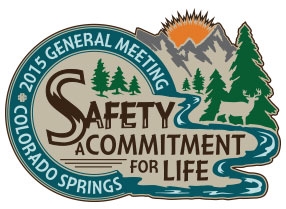
The 84th General Meeting Featured Presentation
A.Thomas Roberts
Making ASME Codes and Standards Smaller:
Small Modular Reactors and Their Needs for Future ASME Codes
The following presentation was delivered at the 84th General Meeting Monday afternoon session, April 27. It has been edited for content and phrasing.
Introduction:
The winter 2015 BULLETIN featured an outstanding perspective on the nuclear industry. It included articles by some of the top experts in the field of nuclear engineering. A. Thomas Roberts wrote one of those articles on the subject of small modular reactors. In this presentation Mr. Roberts examines small modular reactors and the future application of ASME codes. Mr. Roberts has 39 years' experience in the nuclear power industry, including nuclear plant construction, plant operations, and a wide span of engineering management responsibilities. He is an engineering consultant and project manager for MPR Associates in Alexandria, Virginia. He is the current secretary of ASME Section XI Special Working Group, Reliability Integrity Management, that, when published, will become the new ASME Section XI, Division 2.
Mr. Roberts' slide presentation can be accessed here.
MR. ROBERTS:
Before I get started, I’d like you each to think back to your first personal computer or to your first work computer. From my era, that would include the Apple Macintosh II, IBM, and Compaq. It is not important what particular model you may have had. What's more important is to think about the hardware.
The monitors probably weighed close to 250 pounds – at least mine did. In addition to the monitor, there was the central processing unit (computer), a keyboard, and maybe you had a printer, too, and it was all hard-wired together. Now, think about how much physical space this system occupied. Part of it might have gone under your desk, and the rest of it probably took up the top the desk.
Fast forward to today. You probably have a laptop, which is basically self-contained. It probably has a digital-touch screen and a keypad. Everything that the previous hardware had is contained in a small laptop. Now consider this: I’m going to show you what constitutes about 80% of my work environment – my cell phone! Cell phones are an equally functional computer that we hold in the palm of our hand. All of my e-mail is read and responded to on my phone, and with the exception of any kind serious writing, most other work is done on my phone.
This illustration is a logical segue into what I would like to talk about today. For those of you associated with the power industry, most power plants today – whether they are nuclear or fossil – are fairly voluminous, actually behemoth structures. But in the future, the nuclear industry is likely to move away from those behemoth structures. And consistent with that, there is a need for ASME, as the consensus code-writing body, to move with that technology change. And hence the title: Making Codes Smaller.
Just like that computer analogy, other technology is advancing. I have been told -- and I truly believe this -- that miniaturization is really limited only by people. From a technology standpoint, things are going to be made so small that they are going to be, from a human interface perspective, unusable. But there are also advantages to moving towards miniaturization. Literally from an ASME code standpoint, many of the codes, particularly the nuclear codes that have been developed and evolved over the last 30 to 40 years, were focused primarily on the existing technology today.
The title of today's session is “Making ASME Codes and Standards Smaller.” I'm a bit tongue-in-cheek with that because fundamentally, what we are really talking about is a market that's moving forward with small modular reactors, and ASME is embracing those future changes with actions that I will discuss.
What is a small modular reactor (SMR)? For those of you who may not be directly involved with this particular segment of the industry, there has been a lot of confusion. SMRs conjure up images of physical size -- and that is true -- but the truth of the matter is that there is a lot of diversity in small modular reactors. The three main attributes that fit the categorization of SMRs based on the Department of Energy are: 1) Any reactor that produces 300 megawatts or less. 2) It is physically small enough to be transported or manufactured in a shop environment (be able to be readily transported by rail, barge, or typical transport conditions). 3) SMR designs incorporate very advanced safety features that are different than today's existing technology – a particularly important aspect of this session.
