMI does. They're very small, handheld, and we're seeing them being used in a lot of situations. People will go into their spare parts inventory or into their factory and start scanning things to make sure that they have prints for things that may fail.
On the screen, the print is being created as he's scanning. And once the scanning is completed, it goes to the engineers who take that CAD file and essentially touch it up so it can be printed. There’s some scaling on the bottom part, and you can see the crack. The engineers have to clean it up because we don't want the robot printing this with a crack in it. This is the very end portion of the bearing housing being printed. You get a little bit of an idea of scale on this. This is a picture of it still chucked up right after it was printed from a couple of different angles. I think it looks like a work of art, but it's what the computer told the robot to do to build this shape in a position where it's a very safe way to build it because everything is done in the down hand position.
You can see by the way the weld metal wraps around that sometimes it was built this way, sometimes it was built that way, and in some cases, it was woven a bit. Old part, new part, and in this case, not everything had to be machined. You can see that just the bearing surfaces and mating surfaces were machined, and holes were drilled and tapped. Then it was put into service with some of it just as it was printed.
These are fairly large parts. On the left-hand side, this was a blade that goes into a mixer, and it fails because of overheating. It was typically gun drilled. And because it was printed, the designers were able to modify the CAD drawing so that conformal cooling channels were put in there giving it a whole lot better cooling, a lot less failure rate. That one is about 1,000 pounds.
The one on the right that the guy happens to be scanning – checking the dimensional accuracy of it – is a high-strength low-alloy steel. I think it was 100 ksi steel. It was about 8,000 pounds, and it took six weeks to print. That is a big piece with a lot of metal in it. And it sounds crazy – six weeks to print. Why would you do that? Well, because a forging would have taken a minimum of six months.
This one might be a little bit more up the alley of the people here. This is a 617 nickel alloy. It was a pressure retaining part – high-temperature service. And Robert Rettew from Chevron and I and one of the guys from stress engineering co-authored a paper. I'm only pulling out about six slides from this paper. If you want the whole thing, let me know and I will get you in touch with Robert because it's really a cool case.
This was a refinery. They were chasing the cracks and found that they really were not repairable. The service requirements were 1,500 degrees Fahrenheit, 300 psi with a design lifetime of 20 years. The 800H was welded together with 617 weld metal.
Chevron and the designers were comfortable making a new part out of 617, which is a little bit stronger. They didn't take advantage of the strength and the design. They used the same design but built it out of the 617.
The 3D printing was used to deliver the parts in four weeks. They were installed and saved a significant amount of downtime. I think there were three of the headers, so the pieces on the upper right, three of those and three of the one you see scanned. While we can't say exactly where they were installed, you can see a picture of them as installed on the bottom right. You can also see that they were able to install it exactly as printed. They didn't need to do full machining. That one looks like weld metal in service, where in many cases if they have to do machining, you'd never know that was weld metal.
So how did they do this? They started off with the ASME 3020 code case now called QW-600. And you're all used to welded qualifications. Welding qualifications are much tighter when you're qualifying additive weld metal because you have to qualify the lowest heat input in combination with the lowest cooling rate with the lowest interpass temperature. The highest heat input, in combination with the highest interpass temperature, the thinnest and the thickest part, and you’re literally building a box around these qualified procedures. Remember, this is being done by a robot so the data from the welding can be guaranteed to stay within that pounding box, giving you a lot of confidence on what your mechanical properties would be when you finally build this part.
These are the qualification values they got using that QW-600 of code case 3020. They hadn't done this before. And they were using that API 20S specification so they had an extra part built. They took samples out of it in several different directions and in places where they thought it was likely that there might be an issue like where the saddle went on and weld metal curved from one to another.
This is what it looked like after they took it apart. It about broke the heart of the guys who built this to see this all chopped up like that. And this is the tensile testing from there. For those of you who have photographic memories and remember what the code case 3020 numbers were, all these are within that bond of what the code case 3020 numbers are. These are being used a lot. This code case is used quite a bit in the industry now, and we're finding very, very good correlation between what you see if you do a sacrificial part like this and what you have in code case 3020.
With tensile testing, it doesn't matter what direction it's in. I'm not even sure how to say what the X direction or Y direction or Z direction on something that is constantly being turned, but the material is very isotropic. And they even did some accelerated creep testing. Obviously, some of this was done after it was put into service, but they were very happy with the creep properties in both directions.
What does this mean today? Piping systems might already contain this material. Back in about 2015, there was an interpretation that was sent about B31.3 that asked if you could use additive manufactured parts to replace components or replace piping in a B31.3 application. And the answer was, yes. You just treat it as an unlisted material. This is already approved for B31.3 use. They're installed by welding. Obviously, the weld metal is very weldable. The weld metal now in the latest version of Section IX of 2023 is also given P numbers, so it makes it transparent and easy to use. Section VIII had a code case going. Section III has a code case going. You know how the code world works. They are hoping to have the Section VIII code case by the end of the year. I don't know whether that will happen, but it's moving really fast in terms of code years. Code years are kind of like dog years. This is breaking all the code year rules. It really is moving quickly.
