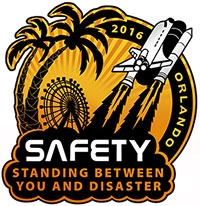
The 85th General Meeting Feature Presentation
Vance Murphy
Statistical and Loss-Based Training
The following presentation was delivered at the 85th General Meeting Monday afternoon session, May 9. It has been edited for content and phrasing.
Introduction:
Statistical and loss-based training has been a topic in our industry for years. Vance Murphy has been a risk engineer for over 30 years. He started his career as a nuclear machinist mate in the United States Navy before going on to work for Chubb Insurance in New York City. Following a 13-year career at Chubb, he left to go to Zurich Insurance, where he does inspections, risk assessments, and training. Mr. Murphy has traveled extensively throughout the Americas and has witnessed the aftermath of a wide variety of boiler and machinery explosions.
Mr. Murphy's slide presentation can be accessed here.
Mr. Murphy:
Fifty thousand years ago, man got his tribe together, brought his plan, started a fire, and told stories. He told great stories. These stories did more than entertain. The stories passed on knowledge to the next generation so the plan itself would survive.
Somewhere along the line somebody got the great idea of calling this mandatory training and took all the fun out of it. My story doesn't start that far back. It starts about 14 years ago when a large company came to us and said, “We are having seven to ten boiler losses a year. How can we prevent this? We want to do training.”
Our first question was, “What kind of accidents are you having?” Their response: “We don't keep that material.” And we said, “Why don’t you keep that material?” And they said, “Well, we have so many plants and they take care of their own stuff. We don't look into it.”
The company was a new account and we had no claims information to go by, so what did we do? We went to the National Board website and looked at the National Board Incident Report to gather some statistics. We saw something very interesting: if I put an operator in a room and gave him basic training, and then beat him heavy on a low-water cut-off, I can reduce 80 percent of the losses.
Fantastic. This company went for it wholeheartedly. So I said, “Okay, first of all, we are going to start this training, but we are going to do it repetitively.” Because training is valueless if you do it once; you have to do it again and again and again. I said, “Let's do this every year.” And then I realized with the numbers of people we were dealing with, that a year was totally impractical. So we went to every five years. And they are saying, “Okay, this worked out well.” We went back and started writing two courses, one for the junior guys and the new guys, and one for the more senior operators, and they said, “No, no, no, no, no, we want to put both of them in the same class together.” And we said, “Wait a minute, how do you do that? How do you teach math to children?” You put the kindergartners who know nothing in this class, and you put the college-educated kids in this class. Well, they were putting them all in the same classes and teaching them AP math. So what did we do?
First of all, we went back to basics, because the new guys needed the basics. But what was very interesting was that the senior guys loved it. Why? Because they were so out of touch with the hands-on operation of the boiler, it was a refresher for them. It renewed their knowledge base.
The other thing we found that amazed me with the senior guys is that I didn't teach to them; I taught with them. I didn't give them the information. I would always start with a question: how many people here have over 20 years' experience, and they would put their hands up, and I would tag them. And my questions to them would be, “How do you do it in your plant? What is different? What am I doing wrong?” It became a roundtable discussion, and they really embraced it.
Safety is never final; safety is never frivolous, but it can be fun. Why? I think back to almost every class I had in school. At one time or another, the teacher walked up to me and said, “Mr. Murphy, do you think I'm here to entertain you?” I said, “Well, yeah.” Why? Because if you are entertained, you are engaged. If you are engaged, you are learning. If you are learning, you are retaining it. So have fun with it.
One way I have fun is that I give a couple of examples. One is Midnight Bob. Everybody who goes to any plant knows Midnight Bob. Midnight Bob is the guy in a dirty set of coveralls with channel locks and a crescent wrench in his back pocket. Every nut he looks at, it's either rounded off or it's got teeth marks on it. He's the guy that walks in after you spent $1,500 tuning up your boiler, and he adjusts the linkage just a little bit because he knows better. He's the guy that takes the chemical treatment pump and turns it from six to nine. Why? Because he knows that six is better than nine. And I look at the class and I said, “Now, I want you to realize something. If you don't know Midnight Bob, you probably are Midnight Bob.” We use Midnight Bob as the foil for the rest of the class, and it lightens up the mood.
