What is the Best Welding Process?
Jim Worman
Senior Staff Engineer
National Board
Category: Design/Fabrication
Summary: This article was originally published in the winter 2013 National Board BULLETIN. (4 printed pages)
Quite often there is debate among welders as to what is the “best” welding process. In reality, the best welding process depends on a few factors: application, cost, and required quality level. The application involves considerations such as the material, welding position, and location.
The cost of welding is generally measured in pounds of deposited weld metal per hour. The cost of labor per hour is normally a fixed cost that is independent of a particular welding process. The required quality level is a function of the codes and standards to which the product is being built, as well as the customers’ requirements.
There are basically five common arc welding processes used in boiler and pressure vessel fabrication:
- Shielded Metal Arc Welding (Stick)
- Submerged Arc Welding (Sub-Arc)
- Flux-Cored Arc Welding (Flux-Cored)
- Gas Metal Arc Welding (MIG)
- Gas Tungsten Arc Welding (TIG)
Each process has advantages and disadvantages that can help determine the most suitable welding process for a project. The following is an overview of each process for consideration.
Shielded Metal Arc Welding (Stick) is the most popular welding process. It is the most versatile and uses the simplest equipment. The small light electrode and holder can be used in very tight places or reach several hundred feet away from the welding power supply.
Even though the equipment is inexpensive (starting around $300), the overall cost of using this process can be high. This is because the deposition rate (pounds of deposited weld metal per hour) is rather low, typically around two to five pounds per hour. Since the typical consumable electrode is only 14 inches long, the arc is continuously stopped to put in a new electrode. This creates down time, stub loss, and overall inefficiency, which drives up the cost.
The quality of stick welding can be very good but requires skilled welders. The heat input is typically low, which gives a fine microstructure in the weld metal. This produces very good mechanical properties; however, the slag that protects the molten weld metal from the atmosphere can produce slag inclusions if not cleaned properly between passes and at the stop and start of each weld. There are many stops and starts in large welds, which quite often are where defects are found.
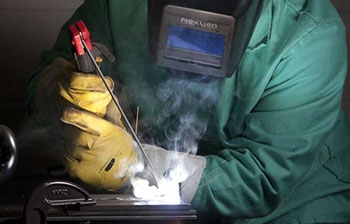
Shielded Metal Arc Welding (Stick)
Submerged Arc Welding (Sub-Arc) is generally the least expensive welding process, but the equipment can be expensive. Since sub-arc is normally an automatic or machine welding process and can only operate in the flat and horizontal positions, a good deal of money can be spent on carriages, turning rolls, manipulators, welding heads, and power supplies.
The high amperage (over 1,000 amps) of submerged arc welding can achieve good penetration and high deposition rates in carbon steel plates. Sub-arc can deposit over 100 pounds per hour, with as many as five wires going into the weld puddle at the same time. This is where big cost savings are achieved.
However, along with high productivity come several limitations. Sub-arc can only be done in the flat and horizontal positions because of the granular flux and fluid weld puddle. The high heat inputs associated with high amperage tend to make large grains in the finished weld metal. The large grains and some micro-inclusions from the slag system tend to create lower mechanical properties than can be found with some of the lower heat input processes, but they can still be quite good.
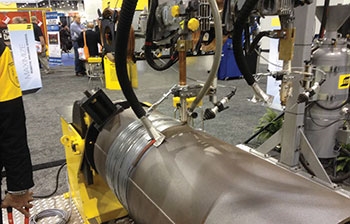
Submerged Arc Welding (Sub-Arc)
Flux-Cored Arc Welding (Flux-Cored) is probably the most diverse arc welding process. It is divided into two main categories: self-shielded and gas-shielded. Self-shielded is generally used outdoors and where high quality mechanical properties are not necessary. Gas-shielded is generally used in indoor manufacturing shops where higher-quality mechanical properties are required.
Gas-shielded is the most popular of the two processes and uses an external supply of shielding gas. Generally, CO2 or a mixture of 75% argon/ 25% CO2 is used to protect the arc. Typically, gas-shielded flux-cored arc welding has cleaner weld metal and better mechanical properties than self-shielded wires.