But the weld metal part is treated as a material. It's not a component. It's a material. Think of it more like a forging. It has to go to someone, and they have to do all the testing on it – whether it requires a burst test, whether it requires machining. It looks just like a forging, except the MTR is much more extensive. The front page of it looks like a normal MTR, but because there's so much data behind it, it ends up being several pages of data that goes along with it. The part stamping and the testing wouldn't change. If you think about a valve manufacturer making big valves and they need some parts built for that, it then would go to the valve manufacturer who had the machine up, put the internals in and stamped it.
We don't know when the code cases are going to happen. This would be incorporated into code, but I would fully expect to see some requests for state specials. There’s just such a need now because the supply chains for these big castings and forgings are so messed up that to get back in business, people are wanting to use this. With those, like what took place with the Chevron project, there's extensive data packages. The designer is very much involved in the whole process. And you would expect to see a large packaging data until the rules are put into the code that kind of let us use this in a more streamline manner.
What can owners do today? Insurers? This does a lot of cool stuff – easier and faster installation. That bearing house was a little project that we happened to document. But if we can combine two or three parts into one, the welders, when they put it into service, only will have to make some simple welds rather than trying to do all the complex stuff that they have to do today. It makes the installation faster and easier.
There is potential to reduce the number of dissimilar metal welds that take place in the field because transition pieces can be built making like to like welds. And there's a lot of cool new designs out there. It reduces material waste because we're starting with a near-net-shape part. There might have to be some machining, but it's a whole lot less. And that whole part consolidation is a game changer in some ways – definitely less inventory of spare parts.
I'll talk a little bit about digital inventory, and that's where a lot of things are going. But the big driver today is time. For new parts, it's reducing lead time. Again, think about that Navy carrier example. The biggest driver today is reduction in downtime because these replacements, these are very large parts, might not be on the shelf.
What can you do? Identify the trouble spots. Work with operations. Work with maintenance. Work with the procurement department. And know what those troublesome parts are – the troublesome materials that they're always chasing the cracks in; the troublesome vendors who never meet their timelines. And then create this digital inventory. Figure out what those parts are and get all the CAD prints put in one place and scan them. Those scanners are widely used. Scan them if you don't have prints so you got those parts.
Look at what you have in inventory and what your maintenance guys would really like to have on the shelves. Set up relationships with additive manufacturers – whether it's Lincoln Electric or another additive manufacturer – and get to know them, understanding what their capabilities are and what you need to provide to them. But more importantly, make sure that the part suppliers do the same because it's all the little things that get us into trouble. It's the bell housing, things like that which go bad and have a six-month lead time. Be ready to move; expect the unexpected. Send prints and material requirements ahead of time for prequalification. Set up and qualify your additive manufacturer.
I can tell you Chevron was in our shop doing a quality audit while we were already printing the part because they didn't have that relationship. It’s not a comfortable way to operate. And provide that qualified vendor list to your suppliers so they're ready to go as quickly as you are. Be the hero; reduce downtime.
That's it for me. I'll be happy to take a minute's worth of questions. Otherwise, I will be out in the lobby on break. Mark Douglas is also from the additive group and would be happy to answer questions as well. One question.
MEMBER: What about the quality of metal for casting and forging – is it better, worse, the same?
MS. MELFI: It all depends on what you mean by better or worse. It's more isotropic so a forging, typically the grains get stretched when you're forging something. And the grains are not stretched so it has the same properties in every direction. It depends what metals you choose. Like the 617 that was used in the Chevron case, it's got better creep strength; it's got better tensile strength; it's got better toughness than the material that it replaced. But if you used a different material, then it would be substandard. That's where this whole code case is going – to make sure that you have at least equivalence with the weld metal than what it's replacing.
MEMBER: Great presentation, Teresa. You mentioned several times the timesaving benefits of additive manufacturing, but once these code cases are in place, as the demand rises, are there enough additive manufacturers to meet that demand? What's going to happen to the forging houses?
MS. MELFI: The forging houses are still going to be busy. When you think about it, if you had everything on hand and you could have a forging done, it's going to be less costly than building it out of weld metal. If you don't have it, you got to get it sooner than you're going to make it out of weld metal. I don't think there's anything that's going to be happening with forge houses. One of the reasons Chevron decided to release this report, and really it's an awesome reporting, is it goes into a lot of interesting things that they did along the way. One of the reasons they wanted to release it is because they want to grow the industry. And they want to make sure that there are enough additive manufacturers around so that they can have a full industry. And from our standpoint, Lincoln Electric is one additive manufacturer. And we're trying to grow that pie so that our slice of pie also gets bigger, but we're happy to help with things like code rules to build the industry. There are – Mark would know better than I would – probably half a dozen that do large metal additive in the world.
MARK: Less.
MS. MELFI: Less. OK. So yes, there's some work that has to be done to grow the industry. Mark will tell you that in his plant he's got a couple dozen robots that are running 24/7 doing that, so there's definitely a demand out there.