From a scaling standpoint, this is a typical containment vessel for a plant today [Refer to power point for images]. You have all seen the iconic images of power plants, particularly nuclear power plants, and they all, for the most part, utilize some sort of containment structure. In comparison to this scaling, this image is one of several current small modular reactors that are being developed actively today. What you are starting to see is that this miniaturization scheme is moving towards being able to physically build an entire reactor system -- not just the reactor vessel; I want to clarify that -- at magnitudes smaller than today's technology.
The term small modular reactor is similar to using the term Xerox. Years ago we all got into the habit of saying “I want a Xerox copy.” Xerox is a name of a company, but it became synonymous with photocopy, even if that photocopy was made on a Minolta printer.
With that in mind, small modular reactors come in a host of different technologies. And they are only limited by their physical electrical output consideration that puts it in the category of being a small modular reactor. In some instances, the SMRs that are currently under development use technology that is common today: light-water reactor technology, low-water reactor, or pressurized water reactor. What is different, however, is that very often the designs have a single vessel that serves multiple functional purposes. With a reactor vessel, one would envision today a steam generator: it's pressurized, but it's all contained in one singular vessel. So that's what brings forth the ability to make these things smaller.
In contrast, another SMR that is currently in development today but doesn't use the single integrated vessel is fundamentally described here. You have the reactor vessel, a separate steam generator, and the surrounding containment on the outside. But again in terms of scale, these are much, much smaller than today's traditional technology. The term small modular reactor, however, is not limited to light-water reactor technology. There are designs currently being put forth that are high-temperature gas-cooled reactors, liquid metal reactors, and molten salt reactors. So if you use the term small modular reactor, you need to realize that you are really discussing a broad spectrum of technologies that are out there.
Right now the list is fairly exhaustive of designers and organizations that are bringing forth designs, and the list is really quite exhaustive in terms of how many different entities are planning to enter into the marketplace. But the bottom line is that the current timeline for these designs, if any portion of them comes to fruition, is basically within the next one to two decades.
Some of the organizations that are further along in development are actually seeking U.S. Nuclear Regulatory Commission (NRC) approval as early as 2016 from a design certification standpoint. And once they pass the design certification application, then it's a matter of bringing it to fruition from the market standpoint.
Another important point is that all SMRs, in varying ways, bring about extremely enhanced safety features that are not present in the current commercial state. When I say current commercial state, I am relating to the U.S., because there are a lot of different reactor types all over the world, but within the U.S., technology in light-water reactors consist of either a low-water reactor or pressurized reactors, but all the SMRs that are currently on board for or moving toward licensing approval employ things like natural recirculation systems, passive cooling systems, and gravity-fed cooling systems for emergency conditions.
I have worked with at least five different vendors and five different types of small modular reactors, and I can state with absolute confidence that all of those designs fundamentally eliminate the need for active safety shutdown components. What I mean by that is while redundancy is a critical component in all reactor designs, SMRs, because of their inherent design features, eliminates the need for such things as emergency core cooling pumps or active valves, and that then leads not needing such things as offsite backup power for emergency shutdown functions. These types of integrated safety aspects are what make, in part, the SMRs very attractive because of their improved safety.
Many of the SMRs don't need emergency diesel generators for shutdown conditions, and many of the SMR designs employ some form of natural recirculation. There are no cooling pumps in some of the designs; it’s pure recirculation conditions. Some of the designs include the use of reactor coolant media such as molten salt or liquid metal that basically upon shutdown solidifies so there is no need to go through separate iterations for core cooling in the event of an emergency. Some of the designs are basically submerged in pools of water such that the pool of water serves as a natural heat sink for shutdown cooling as well. And some of the designs employ subterranean installations that are safer for shutdown cooling conditions. All of the features for all of these designs place the SMRs in a far less vulnerable condition from accident conditions.
Now, I don't know what your viewpoint is of nuclear reactors, but I’ve spent 30-plus years in this business, and from a fatality standpoint, all of the reactors operating today have an incredibly safe safety record when one looks at the generation of output versus the impact of life associated with the industry, even if you include Chernobyl, Three Mile Island, and Fukushima.