But one that hit home and sent chills down my spine was when I asked the class, “Who here can't identify a boiler from a coffee pot?” And we get three or four kids who are in the industry, and they don't know. And I go to one or two of them during the break and say, “Do you mind if we use you? We are not going to make fun of you; we're just going to put you on the spot.” And they usually say, “Sure, no problem.”
We end by doing disaster training, and we put the kid in the boiler room, and we have a slide, a video, and we put him under pressure by setting up a scenario and asking questions: We have a low-water condition. What are you going to do? “I'm going to turn the boiler off.” Okay. Now you find out that Midnight Bob turned the feed pump off. Are you going to turn it on? “Yeah, it's a low-water boiler.” And I said, “Congratulations. You are the first person at the rally point in the parking lot. Second was the boiler itself, because it exploded and blew your body out there. Everybody else is going to make it out when the fire alarm comes on.” And everybody gets a kick out of it, they laugh.
About six months later I was in the same town doing a claims audit for a low-water condition, and I interviewed the person who was operating the boiler. I didn't realize at the time, but it was the same kid. He walked out and said, “I came around the corner and that boiler was red hot. I shut it down and isolated the water, because –” and then he looked at me, laughed, and said – “I didn't want to be the first one in the parking lot.”
It didn't hit me until I got back in my car that that little bit of comedy imbedded in his brain. That little bit of comedy saved that company hundreds of thousands of dollars in extra damage, but more importantly, that little bit of comedy probably saved that kid's life.
So what else do we do? Well, once every five years isn't enough so we decided to make a minute of training. And our thought process behind it was that kids will watch a cat playing the piano for a minute and a half on YouTube, so let's make a safety video that's a minute and a half long. It wasn’t expensive. We took a digital camera and software from the internet and we made them for nothing. The videos are basically how to do a low-water cut-off, how to test a safety valve, how to test a fire-off. And now every time they have turnover, they have what they call a minute of safety and they review one of these videos or they do another thing, but it's become part of their training.
Every manager out there at the end of your review says, how many locations did you do this year? How many stops did you make? That's the wrong question to ask a safety person. The question you should be asking your people is how many lives did you save this year? Because what we did in this location is we charged our inspectors, not to go in there and run in and look at the boiler and run out; we gave them extra time to watch these guys operate the boiler. And if they were doing it wrong, we would teach them the right way; sit down with them, answer their questions. While the boiler is open for an internal, show them the parts, talk to them about how to do a good cleanout, spend time with them, and give them instructions.
What was the end result of all this? They went from seven to ten boiler losses a year down to one or two a year, and we had two or three years where we had none at all.
Over a 14-year period, we trained over 4,000 of their operators, some of them coming back two or three times, and we reduced losses by 80 percent. What did it mean to this company? We saved them over a million dollars a year in mechanical losses, not including the losses from business interruption and the loss of equipment -- or loss of time.
This allowed their upper management to look at training and say, we are going to continue to invest in that. There has never been a question in the 14 years of investing in the training, and it continues today.
So I want to leave you with two things. I want to leave you with a story and then I want to leave you with a challenge. My grandmother used to make tomato ketchup. If anybody knows what it is, it's absolutely delicious. We would go over to her house and we would ask her how she made it. “Well, that's my secret. Just come on over and have some.” She never taught anybody her recipe. Now she’s gone. What was her legacy? It was 20 jars of tomato ketchup. Her legacy, had she taught one person her recipe, could have been passed on to my child, my grandchild.
I want to leave you with this challenge: start a fire, get your tribe together, and tell great stories. If you are not the kind of person that can get up here and teach, that's okay; mentor somebody. When you are going out to that big risk that you know the new guy has never seen, take him with you and show him all the little tricks that the other guy showed you. Pass on your knowledge. Thank you very much.