Large-diameter wires (3/32-inch) can produce a deposition rate of up to 21 pounds per hour and get good penetration. They can only be used in the flat and horizontal positions. Small-diameter wires (.035, .045, and 1/16-inch) are excellent for welding out-of-position. They produce the highest deposition rates and quality of any of the all-position processes. They can deliver 10 pounds per hour welding vertically and overhead.
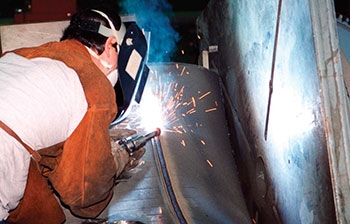
Flux-Cored Arc Welding (Flux-Cored)
Gas Metal Arc Welding (MIG) has four different operating modes (droplet transfers): short-circuiting, globular, spray, and pulsed. The current level, voltage, and the oxidizing potential of the shielding gas determine the operating mode.
Short-circuiting transfer is used in CO2 shielding at relatively low current levels. Consequently, short-circuiting has very low heat input and penetration. This can be good to control distortion on thin sections, to fill gaps, and to weld over contamination. The fast-freezing puddle allows it to be used in all positions. Short-circuiting should not be used on thick sections or “lack of fusion” may occur.
Globular transfer is a higher-current version of short-circuiting. In globular transfer, the arc does not actually go out as it does in short-circuiting, so there is higher heat input and better penetration. It will operate in 100% CO2 or a mixture of argon and CO2.
Spray transfer commonly uses a gas mixture of 98% argon and 2% oxygen. A current level higher than the transition current is also required. Spray transfer uses a high current level and therefore has good penetration and high deposition rates. In the spray mode, 1/16-inch wire can deliver good penetration and a 14-pounds-per-hour deposition rate. Because of the higher heat input and more fluid puddle, spray transfer can only be used in the flat and horizontal positions.
Pulsed transfer is a combination of spray transfer and globular transfer. There is a low background current and a high pulse current. The high current produces a spray transfer and then the welding machine drops the current to the background level. Overall the heat input is lower than spray transfer, so it can be used to weld out-of-position. But the heat input is higher than short-circuit, so lack of penetration is not a problem. Since the arc is completely covered by shielding (as with minimal oxygen content) and there is no slag system, the mechanical properties of the weld metal are generally very good.
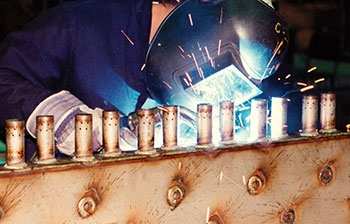
Gas Metal Arc Welding (MIG)
Gas Tungsten Arc Welding (TIG) is probably the highest quality and most expensive of the arc welding processes. It is generally performed manually; however, there are some automatic applications. A good welder can deposit ½ pound of weld metal per hour at about 1-to-3-inches-per-minute travel. Since the travel speed is slow, the heat input can be relatively high per inch of weld, giving good weld metal fusion. But this can also cause distortion in thin sections.
Since manual gas tungsten arc welding operates at relatively low amps and volts, and cold filler metal is added to the puddle, the heat input per deposited weld metal is low. This gives finer grain size and much better mechanical properties than other processes. Since there is no flux, there are no micro-inclusions to lower mechanical properties. Pure argon is generally used as the shielding gas on carbon and stainless steels, so the oxygen level in the weld metal is very low, which produces excellent mechanical properties.
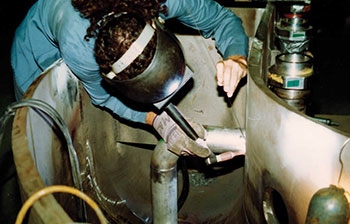
Gas Tungsten Arc Welding (TIG)
Which is “The Best”?
There are pros and cons to each arc welding process. Each can produce high-quality welds; likewise, each can produce defective welds if not operated properly.
Generally, the processes with gas shielding have more pure weld metal and better mechanical properties. The processes with fluxes are easier to use, but can have micro-inclusions, higher oxygen levels, and lower mechanical properties.
And so, depending on the application, desired cost, and required quality level, any of the above processes may be “the best” as long as they are used properly.