Advancing the safety features even more in SMR designs is simply the right thing to do from a safety perspective, because the designs basically don't completely eliminate, but minimize the potentials for natural disaster events, terrorist threat events, and increased overall safety performance. So it's that new technology that is bringing about the interest in the SMR arena.
Okay. We’ve talked about what an SMR is in broad terms, but where does the ASME code fit into this equation? As I have already mentioned, right now there are several SMR designs that employ a single pressure vessel which serves multiple functions. It's a reactor vessel, steam generator, pressure vessel. Because they are a pressure vessel, ASME Section 3, which is for nuclear construction of components, lends itself well to the advent of SMRs in the near-term future. Because some of the designs utilize high-temperature operating conditions, ASME Section 3 NH, Elevated Temperature Service, may be necessitated from a construction and design standpoint. But Section 3, as an existing code and standard, is fairly well suited to facilitate the construction of any new advanced small modular reactor.
As I mentioned before, some of the SMRs have a single integrated pressure vessel. While there is a lot of hardware inside this pressure vessel, it is nonetheless a pressure vessel. It is made fundamentally out of the same materials as other pressure vessels that use Section 2 materials, Section 3 allocations, et cetera. So the construction and design of the components is not as big of a challenge as it is for inservice inspection. And I say that because integrated pressure vessels tend to be very small. Access is difficult, but it doesn't eliminate the necessity for doing inservice inspections. Just because it's difficult to get to is not a justification; rather, we need to come up with new rules that are better suited for these designs. And that is a part of what Section XI is currently working on.
For those of you who have ever opened up Section XI, Division 1, at the very, very back of the book is Division 2. It was originally written with the intent of being used for the pebble bed modular reactor. The pebble bed modular reactor, however, didn't evolve as quickly as anticipated, so Division 2 is just kind of sitting there stagnant. Reliability and Integrity Management (RIM) is a rebirthing of Division 2. The current timeline and milestone objective is to publish a new Division 2 in the 2017 Edition of Section XI.
The real challenge for SMRs is that Section XI, Division I, grew up around the existing technology of today – PWRs and BWRs – because that was the market it was serving. Unfortunately, the Division 1 rules simply aren't appropriate for reactors such as molten salt, liquid metal, and high-temperature gas designs. The new Division 2 is expected to be a technology neutral inservice inspection code, which is to say it won't matter whether it's being applied to a molten salt reactor, a light-water reactor, an integrated single vessel reactor, or a multiple vessel reactor system. In addition to being a technology neutral inspection code, specific appendices are envisioned that will be technology specific that could lend itself well for maintenance and inservice inspection.
The key aspect about a technology neutral inservice inspection code is that it's being built upon what's known as a system-based code. The inherent advantage with system-based codes is that all systems and components are evaluated for their consequences, in terms of safety, for maintaining the plant and overall safety margins. In addition, using the system-based code establishes individualized monitoring. I want to use that term in a very broad sense. For those of you who are in any type of power industry, or even if you are not, there are classic means of inspection and monitoring through nondestructive examination (NDEs), and so forth, that we all have grown used to. Within the new Division 2, inservice inspections may very well be an appropriate methodology for monitoring the safe performance of the component, but not limited to traditional inservice inspections. And I will provide some examples in a moment.
What's also different is that unlike the approach used today in Division 1 – where you have the reactor vessel, a secondary system (like emergency core cooling systems), and then tertiary systems with a stepped approach as far as the types and frequency of inspections that one would perform, starting with the reactor vessel – Division 2 has a much more holistic approach. Here is a brief example, but let me preface it by saying that I’ll sound like a heretic because it took me a while to come to grips with it, too; but there is one design currently being developed in a small modular reactor that, because of the design, the reactor vessel itself could catastrophically fail and it would cause no consequences to the operators, the plant, or the public in general.
However, in the same design, the containment vessel becomes an extremely critical component; right? When one looks at Section XI today, there is this rigorous, continuous inspection of the reactor vessel, and a somewhat less rigorous inspection of the containment vessel. That's why, in part, Division I doesn't work very well, because the designs, unlike a pressurized water reactor or a low-water reactor, has different functionalities and different risk consequences that need to be evaluated on a case-by-case basis for the particular design.
As an illustration, current inservice inspection approach to design construction inspection (but this is not limited to inservice inspection) is that we accumulate margin -- and margin could be from material properties, allowable stresses, regular inservice inspections, et cetera -- and we wind up with an aggregate of excess margin. And that's good, there's nothing wrong with that, except that it may not be appropriate. The approach under the system-based code, which is what Division 2 is predicated upon, is to evaluate what the proper margin is that needs to be maintained for a given component, because its failure would represent some condition that is unacceptable. And then we work backwards, if you know what the margin is, the approach is what is the right margin for a given component over its life. (That's not static; we will talk about that in a second.) And then assign that margin appropriately to the best methodology to monitor and continuously inspect the component throughout its entire service life.
An oversimplified illustration of how the systems-based code works is that you determine the systems, structures, and components for the reactor design to be included in the RIM program. You then evaluate all credible known damage mechanisms that could apply. Once you know what critical damage mechanisms could apply, you then establish the required level of reliability that needs to be maintained for this particular component over its entire service life. Once you have that input, you establish the inservice or monitoring criteria that needs to be in place, and at what periodicity and frequency, in order to assure that those damage mechanisms that may present themselves over time are monitored adequately to preclude them from causing a failure that would be unacceptable. This is an oversimplification of the process, as it is actually a multiple-step process, which is what Division 2 will describe.
Since there is a great deal of probabilistic approach to this type of methodology, all the designs (since they have no track record), need to establish a level of certainty to assure that there is competence in the methodologies and approaches to be used for inservice inspection activities. Once this is bundled up, you establish the specifics for each system, structure, and component throughout its service life with a given periodicity to maintain reliability. That set is a living program.
About 40 years ago, Alloy 600 was considered the premier material for dissimilar metal welds. In the nuclear industry, Alloy 600 in pressurized boiler reactors has cost millions of dollars in efforts to remediate because it wasn't as good as we thought it was. To that end, the RIM process is a life-cycle process. Once you establish the initial criteria for a given system, structure, and component and what the appropriate methodology for monitoring it will be, and then continuously monitor the input and feedback to make sure that all things we felt were necessarily important are being addressed. And if not, then we modify the program in a life-cycle management perspective.
One of the advantages is that the RIM process really becomes an aging management program. It's a living program because it's constantly being fed back with results that the owner/operator of the facility will need to integrate into their DNPs. Similarly, a Deming Cycle chart defines the condition, then you plan, you do, you check, and then you act. It is “living” criteria. And if during the course of the operation of the system, structure, or component something is found ineffective, you go back and correct and adjust accordingly. Like the risk-informed technologies that exist today, the RIM process uses the very same philosophical approach. It's a constant, living program that is fed with inputs from operating experience and information that is gleaned from the course of events over the life cycle of the component.
One point I wanted to touch on today relates to the work of the National Board. With the advent of RIM, there are some pretty significant changes that authorized inspection agency personnel, particularly authorized nuclear inservice inspectors, are going to be facing. Under the current Division I rules of Section XI, inservice inspections were developed in a deterministic approach, and, as such, most plants today operate on what's known as a 10-year inservice inspection interval. So in the first 10 years, you perform “X” number of inspections rather prescriptively within the inspection period, which is usually three and a third years (you complete some percentage not to be exceeded by some other percentage), and it's pretty much a cut-and-paste type of approach. It's not wrong, but the problem with this approach, as I mentioned earlier, is that some of the challenges of using Division I, Section XI, don't fit the SMR designs.
For example, in the inservice inspection world, the 10-year inservice inspection cycle is predicated upon a typical fuel cycle of 18 to 24 months depending on the plant. There are some SMR designs that have anticipated fuel cycles of four years. If you try to put a 10-year inspection cycle into two fuelings because of a four-year fueling cycle for the design, it doesn't work. Some of the changes will be differences from design to design within the framework of the RIM program developed for the particular application.
The other thing I mentioned earlier was that some of the classic nondestructive examination methodologies that are currently in use today may not be the most appropriate or the most effective means of monitoring component reliability, and a perhaps better methodology for a particular design would include real-time online monitoring as opposed to a prescriptive exam or inspection done at a particular periodicity. Therefore, when you look at it from a National Board commissioned inspector’s perspective, there are going to be shifts with the advent of SMRs and the use of RIM with any of the advanced reactor designs that are employed.
I already mentioned traditional ISI examinations and NDE methods; ultrasonic testing and liquid penetrant may need to be replaced with more appropriate real-time monitoring for a particular SMR design, which may involve online acoustic monitoring or surveillance specimen testing. I mentioned several designs that may employ detection of leaks and excess temperature for design and construction, which puts that particular SMR design into a creep range. There are no current operating plants today in the light-water technology regime that have to deal with creep. The drop in temperature doesn’t get into that range. The problem with creep is that there aren’t many protective methodologies for doing nondestructive examinations. One of the conceptual approaches that might be employed with RIM is this: just like a reactor today has specimens that are placed in a reactor vessel that look for radiation and brittle, one methodology that might work for a particular high-temperature gas-cooled reactor would be to have specimens that are periodically withdrawn to look more for creep onset.
These oversight activities would be within the purview of what authorized nuclear inservice inspectors would get involved with. Because of the relative compactness of some of these components, rather than doing periodic leakage inspections (visual inspections), a better approach is to look for active leakage measurement systems. With the advent of SMRs, these are the types of activities and roles authorized inspectors are likely to become involved with.
It is clear that with the diversity of SMR designs coming into the marketplace, the individual RIM program (inservice inspection program, if you will), is going to vary with each design. The methodology of monitoring will vary with each design. The periodicity of monitoring will vary with each design. And because of this, ANII inservice inspectors are going to need to be familiar with the particular RIM program (the particular SMR design), to know and be able to carry out the roles assigned to him or her for what constitutes the appropriate RIM criteria for a particular SMR.
It should be pretty obvious at this point in time that the RIM programs for one design may not be appropriate for another reactor design. This is quite appropriate in order to retain the required safety features. But it means that Authorized Nuclear Inspector Joe and Authorized Nuclear Inspector Bill, who are colleagues today, may be able to go from plant to plant to inspect a PWR on one day or a BWR another day and look up the rules in the code to determine what gets inspected when and what the periodicity is. But in the future, this may not work. There will be some individualized knowledge required for each particular SMR design. Now, if an inspector goes to another comparable SMR, there will be some similarity. But if they go to a totally different SMR, it is going to require some individual familiarization, and I call it rebriefing of what their roles will be.
The bottom line is that all of the inspection methods, surveillance, or monitoring criteria that would be applicable to a specific system, structure, or component will be completed in accordance with a RIM program developed specifically for that design, and as such, that's where the role of the inspection agency is going to change somewhat from today's approach.
In summary, SMR is a huge acronym that covers a waterfront of different designs, and the only thing that is “similar” in SMR designs are their megawatt output, that they fundamentally could be easily transported, and fundamentally can be shop fabricated. That's that broad brush perspective. SMRs are reactors, but the way they work, how they work, and the things that are intrinsic to keep them safe will be slightly different depending on the individual design.
For the last couple of years, the ASME code has been working to address these treatments. The Special Working Group RIM is nearing the point where it will move the new Division 2 forward for codification. Division 2's approach to SMRs and ISI activities is to make the scalable induction that is necessary to accommodate the unique designs of these systems, structures, and components; but still assure that the SMR design, no matter what the design may be, is effectively monitored and evaluated over its life cycle to assure safety.
As with any other technology, ASME is moving alongside technological advances in the nuclear industry, and the nuclear industry at large, including the National Board, will also need to make adjustments to accommodate these advances. But in the long run, the shared objective and goal, whether it's from a code standpoint or a National Board perspective, is to assure the long-term safety reliability. How you do that may change, but the underlying standards that have existed within the purview of the National Board hasn't changed and won't change.